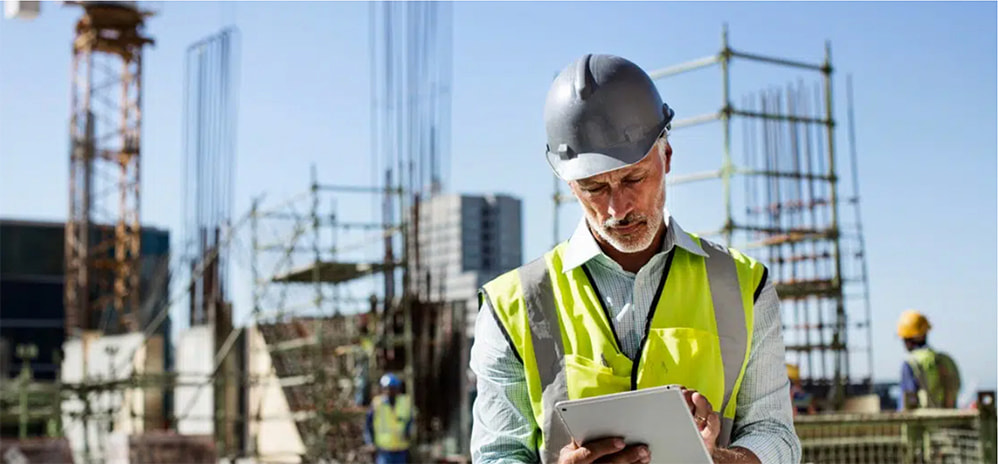
All sorts of businesses rely on inventory to provide goods and services to their customers, but when it comes to construction, supplies and materials are truly essential. Without them, work comes to a halt. To keep costs down and timelines tight, many construction businesses implement an inventory management strategy that relies on inventory control to reduce cash burn without creating unnecessary delays.
What exactly is inventory control? It’s the careful balancing of stocking enough inventory to meet your construction company’s needs without unnecessarily tying up cash — is an essential component of keeping your business running profitably and productively. In this article, we’ll touch on the top nine reasons why practicing good inventory control can save your whole team precious time and money.
1. You’ll always have just enough construction supplies and materials.
Copper, tile, hardwood, steel. Your construction business spends a lot of time and money ordering all the supplies and materials it needs to complete a project. But by practicing optimal inventory control, your business will only need to order just enough supplies and materials to get the job done — plus a little contingency inventory just in case.
Of course, it’s hard to place the perfect order if you don’t know what you need. Take the time to sit down, review consumption over similar jobs, calculate what you really need, account for what you already have left over from previous jobs, and place a reasonable order at the right time. The better your inventory records are, the easier this process — and the more accurate your demand forecasting—will be.
One important tip: Even if your inventory records aren’t in good shape, it’s never too late to prepare for the future. Start keeping better track of what you spend, what you use, and how long it takes to get it. Next time a similar project pops up, you’ll save yourself a bit of time and stress figuring out exactly what you need to begin. You can keep these records in a real file or a digital one, although a digital one tends to be more secure and less likely to be misplaced.
2. You’ll keep a watchful eye on machinery, tools, trucks and other high-value assets.
Your construction business has invested heavily in high-value equipment, machinery and tools. But these assets require vigilant tracking, constant maintenance, and frequent inspection. Plus, if they’re in the wrong place at the wrong time, your team could be looking at a serious slowdown — or even a work stoppage.
While inventory control is all about ordering just the right amount of inventory, you can only practice top-notch inventory control by tracking everything your business owns. And if you’re serious about saving time and money, you might as well add the machinery, tools, trucks and other expensive equipment your company owns to that inventory list. After all, spending all day searching for the right tool can really run up labor costs — and slow down your construction progress — for no good reason.
3. You’ll reduce stockouts and work stoppages by never running out of an item.
Having to send someone to track down a tool or a piece of equipment is a huge waste of resources. And so, too, is stopping work on a project because your team underordered a key material, misplaced it or believed they had more of that item than they really did.
When a stockout occurs, you’ll either have to wait for these materials to arrive at your jobsite, or go out and buy them locally at a potentially higher price. Either way, you’re burning time or money — or both. Practicing better inventory control can help with that. But, to do that, you’ll first need to get organized. The right inventory management system can help your team get a handle on what inventory you need, what you have on hand and where it is.
In fact, the Sortly inventory app actually sends out notifications and emails when an item’s stock levels are beginning to dwindle below a user-determined threshold. If you’re using an inventory system like this, remember to set those alerts with enough wiggle room to receive replenishments on time.
4. You’ll minimize inventory shrinkage with the right surveillance and inventory management systems.
Construction inventory is expensive. The last thing you need is for it to be lost, misplaced, stolen, or damaged. To avoid this, you should abide by all industry standards for storing construction materials, especially if you do business in a harsh climate. You’ll also want to consider securing high-value materials, and adding additional safety measures, such as surveillance or locks, to materials that might be vulnerable to theft.
