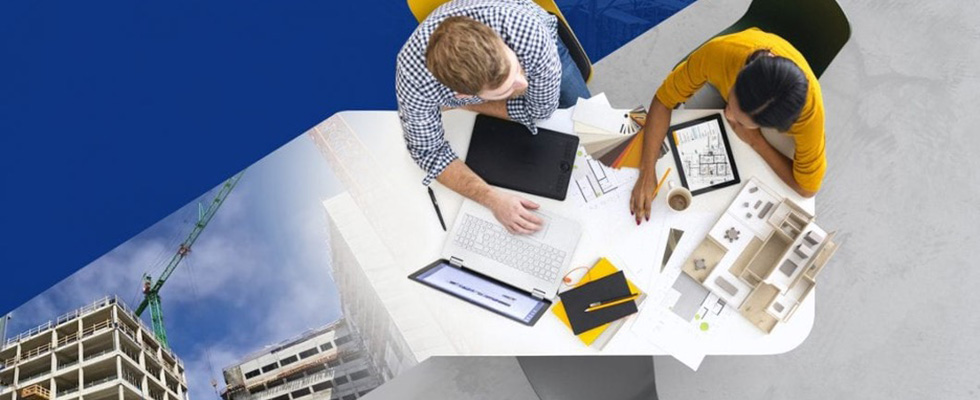
The success of the preconstruction phase depends squarely on effective collaboration across multiple stakeholders. Yet, preconstruction planning has long been full of silos. During the preconstruction phase, teams often operate independently, only collaborating or sharing information when absolutely necessary. This siloed approach has been in place so long that it’s easy to miss the problems it causes.
From overextended budgets to project delays, an ineffective preconstruction phase can cause your construction life cycle to fall like dominoes. Research shows that as a project advances, trying to fix those problems and make changes becomes more expensive and challenging. The upside of this fact is that success in the preconstruction phase can lead to significant cost and resource savings.
Leading construction firms are leaning into preconstruction collaboration to generate better outcomes for themselves and their clients. You can learn more about how to strengthen relationships with trade partners, internal departments and other contributors in the preconstruction phase in the following guide to preconstruction collaboration.
The Challenge of Preconstruction Collaboration
Despite the fact that projects depend on cross-team coordination, construction has long been known as a fragmented industry. There are often so many stakeholders involved that it’s hard to know who’s doing what and what their current status is. Each stakeholder has their own objectives, and it’s easy to lose sight of the project’s overall goal. That being said, it’s not that project contributors don’t want to collaborate. Instead, the problem is that the traditional approach to preconstruction doesn’t allow for effective collaboration.
Challenges With Traditional Delivery Models
One of the biggest challenges to preconstruction collaboration? Delivery models. Traditional delivery models just don’t encourage teams to work together from the get-go. Specialty contractors are essential to the success of projects, yet they rarely have a chance to provide input at the beginning. This setup only leads to conflicts, confusion, rework and delays down the road.
So, what can teams do to improve preconstruction collaboration, especially with specialty contractors? When possible, look for methods that incentivize collaboration. For example, integrated project delivery (IPD) brings together each key element of a project from the start: people, resources, systems and practices. Rooted in lean construction and integrated practice, IPD has all stakeholders work together as one firm. It uses a multiparty agreement to define responsibilities, roles, compensation and rights. Other key components include the implementation of lean concepts and an intentionally collaborative culture.
An expert in IPD describes its benefits for collaboration: “IPD projects share a common theme around collaboration, focused on a team mentality backed by an agreement. IPD contracts are built to bring teams together through the challenges they face. Although there are ways to be successful through trials in a collaborative delivery model, the IPD contract is built to prevent a team from sliding off track. The IPD structure creates an environment of open communication and establishes a chain of command.”
Because collaborative delivery models like IPD align owners into the process much earlier, they help to deliver improved project outcomes.
No Single Source of Truth
There’s one major stumbling block to preconstruction collaboration even the most motivated teams face: disparate systems and data. Without a single source of truth, stakeholders don’t have a clear path to follow or means of accessing information. In construction, information often lives in several different systems. This can lead to duplications, outdated project data and miscommunication. This siloed data environment is also extremely costly; construction professionals spend over 14 hours a week on nonoptimal activities, including looking for information, conflict resolution and rework. That adds up to $2.4 million wasted per firm each year.
It’s absolutely critical to set up teams with a solution that provides a single source of truth from the beginning of a project in design and preconstruction through operations. This tool shouldn’t just be for accessing documents. It should also make it easy to collaborate, communicate and keep track of project progress and tasks. Managing all of these key activities in one place helps to create a fuller, more portable picture of key project data.
Collaboration Requires Connected Tools
Do you have the technical solutions you need to collaborate? Are those solutions connected to each other? Ensuring collaboration throughout the project life cycle depends on connected technology. Those connections matter because they prevent data leakage and loss when they move across stakeholders and phases.
Connected construction tools bring in data and workflows across multiple solutions such as estimating software, bidding software, design models and project management software. By starting with the right tools in the design and preconstruction phases, you can support collaboration as the project progresses. Sharing information across platforms, according to Construction Dive, allows contractors to “load and then find information from all of their preconstruction tools in one place, and vendors are not siloed in their solutions, all of which means that the customer can leverage a connected workflow and customizable solution.”
7 Strategies to Improve Preconstruction Collaboration
In this new guide, you’ll find the highlighted benefits of preconstruction collaboration, plus strategies and methods for making it happen at your own firm, and learn:
- How to move toward a more connected, collaborative process across the board
- Ways seven leading contractors have improved preconstruction collaboration
- Tips for facilitating communication with the field
Download the e-book now to start exploring these seven strategies.