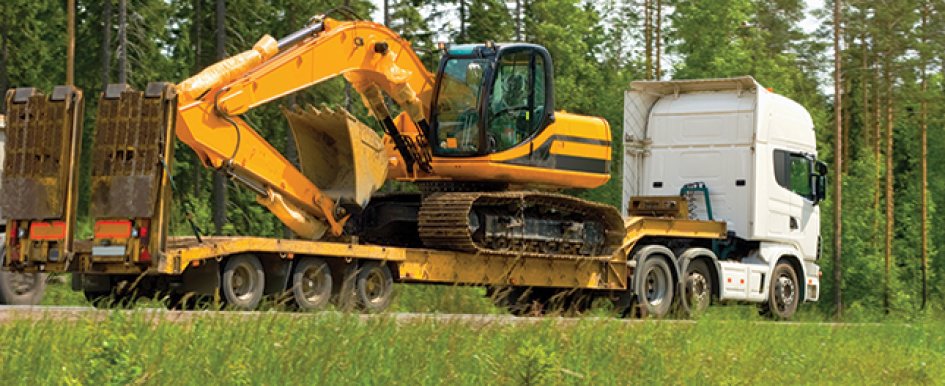
You can’t see it, and typically you can’t hear it, but it’s happening to every trailer tire on the road: loss of air pressure. It results in increased fuel consumption and reduced tire wear life, which causes blowouts that require costly repairs and increased downtime, insurance premiums and labor costs. In the worst case scenario, it can cause serious injuries.
Most fleets experience at least one tire blowout every year due to underinflated or damaged tires, and the associated costs can be staggering. In fact, tires are the No. 1 maintenance cost for fleets. Drivers who operate a rig with underinflated or damaged tires could receive penalties from the Federal Motor Carrier Safety Association, which enforces safety regulations for carriers and commercial motor vehicles.
The best way to avoid these ramifications is to implement a preventative maintenance program that includes everything from checking tread depths to servicing lug nuts. But perhaps the most critical aspect of any program—the one that can have the most profound effects on safety, overhead costs, fuel efficiency, wear life and customer satisfaction—is tire pressure.
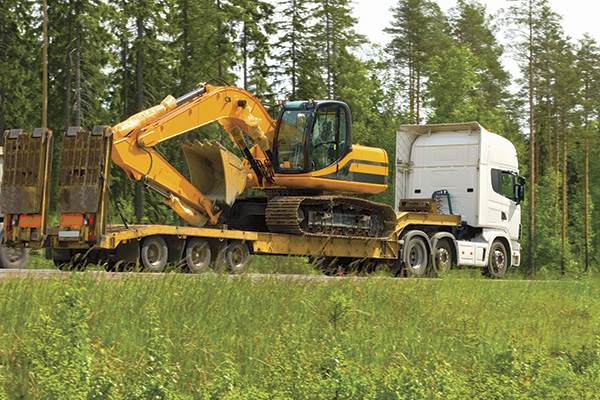
At a Loss
Air loss varies from tire to tire, day to day and load to load, and it can be affected by road conditions and weight distribution with each load. No carrier is immune. According to the U.S. Department of Transportation, only 44 percent of all tires on the road are within 5 percent of their target pressure, and approximately 7 percent are underinflated by 20 psi or more. Tires that measure 20 percent below the psi recommended by the tire manufacturer based on the weight of the load should be removed from service.
The costs associated with a blowout add up quickly. One new tire can cost between $350 and $1,000. Throw roadside assistance or a tow into the mix and you could spend an additional $400. The time spent replacing a tire or repairing damage means drivers are out of service. In addition, blowouts can cause damage to trucks, trailers, property and other vehicles, which can result in more insurance claims leading to increased premiums.
