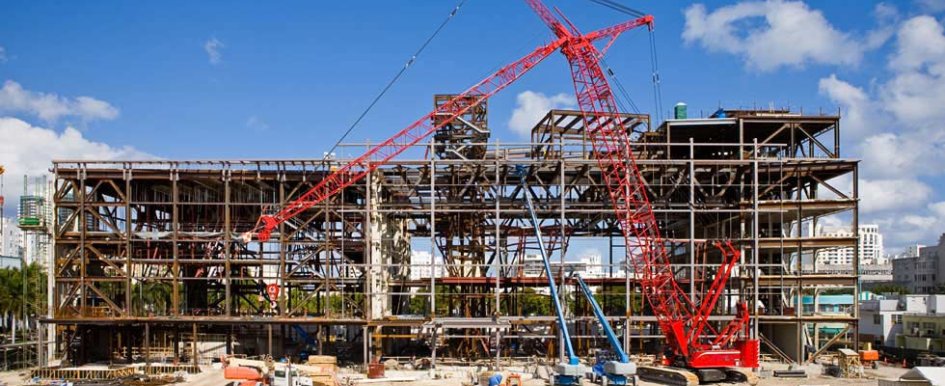
“Escalation, escalation, escalation,” is all I hear from clients and colleagues as they leave their Zoom screens and return to conferences and conventions. In summer 2020, the world saw how COVID-19-related disruptions affected global production and the supply chain.
Just one year into the COVID-19 pandemic, developers were looking at 20% price increases and no end in sight for supply chain disruptions. To further compound the pain, at the end of 2021, the inflation rate in the U.S. stood at 6.2% — approximately four times the market benchmark — and construction materials were up 23% over a year. Then, on Feb. 24, 2022, Russia invaded Ukraine, sending a new set of shockwaves across the construction industry.
Further compounding the crisis, in response to Russia’s unprovoked aggression against Ukraine, the U.S. imposed wide-sweeping sanctions that will affect every aspect of Russia’s economy. U.S. and multinational corporations responded by ceasing Russian operations.
Russia is a major aluminum producer, is the third-largest nickel producer globally and has 10% of the world’s copper reserves, which had already seen significant price increases topping 33% in 2021. The price of copper hit an all-time high of $10,070 per ton on the London Metal Exchange on March 7, 2022. Furthermore, Russia supplies one-third of Europe’s oil and natural gas. Ukraine is a top producer of iron and mercury and has the third-largest shale gas reserves in Europe. A week into the invasion, crude oil pressed sharply upward to $130 per barrel.
The effects on the construction industry were immediate. The higher price of oil and gas immediately increased the transportation price of equipment and supplies.
The worldwide shortage of steel and copper will put an increased burden on an already-stressed supply chain. Although contractors in the U.S. are busier than ever, procurement of materials is becoming more challenging, creating uncertainty in project pricing and schedule.
For example, roofing contractors are particularly hard-hit as basic supplies such as tiles and insulation orders take a year to fill. Steel subcontractors are walking away from projects bought out earlier this year because they cannot fill orders at the prices quoted a few months ago. More and more subcontractors are willing to take the calculated risk of anticipatory breach of contract than proceed with increased project costs. Contractors should consider ways to mitigate price increase risk.
1. Contracts Should Include an Escalation Clause
Project stakeholders are now giving serious consideration to price escalation clauses. Contractors are negotiating allowances for materials that are susceptible to price volatility. Contractors should seek to pass on a percentage of the escalation costs to owners. As an incentive to the owner, the contractor can offer to share any cost savings.
Price escalation clauses should identify specific materials that are volatile or hard to procure, therefore providing owners certainty and control over the project price. Contractors should require their subcontractors to purchase materials in advance or lock down the bid prices with their suppliers. Another option to consider is a contingency in bids to deal with fluctuation in material costs.
2. Consider Alternatives to Mitigate Project Delays
Price volatility, supply chain issues, ongoing labor shortages and the lingering effects of the COVID-19 pandemic will certainly lead to delays.
Project schedules should be realistic and anticipate the volatility in getting materials. Owners should also be open to considering alternate or substitution requests or paying for the storage and expediting of materials.
3. Rethink Force Majeure
Force majeure is a legal doctrine that excuses a party from contract performance if faced with circumstances that are not predictable and beyond the parties’ control. The COVID-19 pandemic put force majeure clauses at the forefront of contract and insurance coverage litigation. War and its effects are likely to be considered a force majeure event, however, it is unclear whether supply chain issues that arise from a war half a world away qualify as a force majeure event. Contractors should carefully examine their force majeure clauses and understand how the clause may be interpreted by the governing laws of the project. Force majeure clauses should be rewritten to anticipate the unknowns of current events.
Regardless of when it ends, Russia’s war against Ukraine will certainly have a long-lasting impact. Globalization means that we are not insulated from the effects of regional conflicts. So be proactive, understand the risk and take steps to mitigate and rethink your material procurement strategies.