
Many terms are used to describe air compressor performance. Cubic feet per minute (cfm) measures the volume of air that a compressor delivers. Pounds per square inch (psi) indicates the amount of pressure behind the air. Horsepower represents the power that the engine or motor produces to turn the pump.
These parts and processes seem simple enough, but compressor specifications can get complicated. Rating the cfm and horsepower of a compressor can be done using multiple methods. Other considerations, such as service factor and duty cycle, can affect performance. For these reasons, contractors should make sure they understand all of the jargon in order to avoid poor purchase decisions.
The most commonly misunderstood compressor rating is cfm. In theory, this specification could be determined by multiplying the cylinder bore by the stroke and revolutions per minute (rpm). However, this formula only calculates displaced cfm. Due to factors such as atmospheric pressure, temperature and friction, compressors actually produce less air than this number implies.
To accurately measure performance, other rating systems have been developed. For instance, standard cfm gives the volume of a unit according to certain conditions, such as 14.7 pounds per square inch absolute (PSIA), 60 degrees ambient temperature and zero percent relative humidity. Actual cfm calculates the true output of a compressor at real-world operating conditions.
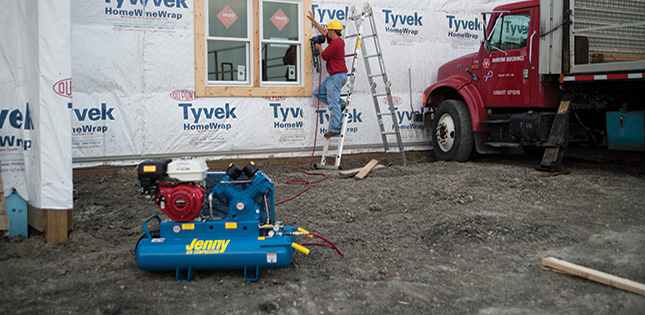
Because the industry doesn’t have a gold standard for rating cfm, manufacturers can advertise whichever number they prefer. Some choose to be more realistic and use the actual cfm rating, while others state the displaced cfm
because it’s the larger number.
Regardless of the rating method, never compare apples to oranges. In other words, don’t directly compare a unit that advertises a displaced cfm with another unit that states the actual cfm. In this case, the best approach is to ask for the actual cfm of the first unit and then make a fair comparison of the compressors’ air volumes.
For gas-powered compressors, horsepower ratings are fairly straightforward, making comparisons of different units easier. Generally, the ideal solution is to look for an engine with more than enough power to turn the pump. If the engine is underpowered for the unit, it will constantly run under high stress, leading to premature failure.
On the other hand, the horsepower ratings on electric motors are more misunderstood. A person may believe he or she has a 5.5-horsepower unit when it really only
operates at 1.5 horsepower. This is the difference between peak and continuous horsepower.
Peak horsepower is the maximum output that a motor can produce. However, the motor only achieves this level during startup when the start windings are engaged. Once the motor reaches normal rpm, the start windings disengage, and the motor runs at its continuous horsepower rating, which can be five to seven times less than peak horsepower. If the motor were to operate at its peak horsepower longer than the initial startup period, it could quickly overheat and would likely experience a short service life.
Some manufacturers will advertise the peak horse-power because it’s a larger number, while others will state the continuous horsepower. Again, be sure to use the same rating system when comparing units.
The service factor can further predict how a motor will operate under load. This number indicates the percentage of continuous horsepower at which the motor can safely operate. For example, if the service factor is 1.15, the motor can run without issue at 115 percent of its rated continuous horsepower. The higher the service factor, the better the motor is at handling various operating conditions.
Also note the operating rpm. Most electric motors found on compressors will operate at approximately 1,725 or 3,400 rpm. The slower rpm units generally hold more value, since they operate more quietly, generate less heat and produce less wear and tear than faster motors.
Even if a unit appears to be adequately rated for the task at hand, a few more items should be checked.
The first item to consider is the compressor’s duty cycle, which will affect its performance on the jobsite. All air-cooled piston compressors generate enough heat that they eventually need to rest in order to avoid overheating. However, some compressors can last longer than others. The best units on the market have duty cycles of up to 80 percent, which means they can run 80 percent of the time and rest for the other 20 percent. On the other end of the spectrum, lower-quality units may have duty cycles of only 10 to 20 percent.
Another item to consider is the drive system. Is the compressor direct- or belt-driven? Keep in mind that direct-drive units may be cheaper, but belt-drive compressors generally last longer and are easier to maintain.
In a direct-drive system, the pump will turn at the same rate as the crankshaft, which is faster than necessary. Direct drives also are susceptible to more damage because the crankshaft is coupled directly to the pump.
Belt-drive units increase the ratio of how many revolutions the crankshaft makes to how many times the pump turns. In fact, the belt can slow the pump to almost half the speed of the motor, which greatly reduces wear and tear. Furthermore, if either the motor or pump fails, the other component is likely to remain unharmed.