Once all your inventory is properly stored and adequately secured in the right place, you can use your inventory management system to document exactly where it’s all located. This will save you the time and stress of having to physically search for it — instead, you’ll simply consult your inventory list.
5. You’ll learn to focus on your most important, most expensive inventory first.
Sometimes, tracking every last item your construction company keeps on hand can feel downright overwhelming. If you want to start practicing inventory control, but feel like you couldn’t possibly do it all in one fell swoop, first try focusing on the most expensive, most important supplies and materials you stock.
ABC classification (also known as the 80/20 rule) can help you determine what inventory to focus on first. While usually, this system uses profitability as the main determinant of an item’s importance, you can focus on what’s used the most. This system breaks your inventory into three groups:
- Category A: 20% of your inventory, but the most important or expensive
- Category B: 30% of your inventory, less vital
- Category C: The remaining half (and the least essential) of your inventory
If you’re new to inventory control, starting with the most vital 20% of your inventory can be a great way to begin.
6. You’ll start to identify weak links in your supply chain.
Practicing inventory control is all about keeping your spending at a minimum without slowing work down. Part of that, as previously mentioned, is placing a thorough order for the materials you’ll need to complete a project — or at least push through that first phase — ahead of time. But another component of inventory control is looking to the past to see how you can do even better in the future.
Even if you’ve already calculated key formulas like safety stock and lead time, there’s nothing like the real-life challenges of construction to help you understand how you can do better next time. When a supplier fails to deliver the right light fixtures at the right time, or there are quality control issues with those quartz slabs — your costs will go up, and your timelines will drag on. While these issues were out of your control, they still affect your bottom line.
As you practice better inventory management and better inventory control, you’ll realize how the mistakes of unreliable suppliers (and sometimes, people on your own team) might be affecting your profitability and productivity. Use this opportunity to correct problems, and don’t be afraid to make a change if that’s what’s best for your business.
If you have solid relationships with vendors, but feel they’ve been underperforming, don’t be afraid to have those tough conversations. Sometimes, a little extra attention from your suppliers can make all the difference.
And it’s not just the supply chain, either. During these global audits, you may notice other inefficiencies in your business, whether in shipping, in receiving, in your administrative office, or on the jobsite. Look for answers, offer retraining, and see what can be done to remedy the problem you uncover. Sometimes, a solution is simpler than you’d think.
7. You’ll more easily manage inventory across multiple jobsites.
One of the chief roadblocks construction companies face? Inefficiencies caused by most team members working across multiple locations, far away from a central hub where information, inventory, and assets are stored. Fortunately, there are a variety of systems and solutions that help address the disconnects that have long plagued the industry.
Using construction inventory software that helps you track construction inventory, materials, and equipment can help your team work smarter — together. This is especially true when it comes to inventory. After all, you cannot practice effective inventory control if you don’t have a solid understanding of where any of that inventory is, how much it’s worth, or when you need to reorder more.
While any inventory system is better than none at all, there are certain systems (usually apps, but sometimes, shared spreadsheets) that work better for teams working across multiple locations. Apps that work on phones and tablets are a particularly good choice if your employees don’t have regular access to a computer. Choosing an inventory control solution that works on a smartphone or tablet can help even the most mobile members of your business understand what they’re working with.
8. You’ll happen to streamline your invoice processing, too.
It’s no secret that keeping track of materials, labors, and all the other costs that pour into a long-term construction project is a tall order. While the point of practicing inventory control is to save money by not over-ordering, running a tight ship can actually save you time and money in a variety of other ways — including how efficiently and accurately your accounting team invoices customers.
When you keep airtight inventory records, always know which materials are where, and have a clear understanding of what job used which supplies, your accounting team will be able to generate a more accurate, more detailed invoice to customers in a fraction of the time. This leads to not only your business generating cash flow sooner, but also to happier customers all the more likely to hire you again.
What’s more, you’ll create a solid paper trail of every item you’ve ordered for a given project, should any questions or concerns about line items on your invoices arise.
9. You’ll learn how to predict demand — and stop purchasing materials you don’t need.
Finally, by practicing better inventory control, you’ll continue to uncover exactly what your construction company really needs to get the job done. With every passing week, you’ll place increasingly more accurate orders that minimize waste, increase savings, and save you time, money, and stress by preventing last-minute orders, purchasing supplies and materials at retail prices, or having to wait for hard-to-find supplies.
If you’re practicing perpetual inventory management, you’ll have the benefit of highly detailed inventory records to help you determine what your business does and does not need to complete certain projects. If you’re using using an inventory app or software like Sortly, you can use the customized inventory reports to further inform your forecasts and track usage patterns over time.
Demand forecasting offers a host of benefits, including better budgeting, better-planned storage solutions and more accurate estimates.
About Sortly
Sortly is a top-rated inventory management solution perfect for construction companies looking to practice inventory control. With automated features like customized reports, barcode and QR code scanning, and helpful, automated reminders that alert you when your stock levels have dwindled too low, Sortly can help your business save time, money and stress — all while helping you stay organized across multiple jobsites.