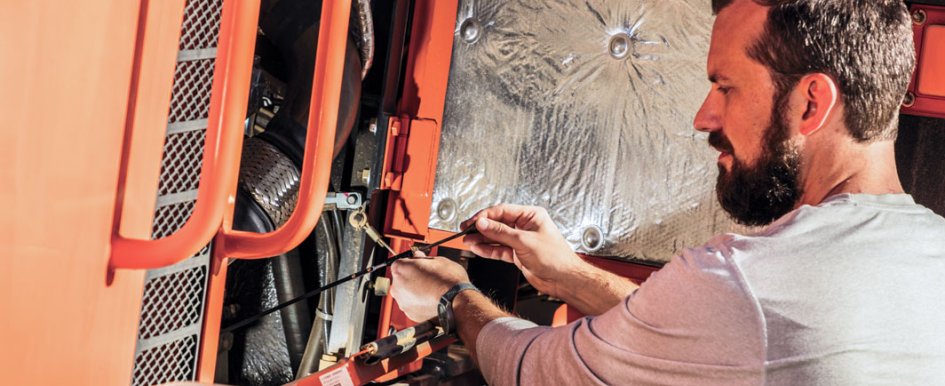
It’s likely no surprise that the diesel engine in your construction equipment today is a far cry from the ones used 30 years ago. Even significant updates within the past 10 years have changed diesel engines dramatically. What is under or behind a machine panel today is a sophisticated and connected diesel engine with less emissions.
Before Tier 4 was a common phrase in the industry, diesel engines were still the lifeblood of construction equipment, including excavators and wheel loaders, providing the muscle to do heavy earthmoving tasks. They may have supplied the power and torque needed to get the job done, but they were not as productive as the diesel engines of today.
Major changes to nonroad diesel engines have resulted in emissions reductions due to changes from Tier 3 to interim Tier 4 and, finally, to Tier 4. Construction equipment manufacturers have designed systems more holistically—instead of producing a diesel engine that is just a component of the larger system.
In years past, the diesel engine itself could be mixed and matched. Now, the whole system is designed very tightly with the specs of the engines so that the hydraulic system or the transmission, depending on the type of equipment, are optimized for one another. The component optimization means owners and operators can enjoy enhanced machine productivity, especially better fuel efficiency, which can lead to significant cost savings.
Massachusetts contractor Ralph DiGiorgio says newer equipment, particularly his wheel loaders with diesel engines, use much less fuel than previous generations. “We have a couple of big machines that are eating 75 or 80 gallons of fuel a day,” he said. “The new machines are burning a third less than that.”
Performance Enhancements
One of the benefits of today’s more sophisticated diesel engines is improvements to how the engine performs. Advancements in more consistent fuel burn and fuel-delivery systems combine to help maintain the optimal torque levels. In other words, while horsepower may be the same as it was a decade or 2 ago, the lugging ability of the engine (also known as the torque curve of the engine) has been optimized within that same horsepower level.
The advancement from mechanical to electronically controlled engines has also brought significant change to diesel engines. Electronically controlled engines are much more efficient. There are multiple injection points for fuel within the combustion cycle to help maximize the fuel burn and generate the most power with every stroke of the engine’s cylinder.
Improvements to high-pressure, common-rail systems—with very fine droplets of fuel injected at multiple points within the combustion cycle—have helped improve productivity in addition to reducing fuel consumption and emissions.
Design Changes
Although the physical dimensions of today’s diesel engines haven’t changed, the space for the engine compartment has increased. Additional space is needed to accommodate the extra components necessary for diesel engines to meet strict emissions requirements. As a result, some machine envelope sizes have been widened or heightened to allow space for the additional components.
In some cases, a larger engine compartment can impact the operator’s visibility into the area behind machines, such as wheel loaders. Many equipment manufacturers now offer rearview cameras to provide operators with assisting visibility to their surroundings.
Keep Maintenance Top of Mind
It cannot be overstated how critical it is for owners and operators of construction equipment to properly maintain the machines. Skipping daily maintenance may lead to debilitating machine shutdowns, resulting in downtime during the peak work season.
It goes without saying that operators must check the engine oil every day. It’s also a good idea to check for leaks around the filters and the oil pan. Operators should keep track of and change oil at the recommend intervals, as service-interval schedules are designed to make sure the engine and other components are kept working at optimal efficiency.
Quick reminder: oil is used in machines to help keep the engine cool or running at its optimal temperature. It also helps disperse impurities that may be within the system. The oil is designed to help dissipate the impurities and the heat within the system. Today’s Tier 4-compliant engines require CJ-4 oil, which has been optimized for working with new high-pressure fuel systems. Another good tip: Be sure there is no major debris around the engine.
Operators should also monitor components, like aftertreatment devices, to ensure they are well maintained, including when diesel particulate filters need to be replaced. The newest CJ-4 oils help minimize issues with these filters. Still, it’s recommended that you monitor the machine’s diesel exhaust fluid (DEF) system if the machine is equipped with selective-catalyst reduction.
If an operator is lax with proper engine maintenance and aftertreatment systems, serious issues can develop. For example, the machine’s diesel particulate filter may start needing more frequent regeneration, as well as replacement, due to the trapping of oil additives. Over time, the machine may experience a reduction in engine performance because it has to work harder for the exhaust to breathe properly.
Operators should keep a supply of oil and oil filters on hand, especially if the machine is working at a jobsite for an extended time. Use genuine original equipment manufacturer (OEM) filters that are designed for use with the engine, since they have the optimal filtering capacity and fluid flow, maximizing the ability for enough fluid to pass through the filter.
Air filters should not be overlooked either. The air filters are designed for specific engines with an airflow window that is optimized for the engine. It helps maintain the proper flow of air into the engine, allowing the combustion process to work properly.
Stay Vigilant
Lastly, even though newer telematics management systems on construction equipment can alert customers and dealers about critical issues, operators should not depend on these warning signals alone. Attentiveness is still crucial for both safety and efficiency on the jobsite.
Diesel engines have come a long way in the last decade. They are more productive, allowing for increased machine performance. However, they also require more vigilance and increased maintenance checks to ensure the engines and the aftertreatment systems are working properly. Visit with your operators to make sure they understand the importance of properly maintaining the engines for peak performance this season.