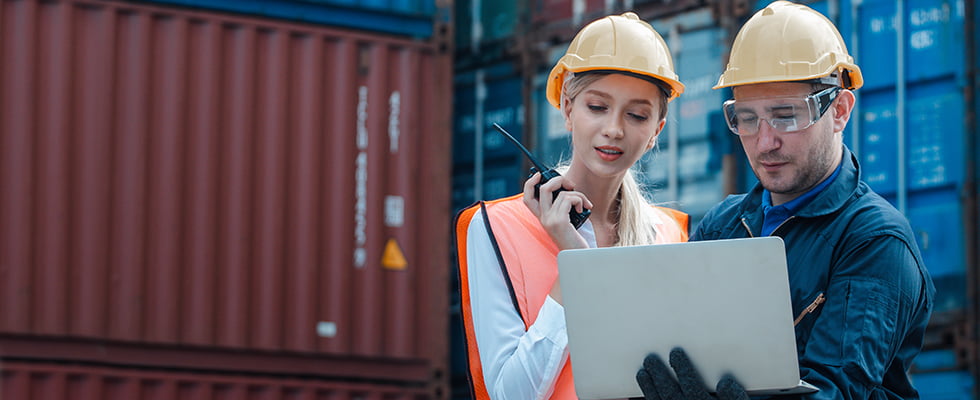
Seemingly relentless volatility and disruption — driven by so many unexpected circumstances (COVID-19, labor shortages, geopolitical conflicts, war) — have caused significant hardships for supply chains. This has been true for every industry, but few have been as broadly affected as the construction industry.
The strength of a construction supply chain heavily depends on other industries — manufacturing, distribution and even retail-commerce — that siphon critical products to contractors and developers. Any compromised link in that chain can hamper the industry, and, over the past few years, all those links have been weakened.
But, though today’s specific circumstances are new to the world, supply chain disruptions themselves aren’t. (Lindsay Moore of TechTarget lists 15 such “snafus,” stretching from 1973 to today.) For construction businesses to stay afloat and remain competitive in the current global market, they must learn the steps necessary for managing supply chain disruptions. We’ll talk about a few of those steps today.
Assess Vulnerabilities
Construction supply chains are naturally complex, and the operating principles that worked in the pre-COVID-19 marketplace may not be as successful today. So, to make future-focused problem-solving decisions, construction firms should step back and revisit the basics of their businesses to find and address vulnerabilities.
Begin this assessment by asking yourself four main questions.
- Where in your supply chain are disruptions occurring?
- Which suppliers are you relying on?
- How “healthy” do those suppliers seem to be?
- How is your budget holding up under the prices of the raw materials and labor you’ve been choosing?
The answers to these questions will help you pinpoint vulnerabilities in your construction supply chain — from suppliers who have run short on inventory to exorbitantly priced raw materials. But, once you’ve found these weakened links, how should you go about fixing them?
Maintain Multiple Suppliers
One of the most pressing issues for today’s construction firms is navigating the global shortage of raw materials — from wood to concrete and everything in between. Calling this a “serious issue” is an understatement. But it can be mitigated by adding more suppliers to your chain.
In the past, maintaining multiple suppliers could have been called an unnecessary complexity, but today it just makes sense. It’s an effective way to safeguard your construction supply chain and protect your business from disruptions and work stoppages. The more options your teams have for sourcing materials, the more you’ll be able to manage supply chain disruptions and steer the firm around obstacles that could otherwise hinder or completely halt it.
Introduce Redundancies
This may seem counterintuitive, but redundancies can strengthen supply chains and promote business resilience. If your budget allows for it, buy raw materials ahead of time and store them until you’re ready to use them. This can help your construction firm skirt the global materials shortage.
Having a storehouse of supplies will also help keep your projects on schedule. With necessary components on hand, you can keep working instead of having to stop, order supplies, and wait for weeks/months for them to be delivered. Playing the construction supply chain waiting game is a preventable issue that quickly drains companies of time and money. (This highlights the importance of investing in a cloud-based business management system. Such software can track inventory in real time for you, so you’ll always know what materials you have on hand and when it’s time to order more.)
Research & Reach Out
How a company goes about managing supply chain disruptions has a lot to do with its location. Certain areas, like large cities, have extremely high construction and materials costs. In more stable economic times, working solely in these areas is a profitable advantage, but, in times like these, the costs can become a major issue. Your budget may not be able to cover materials, and, since customers will likely also be tightening their belts, demand for your services may decrease.
If you’ve found yourself in a situation like this, do some research into the construction markets of surrounding areas. Expanding a business during a period of disruption may seem like the opposite of what you should be doing, but penetrating other nearby markets with lower average costs and/or higher demand may grant you a more stable customer base. In that case, the risk would be worth the reward.
Consider Environmentally Friendly Materials & Practices
Sustainability is paramount for the construction industry, which has historically been a large contributor to greenhouse gas emissions and the release of toxic compounds into the environment. Because of this, construction firms are a major target for regulations enforcing net zero goals or other similar carbon emission reduction plans.
Managing supply chain disruptions means more than simply selecting the best available materials at the most economical price. You will also have to assess your current practices and those of your suppliers to ensure that your teams and the buildings you create will meet regulatory targets.
Construction supply chain disruptions, though frustrating, can mark the perfect time to prepare a carbon reduction plan, outline what materials can be made more environmentally friendly, and determine which workflows should be avoided or revised. Above all, it is critical that you use supply chain issues to build practices that will fuel future growth.
Managing Supply Chain Disruptions With Acumatica Cloud ERP
To help you develop personalized strategies that will accelerate your construction business into a strong, competitive future, Acumatica has created a powerful playbook: “Mitigate Supply Chain Disruption with Acumatica Cloud ERP: Digital Strategies for Modern Supply Chains.” This free resource will teach business leaders:
- How to balance supply and demand
- How to determine the vulnerability of their supply chains
- How 13 advanced supply chain strategies work alongside cloud-based business management technology to overcome disruptions
If you have any questions beyond what the playbook covers, contact Acumatica’s experts today.