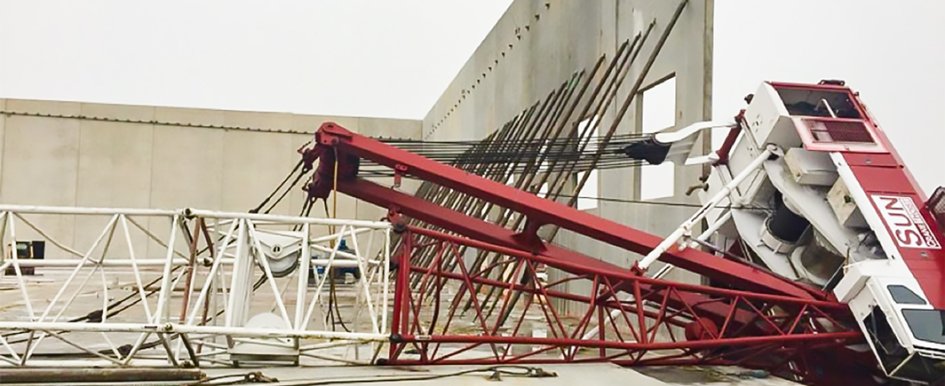
Recently, a crew working a “tilt-up” job in Austin, Texas, got a frightening reminder of how important regular crane maintenance and equipment inspections can be after an accident on the jobsite. (You can watch live video of the accident at youtube.com/watch?v=Mn6PYOG6sWw.)
In any accident situation, there are a number of things that could go wrong with the equipment. In this case, maybe the lattice boom truck crane was too small for the job. Maybe its outriggers weren’t extended far enough to support the pick. Or maybe there was a defect with the rigging. A defect at a hoist point or a strap failure at the shackle may also have been to blame. It’s too soon to say for sure what caused the accident, but below are a few observations that could have signaled a red flag to the teams on the jobsite.
- Where the crew is located—In a tilt-up construction job, a structure’s walls are poured at the jobsite. These large slabs of concrete are then raised into position around the building’s perimeter to form the exterior walls of the structure. Part of the danger of putting up a concrete tilt wall is that someone is usually placed in the most dangerous location—under the load—where they have to be ready to pull the braces away, so they don’t dig into the slab once the wall is vertical. Once the panel is almost vertical, someone has to grab the pole braces and hold them off the floor slab as the panel is set into place, and then anchor them to the slab once the panel is set. Additional crew will be at the base of the panel to ensure it is set correctly, and then they will place shims at the bottom, so it is at the right elevation. In this instance, however, the crew was filmed casually standing next to (and, in one case, on) the load and not really paying close attention.
“Sometimes a crew gets lackadaisical, and they miss something and an accident like this happens,” said Phil Woodruff, operations manager at LC Crane Parts and Service in McDonough, Georgia. “It seems like the safety aspect is sometimes furthest from their minds.”
- The use of tag lines—If tag lines weren’t used (they aren’t visible in the video of this accident, so we can only assume they were not), perhaps this incident wasn’t a crane failure as much as it was a rigging failure. According to OSHA 1926.1401, a tag line is “a rope attached to a lifted load for purposes of controlling load spinning and pendular motions.” These lines are important for controlling awkward loads and maneuvering them into positions.
- The angle of the lift—While watching the video referenced at the beginning of the article, notice the pick residuals on the slab; the panel is not in its original orientation. Those panels are usually raised and—only once they are vertical—moved to their final positions. In the video, the wall is lifted in the eight attachment points (connected to cables that run through pulleys to allow the angle of the panel to adjust as it is lifted) that are embedded in the concrete when they pour the panel. In the video, the operator may have been moving the panel at too shallow an angle. You can see that one of the attachment points comes free, causing excess stress on the other points. “If it was a rigging issue, meaning if the chain snapped or something, a 15-ton wall is going to pull a crane down whether you have the outriggers pulled out correctly or not,” said Woodruff. The tilt-wall panels are thick, solid concrete and rebar. A sudden drop of the panel can easily cause a crane to tip.
The accident certainly could have been a lot worse. According to the man at the site who filmed the video, the only injury incurred was one broken ankle. Of course, it’s too early to say exactly what caused the accident, but the potential mistakes and equipment failures mentioned here are exactly the sort of issues that make a construction site dangerous. In fact, mobile crane accidents typically result from one of the following two factors: operator error and incorrect crane setup.
