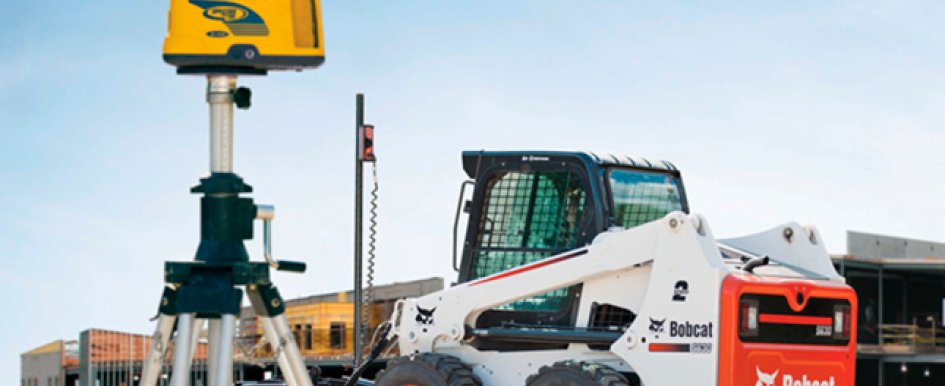
One of the more visible examples of the compact equipment industry's momentum is the development of excavator and loader attachments. It wasn't long ago that attachment catalogs typically started with augers and ended with wheel saws, with dozens of task-oriented hydraulic tools in between.
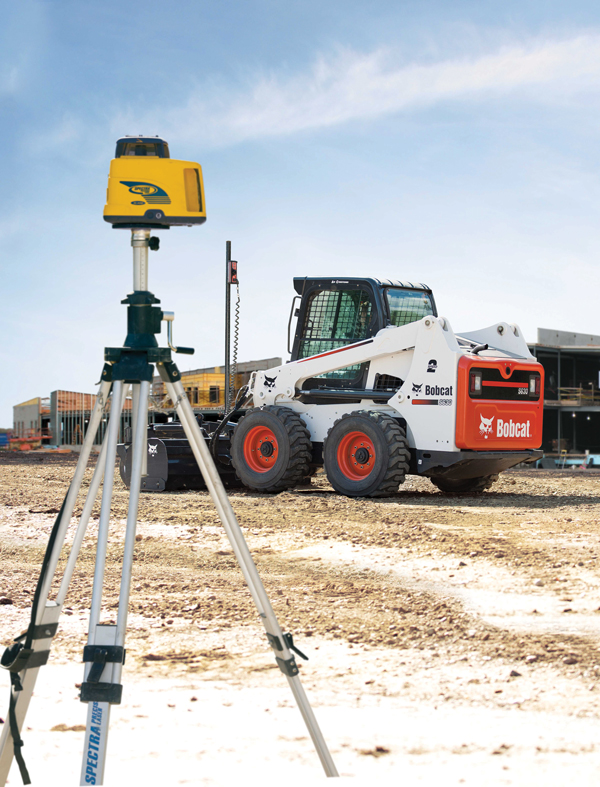
Versatile attachments have always been designed to enhance equipment fleets and assist operators with projects by reducing labor. Today's compact machine operators also benefit from technologies aimed at increasing accuracy in grading and excavating applications and general attachment management. Before the busy construction season arrives, explore some of the innovative technologies you can expect when looking for precision in your next construction project.
Excavators: Grade and Depth Control
Tasks such as trenching for footings or utility lines or grading ditches call for a consistent grade or sustained slope. Grade-control technologies are taking the legwork out of the project and helping operators dig faster and more accurately. The technology is designed to use a series of sensors—one on the attachment, one on the arm and one on the boom—connected to an instrument panel inside a compact excavator's cab to track the precise location of the bucket teeth as the bucket, boom and arm moves. Laser-compatible systems can be calibrated to a specific machine as well.
These systems can offer accuracy within a half-inch, eliminating the need for excavator operators to stop the machine to enter and exit a trench for physical measurements. It also helps to minimize over-digging and under-digging and the costs and time associated with backfilling, compacting fill material and the manual labor required to finalize depth or grade.
Another new offering in the excavation and grading category is a dual function clamp system for compact excavators. Excavators can benefit from one clamp attachment that offers both an adjustable standard tool and reversible grading tool. As a standard tool, the adjustable design allows it to be pinned in positions that provide traditional grabbing performance, or pinned at a point that opens the jaw wider for handling bigger material such as larger-diameter utility pipe, boulders and logs.
The dual functionality of this type of attachment occurs when the tool is pinned in the forward position where it can provide a smooth cutting edge on the bottom of a trench, eliminating the need for a second smooth lip bucket. In this reverse position, the grading tool provides a clamshell function against the bucket, which can reduce manual shoveling requirements on the jobsite.
Loaders: Precision and Versatility
Sonic/slope and laser grading systems are grading attachments that are compatible with loader control technologies. When used properly, these automated grading solutions can deliver grade accuracy within one-quarter inch to provide precision in utility installations and paving projects. When mounted on compact track loaders or skid-steer loaders, the housings of most laser receivers are outfitted with indicator lights to inform the operator if the blade is too high, too low or right on grade. In machines that offer instrumentation, the system significantly increases efficiency because the operator does not need to exit the machine's cab to manually raise or lower the laser receivers or the laser transmitter.
Taking this technology one step further, the development of integrated sonic tracer and slope sensor systems provide an alternative method of automatic grade control on hilly jobsites not suited to lasers. When mounted on a grader blade, these systems provide many of the same capabilities as large road grading equipment does for rough and finish grading. As an integrated system with an instrumentation program, the grade control system is designed to follow the contour of nearly any terrain and eliminates the need for a control panel on the grader attachment.
Management Options
In addition to attachment developments, new innovations in attachment management with multiple functions and controls integrated into excavator and loader instrumentation systems are now available. Attachment productivity can now be intelligently monitored. These systems allow operators to consult their display panels from the cab. Job clocks and cumulative hour meters compute usage on high-output attachments. Owners can also track parameters like bit life, maintenance and total life of an attachment to assist with future purchasing or rental decisions.
Additionally, control panels afford the ability to calibrate auxiliary hydraulic flow rates to optimize attachment operation.
Attachment technology continues to move toward greater sophistication, efficiency and ease of operation. Advancements made in labor-saving attachment designs can translate into measurable efficiencies on the jobsite. Taking time now to understand these technologies could really pay off when your crews are pushed to meet customer expectations and deadlines.