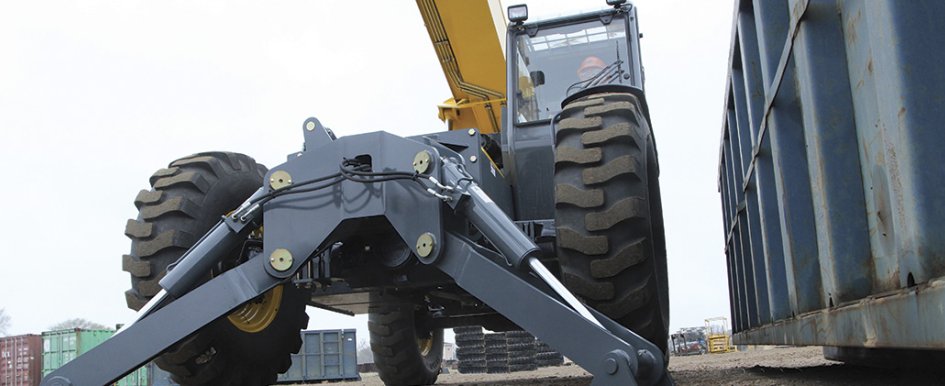
As a large general contractor, a safety coordinator or project manager, selecting and evaluating the correct equipment used by your workers is not only important to your project profitability and schedule, but also to the safety of the equipment operator and other workers on the jobsite.
The telescopic handler is the largest piece of equipment on many construction jobsites. Understanding the correct operation of this unit is critical for the operator, but also for the supervisors to identify and correct poor operation habits before they become an accident.
1. Are all operators trained with certification compliant to OSHA CFR 1910.178 requirements?
Required by OSHA since 1999, the answer to this question quickly tells you if your operator has passed both the classroom and hands-on training required to operate a telescopic handler in North America. Appropriate supervisors are also trained to be aware of those operators not following standard safe operating practices with the telescopic handler on the jobsite. Training materials are available from many telescopic handler dealers or by contacting AEM and asking for the “train-the-trainer” materials for the rough-terrain forklifts. Operator certification is valid for three years at a time. The operator should be required to retrain if they are involved in a near miss event, accident or are observed operating the telescopic handler in an unsafe manner.
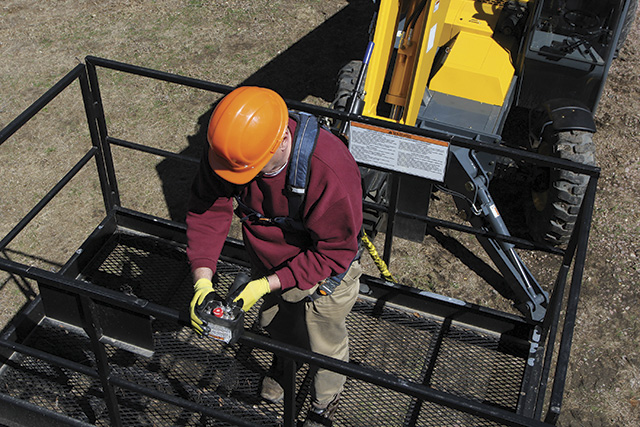
2. Have you identified the jobsite hazards?
Both supervisors and operators are responsible for identifying and addressing jobsite hazards. They must be vigilant in this responsibility as conditions frequently change on the jobsite. Overhead electrical power lines can be deadly if a telescopic handler comes too close to them. Likewise, poor soil conditions, drop-offs or other potential hazards must be identified and addressed to assure safe operation. Identifying potential hazards beforehand allows the telescopic handler operator to carefully consider the best actions to avoid the hazard. Planning ahead to avoid hazards eliminates a situation in which the operator must address the hazard during work tasks. Both current jobsite conditions and potential changing conditions should be
considered carefully.
It is also important that the operator can see a clear path for travel and that other workers can see where the telescopic handler is operating. Placement of jobsite materials and supplies should be done so they can be easily accessed for use, but also so they do not restrict line of sight for the telescopic handler operator.
3. Have you read and understood the operator’s manual?
While reading technical manuals can be difficult, a trained telescopic handler operator must understand the controls and functions of the specific telescopic handler model they are operating. This information is found in the operator’s manual. Some telescopic handler models use different joystick control layouts and have unique options. Your telescopic handler operator should be comfortable with the correct operation of the telescopic handler because they understand how the control functions work on that model.
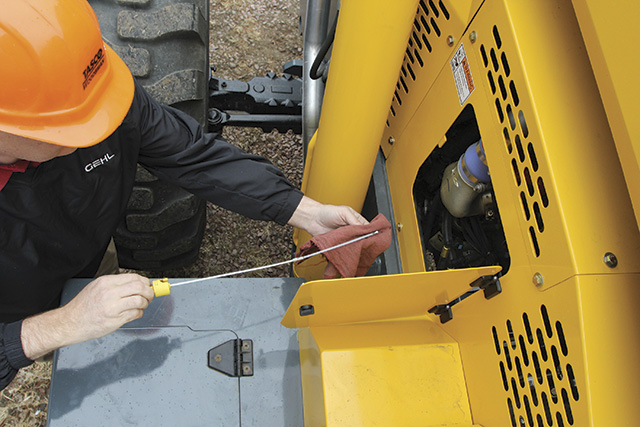
4. When is the next scheduled maintenance for this machine?
Your telescopic handler operator should know that correct daily and weekly maintenance items are being completed as required. Regardless of who is doing the work, the operator should know if the maintenance work on the machine is being completed as needed to prevent premature wear and expensive breakdowns.
Trained operators understand the importance of doing a prestart inspection of the machine before starting work to identify any possible problems with the telescopic handler. This prestart inspection can identify problems with the machine, which, if not repaired, could place both the operator and other workers at risk. Preventative maintenance is important to keeping the project on schedule, too.
A common operational misunderstanding of telescopic handlers is that, because they have a steering wheel and two pedals, like an automobile, the two vehicles can be operated in the same manner. It is critical that operators recognize and understand the differences between the two pieces machines. A telescopic handler is designed to be different and should be operated in a different manner than driving an automobile. For example, the telescopic handler is designed for low-speed travel on uneven terrain, while the automobile is designed for high speed travel on improved surfaces. Additionally, when loaded, the center of gravity for the telescopic handler changes, and when changing the position of the load using the telescopic boom, the center of gravity will also change. Due to the unique design of the telescopic handler, operators must always be aware of the stability of their machine for safe handling on the jobsite.