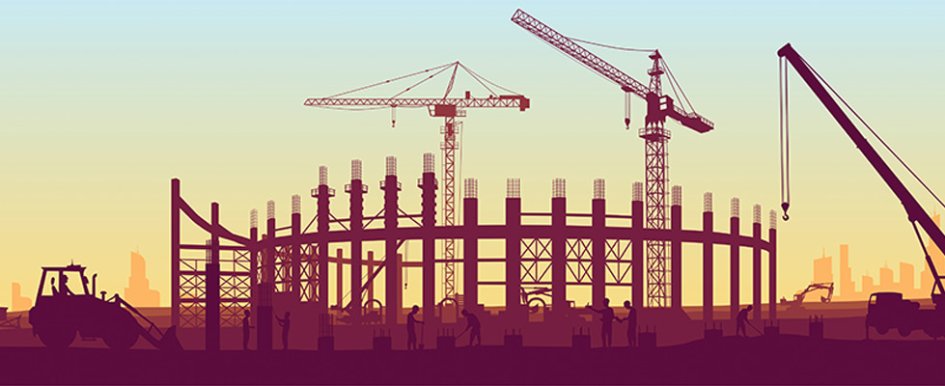
Sustainability is no longer a peripheral concern. Construction businesses are under growing pressure to minimize environmental impact, comply with regulations and meet market demands — all while managing rising costs and economic uncertainty.
Still, sustainability is not just a buzzword — it’s a critical aspect of modern construction. In addition to helping preserve the environment for future generations, implementing sustainable practices can lead to cost savings, improved marketability and compliance with increasingly stringent regulatory requirements.
Emerging policies such as the Federal Buy Clean Initiative and the Inflation Reduction Act (IRA) low embodied carbon program prioritize low-carbon construction materials such as asphalt, concrete and steel for federally funded projects. While these policies currently focus on large-scale projects, they will inevitably influence the broader construction industry in the coming years.
Sustainability must be an intentional commitment and investment, and although each company’s strategy may differ, technology will invariably play a critical role in success.
Leveraging Technology for Sustainable Outcomes
Modern technology is essential for reducing waste and lowering the construction industry’s carbon footprint. Building a greener future also depends on connected, collaborative design and construction workflows that democratize data and eliminate silos.
Connected construction gives the right people access to the right data at the right time so they can detect problems earlier and make informed decisions faster. Breaking down communication barriers and encouraging collaboration and data sharing across project teams will reduce errors, rework and waste through every project phase. In addition, having accurate and timely as-built data before, during and after construction significantly increases efficiency and helps reduce costs.
Before construction begins, software and analytics technology allow architects, engineers and designers to create eco-friendly models while considering other aspects of the project, such as material, water and energy needs. With technological advances, owners and project teams can explore concepts nimbly, without fully defined parameters to make sustainable design decisions. Concepts can be shared across stakeholders for collaboration, ensuring designs are sustainable and constructible.
Constructible data can then inform fabrication and off-site prefabrication for more accurate material estimates and less over-ordering and waste.
Clark Pacific, a California-based manufacturer of prefabricated building systems, uses 3D modeling technology to design and manufacture with precision, and in turn, eliminate waste. During a recent project to manufacture wall panels for Mission Rock Building G, a 13-story, 310,000-square-foot mixed-use building, 3D modeling technology was used to produce machine-ready, constructible designs with lower material requirements. This reduced material carbon by roughly 10% and transportation carbon by 44% because the panels were lighter and easier to transport.
Technology is also impacting sustainability in the field. Viewing 3D models in the real-world environment increases accuracy during site prep and advanced 3D scanning technology generates high-fidelity data for in-field verification for fitment of prefabricated components. These are merely a few ways technology drives sustainability efforts forward by lowering material waste, reducing errors and eliminating rework.
Exploring New Ways of Working
In the effort to build more sustainably, construction businesses like Saunders Construction are testing new technologies and workflows. The company recently completed construction on One River North, a 343,000-square-foot, 16-story building in Denver, Colorado. Saunders used the project to demonstrate and improve its cast-in-place practices by pre-concrete pour scanning.
Traditionally, post-tensioned concrete floors are subject to errors ranging from missing embeds, bollards and planter drains, to misplaced or misoriented connection conduits and light boxes. Conventional quality control methods are typically slow and error-prone with long feedback loops, often resulting in rework and material waste.
Saunders implemented a pre-concrete pour scanning workflow. Using a Trimble X7 high-speed 3D laser scanner, teams scanned each floor of the high-rise before pouring the concrete.
The Saunders team compared the scans to 3D models and drawings to identify any issues they needed to address — all while in the field and within minutes. Progressive scanning allowed the team to uncover and resolve potential issues quickly and, in most cases, before the pour. The estimated return on investment of the virtual design and construction process was 1,164%, with a total cost savings of $505,000 and total carbon dioxide savings of 144,221 kilograms.
An Accessible Path to Sustainability
Construction businesses have a pivotal role to play in a more sustainable future. Reducing the industry’s carbon footprint requires strategic technology integration, collaborative partnerships and continued innovation.
Connected construction is within reach thanks to the emergence of subscription programs that make technology accessible, and technology vendors that prioritize interoperability to democratize data and open the door to collaboration. Utilizing software and/or hardware as a subscription gives construction businesses of all types and sizes — from owner-operators to large general contractors — an opportunity to upgrade or test new technologies without significant up-front investment or long-term commitment.
Taking advantage of accessibility to technology and leveraging digital solutions to enhance efficiency, reduce waste and mitigate environmental impact will help the construction industry build its way to a greener future.