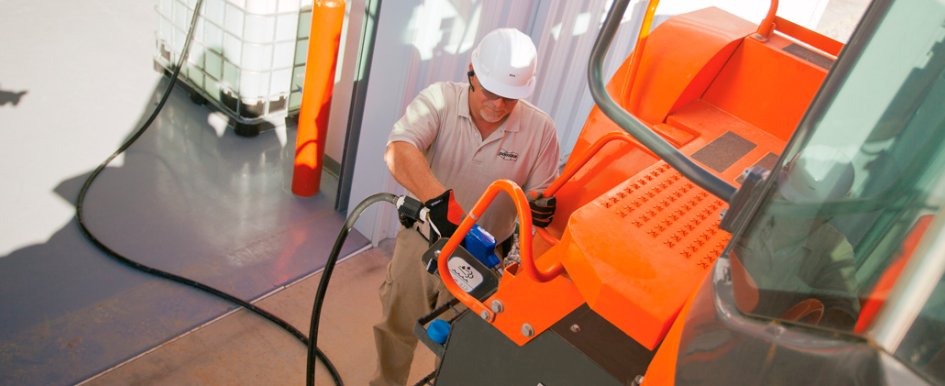
The path to improving air quality and reaching today's emission standards for nonroad heavy equipment began in 1994. Two decades later, most nonroad machines in the United States are Tier 4-compliant, changing the way heavy equipment emits engine exhaust in the atmosphere.
The goal of the emission standards for nonroad equipment has been simple: to lower harmful exhaust emissions, such as particulate matter (PM) and nitrogen oxides (NOx), to help promote clean air and maintain a sustainable environment. These emission standards are part of the Clean Air Act of 1963, which is regulated by the U.S. Environmental Protection Agency (EPA). Reaching Tier 4 compliance has presented some challenges for nonroad equipment manufacturers, including incorporating new technologies to meet the strict standards.
With a better understanding of Tier 4 technologies, following proper maintenance intervals and correctly storing and handling diesel exhaust fluid (DEF), owners of heavy equipment can become more knowledgeable about the impact of today's emission standards on equipment.
Evolving Technology
Articulated dump trucks, excavators and wheel loaders have gone through five emission tiers, ranging from Tiers 1 through 3, interim Tier 4 (iT4) and now Tier 4. As nonroad machines made the move to Tier 4 compliance, the development of more efficient technologies led manufacturers to promote improved machine performance, better fuel economy and longer engine life.
Multiple technologies—ranging from mechanical fuel-injection systems to electronic injection systems—have been incorporated in various tier levels to help meet increasingly stricter EPA emission standards. Technologies such as an electronic control unit (ECU), a high-pressure common rail system (HPCR), diesel oxidation catalysts (DOC) and diesel particulate filters (DPF) were added to help reduce PM, leading to cleaner exhaust.
- ECU: Electronically monitors the controls in the engine
- HPCR: An advanced fuel-injection design controlled by the ECU that regulates the fuel pressure and the injection timing
- DOC: A catalyst that reacts with engine exhaust upon contact, transforming some of the PM emissions into harmless substances
- DPF: A "ceramic wall flow" filtration system that separates PM from engine exhaust (a cleaning process called regeneration is used to burn off accumulated PM and is monitored by the ECU)
With the expansion of iT4 requirements to heavy equipment in 2014 and continued through this year, many off-road machines have an additional system called selective catalyst reduction (SCR). SCR uses an ammonia- and water-based liquid called diesel exhaust fluid (DEF). Combining exhaust with DEF causes a chemical reaction that converts NOx into harmless nitrogen and water vapor. Tier 4 emission standards reduce PM and NOx emissions by approximately 90 percent.
In addition to the engine technologies and aftertreatment systems, diesel fuel refiners started to produce ultra-low-sulfur diesel in 2006. According to the EPA, ultra-low-sulfur diesel is 97-percent cleaner than diesel fuel refined prior to 2006. Customers should be aware of how to properly store ultra-low-sulfur diesel in bulk storage tanks to avoid potential contamination in the diesel fuel and, eventually, in heavy equipment.
Newer fuel filters for heavy equipment are designed to prevent contaminants in diesel fuel from reaching the engine and potentially causing damage that can be expensive to repair. It is recommended that heavy equipment owners regularly clean their bulk diesel fuel storage tanks and work closely with their local fuel provider to verify the quality of the fuel before it is added to equipment.
Easier Maintenance
Many manufacturers implemented a Tier 4 solution with non-DPF diesel engines to eliminate the regeneration process required to clean the accumulated PM in the DPF. With a non-DPF aftertreatment system, customers do not have to clean or replace costly diesel particulate filters.
The machine's engine does not have to burn extra fuel to heat up the filter during the regeneration process, so owners can continue operating without parking the machine for forced regeneration. Another advantage of a non-DPF engine is more room in the engine compartment for ease of serviceability.
"Some heavy equipment manufacturers that have a DPF are required to increase their engine compartment size, and operators may lose visibility to the back of the machine," says Mike Stark, Doosan wheel loader product specialist. "To remedy this, some wheel loaders have a standard rearview camera for better visibility." Most manufacturers offer a rearview camera as an option for enhanced visibility.
Staying on an extended maintenance schedule for engine oil and filters and hydraulic filter changes helps promote the machine's long-term durability and provides many cost benefits to owners and fleet managers. Customers should review their manufacturer's opperation and owner's manual for recommended oils and filters for their Tier 4-compliant machines.
If recommended SCR maintenance is not followed, the NOx levels may not be compliant with Tier 4 emission standards, resulting in the requirement for a machine's diesel engine to be derated until the issue is rectified. Overall, maintenance schedules have not changed in the move from iT4 to Tier 4; however, recommended oils have changed to CJ4 engine oils. If equipment operators fill the machine with incorrect engine oil, it can cause costly damage to the machine's internal components, causing them to become plugged, corroded and not work efficiently.
Importance of Diesel Exhaust Fluid
DEF is a colorless, non-hazardous chemical that has been incorporated in most 75-horsepower engines and higher to help meet Tier 4 emission standards. The aqueous solution consists of 67.5 percent deionized water and 32.5 percent pure urea and is susceptible to variations in hot and cold temperatures. Keep these questions in mind before storing DEF:
- Is the fluid stored out of direct sunlight?
- Is the fluid stored between 12 and 86 degrees Fahrenheit (-10 and 30 degrees Celsius)?
- Is the fluid stored in an airtight container?
If you answered yes to all three, then you are taking the necessary steps to properly store DEF. When the fluid is exposed to extreme heat and direct sunlight, it can shorten its shelf life. One thing to note is that DEF inside heavy equipment can freeze. To thaw DEF tanks and supply lines, engine coolant is used to heat them to allow \uc0\u8232 operating the machine in sub-freezing temperatures.
Operators should also be cautious when storing DEF to help reduce contaminants, such as dirt and dust, when working in earthmoving applications. Operators should try to fill the DEF tank directly from the DEF container. If you are using a funnel or intermediate containers, make sure to keep the container clean and only use the container for DEF. Contamination can damage the catalyst in your SCR system and can cause you to use more DEF than you need. Purity and concentration are critical with DEF.
By understanding the technologies needed to make the shift to Tier 4 emission standards, the required maintenance and how to properly store and handle DEF, construction equipment owners and operators can be better educated about the maintenance that accompanies new technologies to help meet air quality standards.