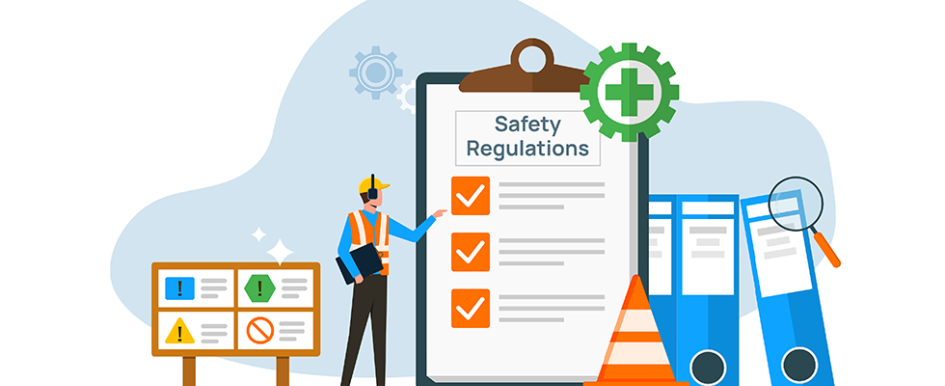
As workplace safety remains a critical focus for business owners in the construction industry, Construction Business Owner (CBO) spoke with safety experts to explore emerging trends, safety culture, and actionable strategies for reducing injuries and costs. Representing Travelers in this discussion are Rich Ives, senior vice president of business insurance claim for Travelers Insurance, and Ken Wengert, vice president of risk control for construction, energy and marine at Travelers.
Together, Ives and Wengert bring decades of experience in managing risk and creating innovative solutions tailored to the unique challenges of construction. Their insights provide a clear picture of current injury trends, the financial impact of workplace incidents, and forward-looking strategies to help contractors foster safer environments in 2025 and beyond.
CBO: How have the most common injury trends changed over the past five years, particularly in high-risk industries like construction?
Ives: Over the past few years, we’ve observed a decline in the frequency of workplace injuries. However, what’s surprising is the increase in severe injuries — those costing over $250,000. This shift is particularly notable given the turnover in the workforce and operational disruptions.
New employees are especially vulnerable, with 35% of all workplace injuries occurring in their first year on the job. In construction, that percentage is even higher — 44% of injuries involve first-year workers. Aging workforce trends also contribute, as older employees tend to have more comorbidities and slower recovery times, increasing the severity of injuries.
Wengert: Rich makes an excellent point. It’s worth emphasizing that this trend is even more pronounced in the construction industry. We’ve also found that the aging workforce and new hires play significant roles in these increased injury severities.
CBO: What measures can business leaders take to reduce the likelihood of workplace injuries, particularly the more severe and costly ones?
Ives: Across industries, the leading causes of injuries remain consistent. Overexertion accounts for nearly a third of injuries, followed by slip, trip and fall incidents at 23%, and struck-by-object injuries at 12%.
In construction, falls from heights are a major contributor to both frequency and severity. These incidents are common in jobsite environments and often result in catastrophic injuries. Employers can mitigate these risks by emphasizing safety measures during onboarding, particularly for newer workers. Ensuring new hires are familiar with safety protocols and encouraging open communication about risks can be transformative.
Wengert: Planning and communication are crucial, particularly for new workers. Employers should think about where materials are delivered, how they are handled and whether mechanical aids can reduce strain injuries. Additionally, it’s important to equip field leaders with strong communication skills to foster a collaborative safety culture.
CBO: Let’s talk about safety culture. What role does it really play in preventing injuries, and how can companies build an effective one?
Wengert: A strong safety culture is foundational to preventing injuries. Leading contractors today emphasize transparency, collaboration, and training. This is particularly important as the construction industry faces challenges attracting new entrants. An open-door policy, where workers feel empowered to voice concerns, is a hallmark of a thriving safety culture.
Ives: I’d add that safety culture shouldn’t just focus on preventing injuries but should also address the response when incidents occur. For example, having a plan for medical care, ensuring access to qualified providers, and encouraging transitional duties for injured employees can significantly impact recovery outcomes.
CBO: How are new technologies influencing workplace safety in construction?
Wengert: Technology offers incredible potential, but its success depends on thoughtful implementation. Businesses should begin by identifying specific problems they want to solve rather than adopting technology for its own sake. Telematics, project management software, and analytics tools can be powerful when integrated effectively.
However, without clear objectives, technology can add unnecessary complexity. Ensuring feedback loops and involving both field teams and management in the decision-making process is essential for success.
Ives: That’s a great point. Technology alone doesn’t solve safety challenges, but when paired with a strong safety culture and leadership buy-in, it can drive meaningful improvements.
CBO: What financial impact do workplace injuries have on businesses, and how can companies manage these costs?
Ives: Injuries have both direct and indirect costs. Direct costs include medical expenses and lost work time, while indirect costs might include productivity losses, schedule delays and higher insurance premiums.
In construction, lost workdays per injury average 103 days, compared to 72 days across all industries. Nearly 50% of all costs come from injuries to first-year employees. These numbers underscore the importance of investing in safety measures and proactive injury management.
Wengert: Rich’s points align with what we see in the field. Indirect costs, like disruptions to team performance and project schedules, are harder to quantify but equally significant. Tools like our Travelers Preferred Network, which connects employers to high-performing medical providers, can help mitigate these costs.
CBO: What roles do psychological and social factors play in recovery from workplace injuries?
Ives: Psychological and social factors — such as anxiety, depression or a lack of coping skills — can increase injury costs by 50%. Addressing these early through tools like virtual coaching can improve outcomes. Employers can also play a key role by maintaining regular, supportive communication with injured workers. This fosters engagement and alleviates fears about job security, which aids recovery.
CBO: As we look ahead to 2025, what trends or challenges do you anticipate in workplace safety?
Ives: Many of the trends we’ve discussed — aging workforce, new employee vulnerabilities and environmental risk factors — are likely to persist. For example, the largest workforce growth is expected among those aged 60 and older, leading to higher rates of comorbidities.
We’re also seeing an increase in severe injuries linked to workforce strain and maintenance issues. These challenges require a continued emphasis on safety culture, proactive planning, and innovative solutions.
Wengert: I’d highlight the importance of leadership development. As more new workers enter the field, investing in future leaders who can effectively manage safety and communication will be essential. Employers must also plan for changing work environments and engage all stakeholders — subcontractors, project owners and suppliers — in safety efforts.
CBO: Any final takeaways for business owners about workplace safety and injury prevention?
Ives: Preparation and prevention are key. Contractors should focus on robust safety and maintenance practices while being ready to handle injuries when they occur. Engaging with employees and prioritizing their well-being pays dividends in both morale and financial outcomes.
Wengert: I’d echo Rich’s points. Additionally, learning from past incidents — both within your company and across the industry — is invaluable. Tools like our injury impact report provide insights that can help contractors stay ahead of risks.