Drivers operating vehicles with underinflated tires also could be heading to the pump more frequently. As the underinflated tires roll, they bend more, which builds up internal heat and increases rolling resistance. This can reduce fuel economy by up to 5 percent, and companies with larger fleets can see a substantial increase in fuel costs over time. Also, a reduction in tread life of up to 25 percent can occur in tires that are underinflated by only 6 psi. Shorter tread life can mean premature tire failure or blowouts and more frequent retreading or tire replacement. In addition, drivers can experience poor braking, reduced steering control and instability around corners.
Conversely, pumping a little extra air into your tires may sound like a good way to save time and avoid the hassle of regular inspections, but it also can lead to costly repairs or replacements. Overinflated tires maintain less contact with the road, so they are more susceptible to damage when driving over rough roads, debris and potholes. The center of the tire also wears faster than the outside, which shortens its wear life.
Putting the Pressure On
Monitoring tire pressure is simple, yet it’s one of the most challenging aspects of a maintenance program to enforce. Checking pressure on 18 tires and refilling two to three can take up to 30 minutes. Doing that on a weekly basis adds up to 26 labor hours per year, per truck, which directly impacts the bottom line. However, advanced monitoring systems can reduce or nearly eliminate the time it takes to monitor pressure.
Tire pressure monitoring systems (TPMS), which typically can be installed on most wheel sizes, feature sensors that are mounted to each of the wheels and constantly track the psi of each tire. The sensors transmit the air pressure reading in each tire to a factory-installed or retrofitted display, which alerts drivers of low pressure so they can refill before a blowout occurs. Because the system—not the driver—monitors the pressure, these systems reduce overhead costs.
Another option for monitoring tire pressure is to install an automatic tire inflation system, which routes air from the trailer’s existing air supply to the system’s control box and through each axle. The axles carry air through a rotary union assembly, which distributes air to each tire as needed to maintain optimal pressure while traveling.
Drivers don’t need to check tire pressure or even refill, which practically eliminates operator involvement and reduces labor hours. Since the system keeps the tires at the optimal pressure, it can provide an average fuel savings of 1.4 percent and can increase tire life by up to 10 percent. In addition, an automatic inflation system nearly eliminates the chance of a blowout due to underinflation, enhancing the safety of the driver and other motorists and reducing downtime.
Some systems also monitor the temperature of the wheels, which can increase as a result of hub bearing failure or brake-related failure. The system alerts the driver if wheels become overheated before costly damage to the wheels and tires occurs. The system also is compatible with satellite communication systems so both the driver and dispatcher can monitor tire conditions at all times.
Like a TPMS, an automatic inflation system can be installed on any wheel size and on new or existing trailers, including flatbed, drop, liquid tanks and dump. While the up-front cost might be a deterrent initially, the time and money these systems will save can typically be recouped in only one year.
Regular Inspection
Drivers should regularly inspect the wheels and surface of each tire. An uneven wear pattern or flat spot typically indicates that the wheels need to be realigned. Driving with misaligned wheels causes tires to wear faster, increases rolling resistance and results in increased fuel consumption. Look for tread or sidewall separation, cuts or gouges, and inspect the exposed belt or ply material to ensure every part is in good condition. Rocks or material built up between duals should be removed as the pressure could puncture the tires.
You should also periodically check the lug nuts. They can loosen over time, which puts extra force and weight on the remaining nuts, adding stress that could fracture the wheel. Inspect the lug nuts periodically to make sure they are tightly fastened and free of rust, and ensure the lock rings are properly sealed.
Road conditions can change in a moment, so ensure tread is the right depth and in good condition to optimize traction control in rain, sleet or snow. Drivers should check tread depth once a month. The Department of Transportation specifies that tread depth should be a minimum of 2/32 of an inch when traveling during normal conditions. If rain becomes a factor, the depth should be at least 4/32 of an inch and 6/32 of an inch in snow.
From increased safety to reduced repair and replacement costs to lower fuel consumption and longer wear life, a preventative maintenance program offers benefits companies can’t afford to be without.