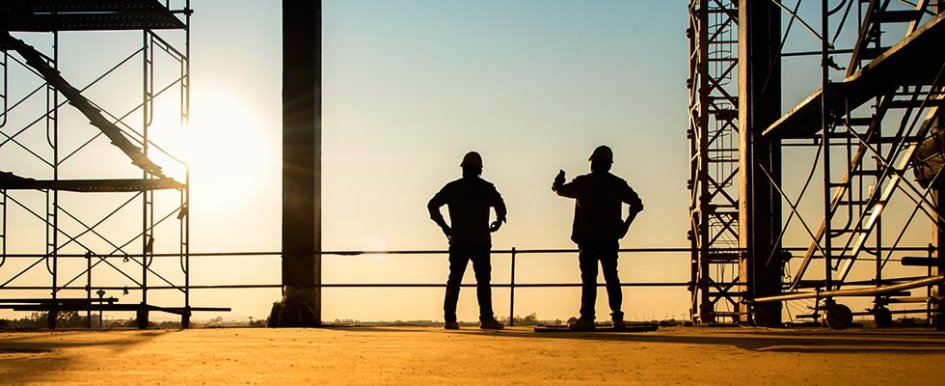
The COVID-19 pandemic brought about one of the most challenging periods in the history of the construction industry. Lockdowns, supply chain breakdowns and financial struggles wreaked havoc, causing existing projects to be delayed and new projects to be restructured. At times, managing supply chain interruptions and trying to keep a healthy cash flow seemed nearly impossible. These factors made planning for future growth more difficult.
Now contractors have a unique opportunity to incorporate the lessons learned throughout the pandemic to be more resilient and profitable in any circumstance. The following will reflect on the most significant pandemic-related developments to affect the construction industry and the lasting impacts they may have on industry practices.
Project Delays
Looking Back
Project delays were a significant hurdle during the early days of the pandemic. With completion deadlines and delay clauses, contractors faced financial penalties and damages where their contracts didn’t specifically state federal shutdowns or pandemic-related disruptions as excusable factors for delays. In fact, contractors bringing COVID-19-related impact claims are having trouble in court. The projects may be back on track, but recouping delay penalties and related legal fees has proven tough.
Looking Ahead
Contractors wary of a COVID-19 resurgence or similarly disruptive event may want to reinforce the language in their contracts to protect against large-scale shutdowns and other major disruptions outside of the business’s control. To date, companies seeking to compel insurers to cover pandemic-related losses by claiming coverage under damage or suspension clauses have been largely unsuccessful. In the future, success compelling an insurer to issue reimbursement might depend on the addition of language specifying coverage for federally mandated shutdowns.
Supply Chain Issues, Material Costs
Looking Back
When countries implemented lockdowns, the shutdown of nonessential businesses caused supply chain issues, which in turn increased material and labor costs. Jobs bid on and awarded prior to the pandemic used now-obsolete pricing, causing reduced margins and profits across the board. With nowhere to pass the cost increases, contractors needed to dig into their own pockets to cover these overages. At the start of the pandemic, material costs for sand, bricks, lumber and cement increased significantly as a result of limited availability. In May of 2021, lumber prices alone had increased six to seven times their annual average, according to Macrotrends. These figures have since returned to reasonable levels. However, these prices are still one-and-a-half to two times their pre-pandemic levels. Not only are material costs increasing, but the cost to land these materials is rising as well. Labor shortages are compounding the issue, with some companies having trouble finding the resources to deliver the materials in a timely manner.
Looking Ahead
Most contractors didn’t have an escalation clause in their contracts to cover the steep increase in material costs. While some contractors were able to renegotiate existing contracts, not all were successful. This led to contractors going out-of-pocket and eating into already razor-thin margins. To mitigate the impact of future pricing volatility, consider incorporating escalation clauses and delay provisions into project bids and contracts.
Larger construction firms went so far as to order excess materials to lock in favorable pricing. Of course, caring for that material requires suitable storage facilities and shipping capabilities. Certain specialty businesses with limited material needs and suitable in-house fabrication capabilities might find this strategy of bulk ordering effective going forward, but equipment costs could prove a barrier. For example, a painting contractor buying paint months or years in advance would need to also be able to mix materials to each project’s specifications in-house.
Labor Shortages
Looking Back
With material prices back down from all-time highs, contractors are attacking their backlogs only to find they’re short of the skilled labor necessary to complete the work. Labor shortages introduce their own issues, including delays in project completion, quality control concerns and increased overall job costs. According to an analysis conducted by Associated Builders and Contractors (ABC), the construction industry needs approximately 650,000 more workers to keep up with the pace of current work. Labor shortages are forcing some contractors that typically perform work themselves to turn to subcontractors. Prior to the pandemic, studies showed that more contractors were leaving the industry than entering, and construction’s aging workforce is a major problem, considering younger employees don’t yet have the technical skills or experience to keep up with demand. It is estimated that the number of construction workers dropped 8% over the past decade. And, with 1 in 5 workers older than 55, senior workers are approaching retirement with no clear indication that younger generations are prepared to step into their shoes. This skill gap was exacerbated by COVID-19 and will persist until younger generations enter the construction industry and gain the necessary skills.
Looking Ahead
In response to a tight labor pool, the industry has taken steps to encourage young people to enter the profession and incentivize existing employees to stay on. That’s driving increases in wages and broader benefits packages throughout the industry. In addition, industry organizations are promoting the benefits of trade school and encouraging companies to develop relationships with high schools, participate in career fairs and streamline hiring practices. Finally, some construction firms are restructuring with hiring and retention in mind. Employee stock ownership plans, for example, are making a resurgence as an ownership structure rewarding long-serving employees with equity.
Financial Struggles
Looking Back
Contractors continue to work through the financial struggles that arose at the beginning of the pandemic. As project delays caused financial strain on contractors, supply chain issues drove up the price of materials, and labor issues created more financial tension than ever before, contractors focused on taking safe cost-cutting measures. Since the pandemic started, there has been a larger focus on balance sheets and cash flow management as companies look to cut unnecessary costs.
To help offset some costs, federal aid was made available to businesses in the form of forgivable loans and tax credits. The most popular of these were the Paycheck Protection Program (PPP) loans that businesses were eligible for as long
as they kept employees on payroll during the pandemic. The Employee Retention Tax Credit (ERTC) was another major aid and allowed qualified businesses up to $28,000 per employee in tax credits. These helped struggling businesses get back on their feet and maintain a healthier cash flow. With this money drying up, contractors are again focused on cutting costs and increasing margins where they can.
Looking Ahead
While programs like the PPP are unlikely to return except under extraordinary circumstances, the 2022 infrastructure bill promises billions in as-yet unawarded construction spending. Some firms are reviewing the bidding requirements for this work to best position themselves for future awards. As budgets are slashed, falling material prices should be kept in mind to avoid unnecessary cuts.
While the last few years have proven difficult, it’s important to recognize that the industry is rebounding, and companies are carrying the lessons of the pandemic forward. Overall, positive long-lasting change appears imminent, particularly for those eager to evolve.