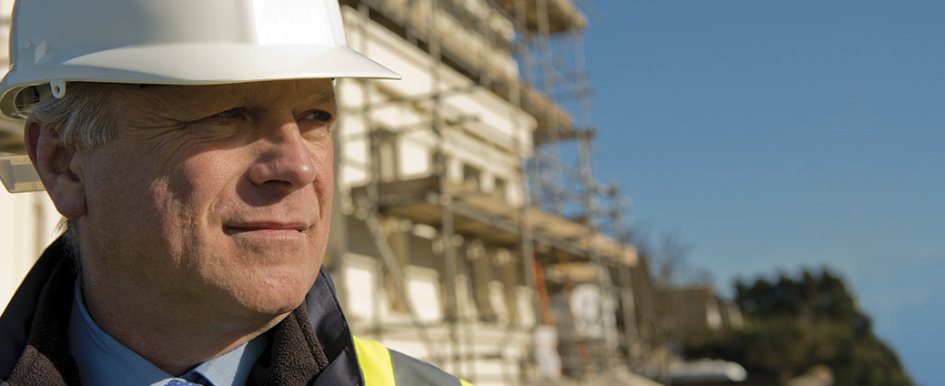
Contractors face extensive challenges in their quest to build and maintain successful businesses in one of the most competitive industries. On a regular basis, you need to bid and successfully complete jobs that achieve acceptable margins, balance demanding and often conflicting work schedules and produce high-quality work, all while ensuring a safe environment that protects your employees, your reputation and the general public. Anything that can provide your company with a competitive edge is worth investigating.
One of the most frequently asked questions from contractors is "How do my safety and risk management controls compare to those of my peers?" From new hire orientation challenges to return-to-work practices, the list of topics that spark the interest of contractors is considerable. A safety peer review is one way contractors can gain a competitive edge by comparing their operations to groups of similar contractors.
How They Work
The data obtained from risk control visits is aggregated by industry SIC code and line of insurance, then further broken down into revenue bands in order to help benchmark safety and risk management practices to a peer group.
The ideal setting for a safety peer review is a meeting with you, your agent and carrier. The aggregated peer group data provides perspective and leads to questions and conversations that can help improve safety and risk management programs.
Availability
Currently, safety peer reviews are available for the five largest contractor segments: general contractors; highway, street and road; utility; electrical; and plumbing-mechanical HVAC. Safety peer reviews are also being developed for other construction operations.
Skilled Labor
Safety peer reviews are great for contractors who are facing difficulties finding, retaining and onboarding new employees. Most of them are surprised to learn that approximately 50 percent of contractor workers' compensation claims result from workers in their first year of employment, regardless of how much previous experience the new worker has in the construction industry. It is not only young, inexperienced workers who get injured during their first year as a new employee. Employees with significant, previous construction experience are equally at risk during their first year as a new employee while acclimating into a new company and new projects.
Case Studies
An electrical contractor with $40 million in annual revenue wanted to compare certain risk management techniques he uses to aggregate data of more than 1,200 electrical contractors. He noted that 41 percent of electrical contractors with revenues between $10 million and $50 million actually had formal return-to-work programs, while his company took a far less structured approach on this important issue. This contractor found it even more compelling that 76 percent of contractors with revenue exceeding $50 million have formal return-to-work programs. These observations prompted the contractor to seek more information and assistance to implement techniques that formalize his company's return-to-work program. The objective was to find efficient ways to lower the direct and indirect costs associated with injured employees who remained out of work when the contractor could bring them back to work in a capacity that produces a favorable outcome for all parties.
Similarly, a large general contractor with annual revenues exceeding $50 million took note of the percentage of peers that have a policy restricting electronics while driving. While this general contractor wisely had a policy that prohibited cellphone calls while driving, its program did not include other restrictions on cellphone use. This led to a discussion with a risk control consultant, who provided additional context around the risks associated with texting while driving. According to research conducted by the Virginia Tech Transportation Institute, texting while driving increases the risk of physical crashes by 23 times that of normal driving. The contractor realized that an immediately effective, enforceable policy around texting was necessary, and the company updated its controls to include a more comprehensive policy.
In a highly competitive environment like construction, it is natural to wonder if you are doing everything you can to help build and maintain success. Comparing your safety and risk management practices to a peer industry group benchmark is a highly effective way to identify opportunities to improve your company's controls and practices. Combining peer data benchmarking with risk management expertise from your carrier and agent can help you build more effective safety and risk management programs. These programs give your company that extra edge on your competition and ensure you are staying current with continuously evolving construction risks, no matter what they are or what they entail.