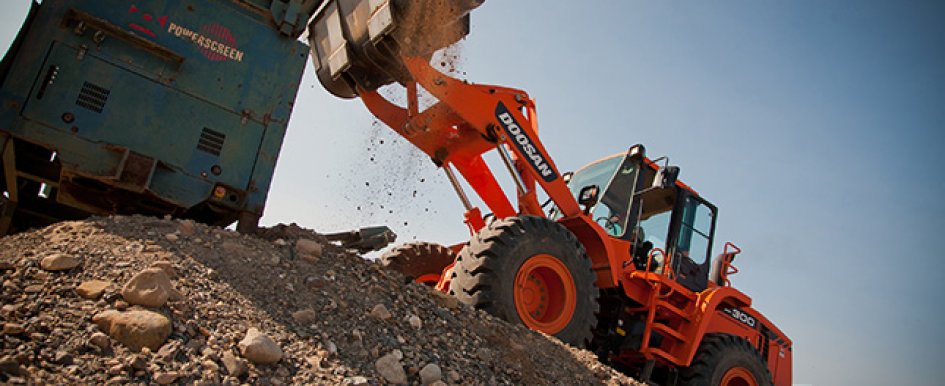
In today’s rapidly evolving industry that is characterized by continual innovation, you are expected to be on the leading edge of the services you provide to your customers and the equipment you invest in. And you need to do it all without sacrificing the safety of your employees. Whether you spend your days in a machine cab or at a desk, as an owner, you know that each machine has its performance limits, but a number of other factors can impact operator protection and productivity.
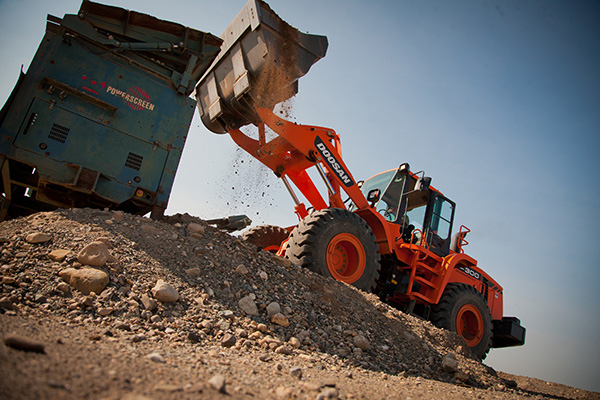
You and the operator will be the most knowledgeable about the capabilities of a wheel loader or an excavator and the machine’s role in your operation. Ultimately, however, you are responsible for your fleet and its proper operation. To avoid exceeding the limits of your machines, you must first understand the application each machine will work in and be aware of the potential hazards that may exist at a particular jobsite. You’ll want to consider the jobsite’s terrain and how often the machine is being used to perform multiple high-volume tasks.
Stretching your equipment’s capabilities has consequences, including more downtime, higher maintenance costs and increased total cost of ownership—all of which have a direct impact on productivity and profitability. The more you know your machine’s limits, the faster your company can respond to changing jobsite conditions that could pose a threat to the operator or others and the greater chance you have of extending the life of your machine.
Evaluate Capabilities
The process of learning a wheel loader’s or excavator’s limits typically starts with examining the specifications of a particular machine. Don’t assume that you or the operator knows a machine’s specs just because you may have owned a similar model in the past. Specs change as models change, and a knowledgeable dealer can inform you about how a machine will perform in your application and working conditions.
Evaluating performance specifications for a crawler-excavator should include an analysis of lifting capacity, arm and bucket force and swing torque, as well as front digging dimensions, such as reach and depth. Top wheel loader specs should focus on lifting capacities, as well as full-turn rated operating capacity, breakout force and dump height.
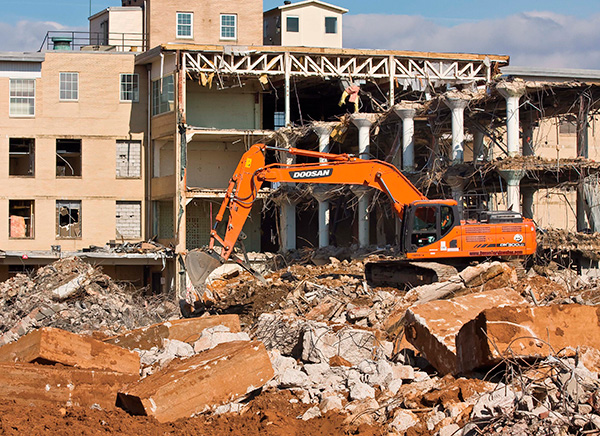
Both wheel loaders and excavators can be used with different attachments, which can double or triple their capabilities to enhance your business year-round. Attachment weight and dimensions are typically not included in general specifications. Because of this, owners and operators must account for the added weight of an attachment or coupler system and adjust the lifting capacity of their machine accordingly. For instance, a 14-ton excavator equipped with a 36-inch bucket can weigh considerably more than a machine with a 24-inch bucket. This additional weight can significantly lower the lifting capacity of the excavator.
