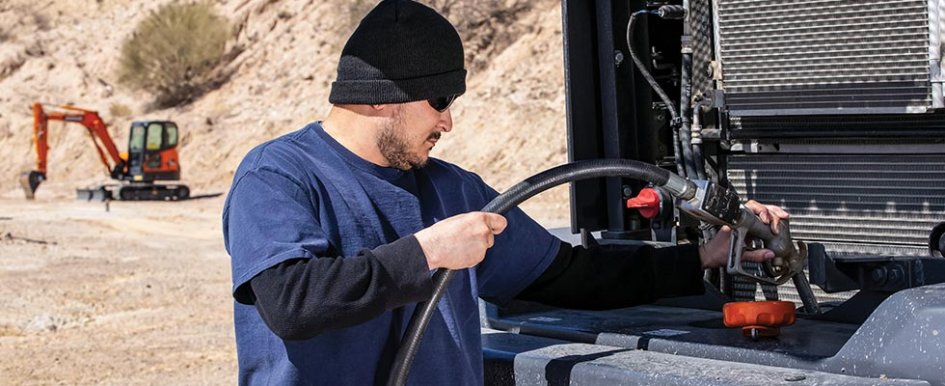
The cost of diesel fuel remains a primary concern for contractors in the construction industry. Fuel costs can constitute a significant portion of operational expenses, particularly on large projects or when equipment operates in less populated areas, requiring longer-distance fuel transportation.
The evolution of nonroad diesel engines has helped with fuel consumption, and manufacturers are also designing dozers, excavators, wheel loaders and articulated dump trucks (ADTs) with cutting-edge heavy construction equipment technologies. These include real-time fuel management systems, automatic engine start-and-stop features, and selectable power modes. These innovations can go beyond fuel saving and reduced emissions — they can also increase equipment longevity and improve efficiency.
Advancements in Technology
Newer technologies on construction equipment can help optimize fuel consumption and improve overall efficiency. Here are several technologies of importance.
Fuel Management Systems
Fuel management systems offer real-time monitoring capabilities, allowing you to track fuel consumption for each machine. You can use the live data to make informed decisions about equipment usage, maintenance schedules and operational practices. These monitoring systems generate detailed reports that break down fuel efficiency metrics, including information on fuel consumption patterns, high-consumption periods and locations of specific machines. They can also be configured to send alerts or notifications based on predefined thresholds. For example, if a machine’s fuel consumption exceeds normal parameters, the system can automatically notify you and your dealer, prompting an investigation into such potential issues as fuel leaks or inefficient operation.
One major benefit is that fleet management systems often integrate with maintenance scheduling tools. This integration allows you to align fuel efficiency with preventive maintenance, ensuring the equipment operates at peak efficiency. Regular equipment maintenance helps prevent issues that can lead to increased fuel consumption.
In addition, fuel management solutions can help with operator training and accountability. By providing actionable insights into equipment fuel consumption and efficiency, they can help you encourage more responsible and fuel-conscious behavior, and contribute to cost savings.
Automatic Engine Start-&-Stop Systems
Also called idle management systems, automatic engine start-and-stop systems are designed to optimize fuel consumption in heavy equipment by automatically managing engine idling. Engine idling is a significant contributor to fuel waste in the construction industry. These systems shut off the engine during periods when equipment is not actively working, such as during breaks, waiting times or temporary halts in operation. When the equipment is ready to resume work, the system starts the engine, so there is minimal disruption to workflow. The systems can be equipped with an option to override the automatic function in situations where continuous engine operation is needed.
In addition to saving fuel, auto idle can contribute to the overall health and longevity of heavy equipment. Reducing unnecessary idling minimizes the stress on the engine, contributing to extended service life and reducing maintenance costs.
Power Modes
Heavy machinery can be equipped with power modes, which are designed to balance power output and fuel efficiency to adapt to different working conditions. The eco, or economy, mode is geared toward optimizing fuel efficiency without compromising overall productivity. In this mode, the engine operates at lower revolutions per minute (rpm) to reduce fuel consumption during less demanding tasks or when maximum power is not needed. This is especially beneficial during periods of idling or with lighter workloads.
Proper training on how to use different modes helps maximize efficiency, extend equipment life and minimize fuel consumption. Your local equipment dealership can help make sure your construction equipment is outfitted with the right fuel-saving technologies.
Evolution of Engine Technologies
Today’s diesel engines in construction equipment are very different from what was on the market even 10 years ago. The advancement from mechanical to electronically controlled engines has made diesel engines significantly more efficient. These systems continuously monitor and adjust various engine parameters in real time, optimizing performance based on the specific operating conditions while minimizing fuel emissions.
Loran McNally, with The A. Johnson Company in Vermont, gives a prime example. The company purchased a newer wheel loader equipped with a more sophisticated diesel engine and fuel systems, and it has reduced fuel consumption “easily by 50%,” according to McNally.
The ongoing development of alternative technologies like hydrogen power and electric vehicles (EV) is becoming a popular trend. EVs operate solely on electric power, eliminating traditional fuel sources altogether, along with the reliance on aftertreatment systems in equipment. Electric equipment not only provides zero-emission operation at the point of use, but also contributes to lower overall energy consumption when the electricity is sourced from renewable or low-emission power generation.
The construction industry is increasingly exploring alternative power sources like hybrid technology, which combines traditional engines with electric power. Hybrid systems allow heavy equipment to operate more efficiently by leveraging electric power during periods of lower demand. For example, electric power may be used for lower-speed operations or during idle times, reducing the reliance on the combustion engine and resulting in significant fuel savings.
Autonomous technology is another notable trend that may lead to reduced fuel consumption because owners will have more control of the machine operation. And this technology can enhance safety by reducing the need for operators on high-risk jobsites. The remote monitoring and control can offer real-time insights into equipment performance and enable quick responses to any issues that may come up.
Autonomous technology is in the works for some equipment manufacturers, and companies are already testing ADTs, wheel loaders, dozers and excavators that can function without an operator in the cab. These machines will have the power to navigate through complex environments and perform a variety of tasks on their own, reducing the risk to employees on jobsites.
From advanced engine technologies and automatic engine start/stop systems to customizable power modes and sophisticated fuel management systems, you now have a diverse toolkit to optimize your equipment performance and reduce fuel consumption.
Telematics Technologies
Telematics systems are revolutionizing the construction industry by providing real-time insights for contractors, including the location, performance and usage patterns of heavy machinery. Telematics systems utilize GPS, sensors and data analytics. By leveraging this data, contractors can make informed decisions to streamline routes, reduce idle time and ultimately curtail fuel consumption.