- Operator error—Crane safety depends on multiple stability measures. Some considerations can include outriggers, counterweights and weight scales, along with the operator’s own choices. Operators need to know how to read load charts and how much weight cranes can lift safely with the boom at any given angle. The national certification program offered by the National Commission for the Certification of Crane Operators (NCCCO) can prepare candidates for the CCO certification examination and equip them with the knowledge they need to perform safe lifts. New OSHA regulations requiring employers to ensure operators are adequately skilled and properly instructed on how to operate equipment go into effect later this year.
- Incorrect setup—Mobile cranes don’t have as many safety devices built into them as tower cranes, plus it’s much easier to override the onboard safety systems. Operators should make sure the ground beneath the crane is stable and can withstand the weight of the machine and the load. This means making sure the correct blocking and cribbing are in place, and that outriggers and crane pads are placed correctly. They should calibrate the load moment indicator (LMI) to ensure data such as boom angle and load weight are accurate. They need to be aware of the proximity of overhead power lines and of environmental factors such as high winds.
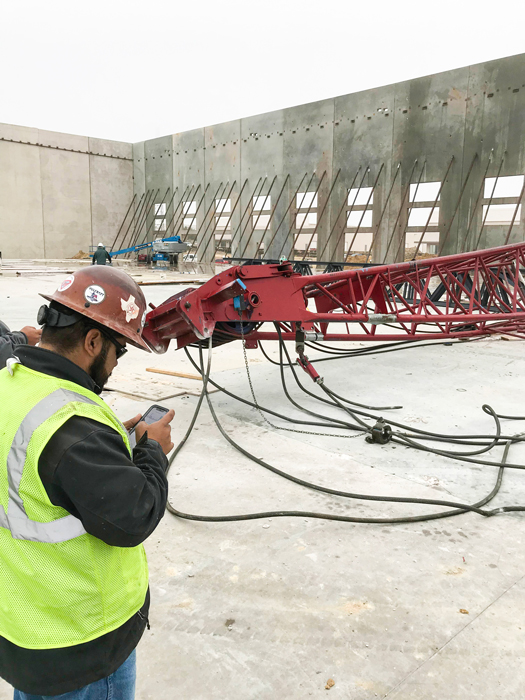
Now that we’ve looked at what can go wrong at the jobsite, let’s look at some preventive measures to take before the lift even begins. It’s important for fleet managers and contractors who operate cranes and other equipment to use a regular maintenance schedule. If they follow the maintenance section in the operator’s manual for each crane, they will be in good shape. Real problems can arise when they don’t.
“They can’t just run the cranes until something breaks, and then worry about it,” said Woodruff. For example, regular maintenance means checking lattice work to make sure there are no weak spots, checking all the fluids and keeping all the filters changed. “If a contractor doesn’t know how to do the preventive maintenance, one of our guys can go through it with them,” said Woodruff.
In addition to following a maintenance schedule, prelift inspections are also critical. Even experienced crews may have inadvertently pushed a crane beyond its limits, damaging key components and parts in the process. Annual inspections may be required to ensure all components are working properly, depending on the crane and where you work. Still, a prelift inspection before every job will mitigate risk as well.
“If the problem [that caused the accident in Austin] was with the rigging and not the crane, there may have been something wrong with the chain that led to the accident,” said Woodruff. “A proper inspection might have caught a weak spot in the chain, for example.”
Although crane owners generally come to them when there’s a problem with the electrical system or some other repair is needed, crane service providers can help companies when they add a new crane or other equipment to their fleet and aren’t sure how to inspect it and establish a maintenance schedule.
Woodruff’s advice for someone buying a used crane? “Make sure you get the crane inspected. That’s No. 1. If you’re going to pay a couple hundred thousand dollars for a piece of equipment, you need to make sure it works.”
The next most important safety objective is to make sure you have the correct load capacity for the work you’ll be doing. Make sure the used crane you buy is rated at the capacity that you need to do your next job.
“It’s hard to forecast what job somebody may call you for in the future,” said Woodruff. “But you can look at your project history and know what kind of loads and picks you made and decide what kind of capacity you need.”