Owners and operators should give strong consideration to the density of the material a wheel loader or excavator bucket can safely move. While you may be working with multiple material densities from sand to boulders, you should determine bucket specifications based on the heaviest material the machine will handle and include that calculation in the lifting capacity evaluation.
Finally, the operator’s visibility of all sides of the machine, including the attachment, is key to safe digging and lifting in any application. Operators should be able to see their attachment working at ground level from a normal seated position in the cab. Many manufacturers have improved an operator’s sight lines to increase visibility. In addition to reducing component obstructions, the cab designs of some excavators and wheel loaders provide windows that offer 360-degree visibility. Being able to comfortably see the attachment with top-down and peripheral sight of the tires or tracks and having an unobstructed view of the machine’s rear are critical to efficient operation.
Perform Routine Maintenance
While a list of machine specs provides quantifiable performance capabilities in an ideal situation, specs don’t take into account the condition of a machine that hasn’t received maintenance in 2,000 hours. Routine daily maintenance and pre- and post-use inspections of heavy construction equipment are critical to ensure proper machine function and keep productivity high.
Good performance of hydraulic and lifting systems can easily be squandered if maintenance intervals are extended past the manufacturers’ recommendations. Although machines have some built-in component protection, staying on top of routine maintenance intervals—especially with today’s more sophisticated engines and hydraulic systems—is critical to avoid expensive repairs and replacements. Assistance from dealers and tools such as fleet management systems can help you monitor routine maintenance intervals, keep the emphasis on checking vital fluids and filters and help operators detect early warning signs of critical system failures.
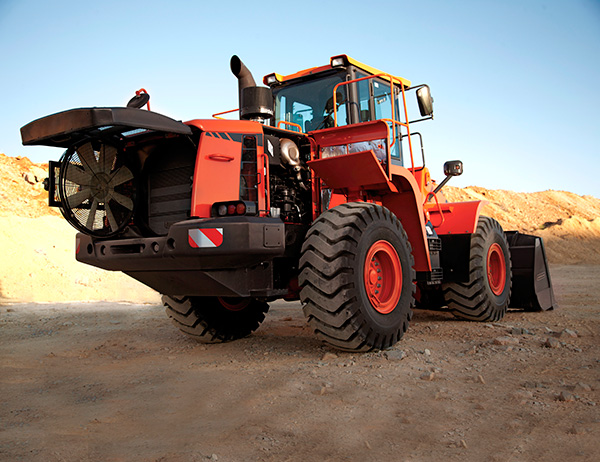
Those responsible for maintaining wheel loaders and wheel excavators should also check their tires frequently—referring to manufacturers’ recommendations for proper pressure—and inflate the tires accordingly. In addition to the correct pressure, maintenance and inspection of tires would not be complete without a thorough visual inspection to make sure no sizeable chunks of tread are missing, the bead line and the rim are intact and the wheel mounting hardware is torqued properly.
For crawler excavators, routine visual inspections of tracks and the condition of attachments are especially important. In rugged and rocky environments, wear will be greater on the ground-engaging tools, the undercarriage and items such as pins, bushings and idlers. While visual inspections are excellent avenues to help prevent common maintenance problems, the bottom line is that diligent routine maintenance pays off.
Elevate Training
Your wheel loader or excavator investment is even more valuable when an operator has the proper training to put it to use safely and productively. Though innovation is continually improving machine capabilities, operators still need to enhance their core competencies. Are you making training opportunities possible for your operators? Some machines offer power modes that can balance fuel consumption and machine power to match working conditions. By selecting the proper power mode for a particular task, operators can improve fuel efficiency. These technologies can enhance an operator’s control of the machine performance but only if they’re activated and used effectively.
Typical training opportunities are designed to increase operator proficiency with systems, controls and proper operating procedures. A quality training program can help you and/or your operators achieve a machine’s maximum performance, enhance your knowledge of the particular features of a brand and improve the likelihood that an operator’s skill level will increase. Several manufacturer, dealer and third-party resources exist to help operators elevate their operating skills to the next level.
Every machine has its limits. The time you take now to understand each model’s specifications, capabilities and performance potential and to meet the education needs of your operators will pay dividends for your long-term investment.