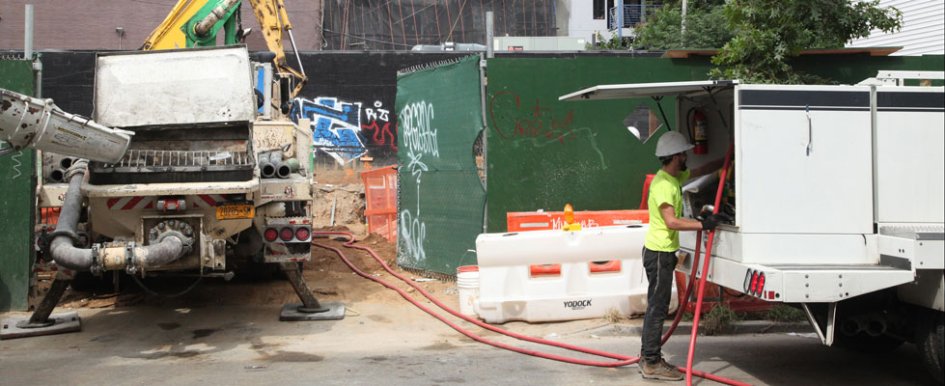
Managing the flow of fuel in compressed, urban environments is a challenge that contractors working in cities face on a daily basis. On many metropolitan jobsites, fueling becomes a juggling act of servicing core heavy equipment, as well as generators, lighting structures and other on-site assets that require around-the-clock energy.
In big cities, the crush of traffic and small jobsites put immense pressure on foremen and site managers to ensure optimal traffic flow of third-party partners—including their fuel provider. The challenge isn’t just space, though.
Optimizing uptime by eliminating process-halting interruptions is also key, and business owners can achieve this by selecting a fueling partner who works smarter to maximize efficiencies.
The following are three tips contractors and construction operations managers should consider for optimizing their fueling and service operation.
1. Stay Nimble
A traditional fueling truck will likely gum up your construction site considerably, so consider a fueling solution that’s nimbler, or could even be dropped temporarily in a convenient area on-site.
Fuel trucks with a large footprint could force work on the site to come to a halt completely, while also causing issues with traffic and parking at your site and nearby businesses. On the other end of the spectrum, a pickup with a 100-gallon fuel tank affixed in the bed isn’t going to cut it either. Making multiple fuel runs each day isn’t an efficient use of time or human resources.
A solution somewhere in the middle of all of these has been a great fit for Ari Simkin, owner of IZE Rentals, of Brooklyn, New York, who uses a diesel solution with a 920-gallon capacity on a truck with a footprint no bigger than a medium-duty pickup truck. This allows him to squeeze onto tight New York City construction sites without disrupting productivity.
“We realized that a lot of big fuel trucks that carry 5,000 gallons of diesel cannot even access the certain points where we needed to fill up,” Simkin said. “And we actually got phone calls telling us that with our new solution ‘only you could fit in to this specific area’ because Brooklyn is so tight.”
Of the logistics, Simkin said, “The big fuel trucks just park and block the whole street. When we’re in front of a construction site, they can’t do that. We have other trucks coming in and out. There are dump trucks waiting. With our new fueling truck we can just sneak in there, fill them up and then go on.”
2. Stay Determined on DEF
When rushing to maximize time on dirty, gritty jobsites, you run the risk of diesel exhaust fluid (DEF) contamination. While the International Organization for Standardization (ISO) standard allows for open systems for storing DEF, many original equipment manufacturers (OEMs) and industry experts suggest closed systems are the most effective.
Closed DEF systems minimize the risk of debris contaminating the DEF, which can cause significant issues with heavy equipment. At its worst, contaminated DEF can cause selective catalytic reduction (SCR) malfunctions, engine derating and damaged equipment that may void the manufacturer’s warranty.
Comprehensive DEF transportation and distribution solutions deploy a two-in-one DEF pump that connects the system directly to a bulk DEF tote with a coupler. The pump then intakes the DEF directly to the transportation tank and shuts off when the tank is full. To distribute the DEF, the user simply replaces the coupler with a traditional nozzle and pumps. These new DEF delivery solutions also eliminate the dreaded task—still employed by some contractors—of filling equipment by hand, with 5-gallon totes that take more time, create more waste and open you up to greater contamination risk.
Colorado Milling is a full-service asphalt contractor that does a large percentage of its work across downtown and metropolitan Denver, Colorado. Leveraging a two-in-one, closed-loop DEF system on the company’s bulk fuel trailer has helped employees maximize efficiency while minimizing the pain of hand-filling their milling machines via plastic totes.
“My millers run DEF, and we top the DEF tanks off probably once a week, and it works out great,” said Chris Vorhies, owner of Colorado Milling. “Now we’re not having to carry 5-gallon jugs in the back of our service trucks. It just streamlined everything. One vehicle can take care of all the equipment as far as fuel and DEF go.”
3. Don’t Take Your Time
Every minute of downtime on a jobsite translates to money lost. On compact jobsites in a big city, that could also mean equipment stopped for refueling, with the domino effect of other vendors being forced to wait or other work being delayed due to a fuel delivery truck blocking the single point of entry.
Make sure you have a fueling and maintenance process that is correctly sized for your operation and won’t cause issues that will have negative impacts on productivity and equipment in the long run. Whether that’s timing your fueling during periods of lower traffic density or abiding by local municipal restrictions, such as off hours for city transportation services, make sure to design your company’s fueling process to maximize your uptime while minimizing external impacts.
Before upgrading to their current fuel and DEF trailer, Vorhies and the Colorado Milling team were spending 10 hours each day refueling across multiple crews. Between battling Denver traffic and using 90-gallon fuel tanks, the process was time-consuming and inefficient. Now, with a larger capacity fuel trailer, Colorado Milling refuels just once daily at 10 a.m., which helps them miss the crush of traffic that comes with having jobsites in downtown Denver.
“Previously, it would take one guy several hours a day per crew, just running back and forth to the fuel station,” Vorhies said. “Over time, my guys got drained going back and forth to the gas station. The efficiency that we’ve gained by changing our process and fueling operation is time. Now I’m only having one guy fuel everything versus one guy per crew accruing overtime doing it after hours.”