
Serving the construction market is a competitive business. Between bidding against other companies and striving to meet project deadlines, contractors always are looking for ways to boost productivity. The welding operation is one key area where improvements could make a difference. For some structural steel jobs, it may be possible to convert from the stick welding or shielded metal arc welding (SMAW) process commonly used on these applications to self-shielded flux-cored welding (SS-FCAW). The conversion typically involves changing from an American Welding Society (AWS) E7018 stick electrode to an AWS E71T-8 self-shielded flux-cored wire. The self-shielded flux-cored process can offer faster welding travel speeds, in turn increasing productivity, providing greater cost savings and giving companies an edge in the industry. The process minimizes downtime for changing out stick electrodes so that welding operators can spend more time welding.
The Self-Shielded Flux-Cored Process
Strict codes regulate the welding procedures for everything from fabricating components for structural steel erection to constructing portions of a bridge. Under the AWS D1.1 structural welding code and AWS D1.5 bridge welding code, for example, companies must follow the prescribed base metal, filler metal and power supply settings for each given application.
Converting from stick welding to a self-shielded flux-cored process, therefore, requires the requalification of welding procedures for each given project. It also involves updating welding operator certifications.
Companies that make the switch will face downtime for training welding operators the techniques of welding with an E71T-8 wire—often called a T-8 wire—and for operators to successfully complete the certification process; however, both activities are just a matter of business. Welding operators must have their certifications requalified periodically throughout the course of their careers. Transitioning to a self-shielded flux-cored welding process simply facilitates this process sooner.
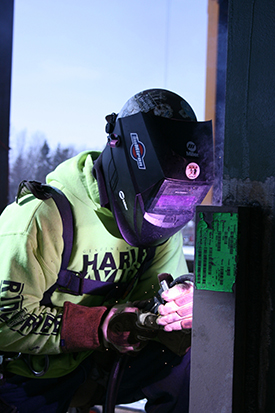
Having the certifications for this process can help position companies for greater competitiveness. Being able to complete the same project faster than another contract bid gives you a clear competitive edge.
Proper Equipment
The transition also requires access to the proper welding equipment (power source). Welding successfully with a T-8 wire requires a constant voltage (CV) power source. This portion of the conversion is non-negotiable—it is critical for welding to code.
One word of caution: Adding a voltage-sensing feeder to a constant current (CC) power source used for stick welding will not suffice. This system is not acceptable for self-shielded flux-cored welding to AWS code D1.1, as it does not react quickly enough to maintain a steady voltage throughout the welding process. Those fluctuations in voltage can lead to weld defects, especially porosity, which can cause downtime and costs for rework, not to mention
potential delays and possible contract fees for missed deadlines.
Get to Know T-8 Wires
The key to using a T-8 wire is to understand its characteristics and operating requirements, its chemical and mechanical properties and how they meet structural steel application needs.
A number of T-8 wires that meet seismic requirements and offer the necessary high-impact strengths for critical code work are available on the market. A filler metal manufacturer or trusted welding distributer can help you make the best selection. Understanding the various portions of its AWS classification is a good first step in becoming familiar with a T-8 wire, beginning with its most basic arrangement, E71T-8:
- E indicates an electrode.
- 7 refers to the wire’s tensile strength measured in pounds per square inch (psi). For this classification, the 7 refers to 70,000 psi.
- 1 indicates that the wire offers all-position welding capabilities.
- T denotes it is a flux-cored wire.
- 8 indicates the usability of the electrode or, in this case, DCEN single- or multi-pass welding.
Some T-8 wires also offer added designations for impact strength, seismic requirements and hydrogen content, each of which contribute to the suitability and usability of a given manufacturer’s T-8 wire for a specific application.
T-8 Wire Operating Characteristics
The allowable voltage ranges for T-8 wire vary according to a given filler metal manufacturer’s formula, the position in which it is used and, most important, the wire feed speed, which directly affects amperage. As a rule, T-8 wire operates at 175 amps or greater, with a voltage range from 18 to 24 V on an all-position weld regardless of wire diameter. Welding operators must weld within the recommended parameters to avoid defects that could lead to
time-consuming and costly rework.
Electrode extension, or stickout, also impacts the manner in which a T-8 wire operates and, again, varies according to the filler metal manufacturer.
Typically, most T-8 wire requires stickout in the range of ¾ to 1 ¼ inches, depending on the given diameter used. The general rule is that a smaller-diameter wire will require a shorter stickout than a larger-diameter wire.
Too short of a stickout can cause the amperage to increase disproportionately to the voltage setting, which can lead to lack of fusion. Too long of an extension causes the amperage to be too low for the given voltage setting, leading to incomplete slag coverage and other weld discontinuities.
To help minimize such problems, always check the specific stickout requirements for the T-8 wire being used. It is also important to maintain the appropriate gun angle and travel speed with a T-8 wire. Doing so helps prevent slag inclusions that could lead to poor weld quality and rework. Specific gun angles vary from wire to wire, anywhere from 10 to 45 degrees, and are determined according to the recommendations of the filler metal manufacturer.
Welding operators also should employ a drag or backhand technique when welding with T-8 wire. As a rule, the presence of a uniform slag line behind the weld puddle is a good indicator that the welding operator is using the proper gun angle and travel speed.
Finally, when using a T-8 wire, contractors must ensure that their welding operators take precautions to protect against the voltage fluctuations that commonly occur on jobsites.
Using a multi-meter or a wire feeder with digital voltage meters can help maintain proper voltage range and desirable weld results.
Maintaining good weld cable conditions and secure connections between the welding gun and the power source is also a good practice.