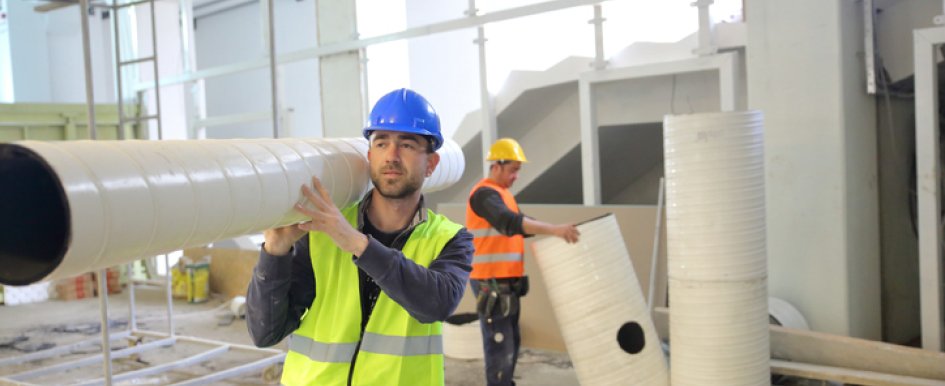
To someone not well-versed in mechanical plant construction, a project that requires the HVAC piping system to be supported only from the floor is rare. Supporting pipe from above is the standard because it leaves space free of obstruction, providing mobility for the workforce executing the project. Creating modular, fabricated skid assemblies is a new concept to most owners and design teams.
For example, consider a project where the design requirement for a 15,000-square-foot mechanical plant requires that all system piping to be supported from the floor. It is not unique to use the floor for some support. It is unique in that support from above was removed as an option. A forest of floor supports is a major obstacle to productivity.
However, on a recent project in Washington, D.C., one construction company used the complication as a way to maximize capabilities; optimize productivity through prefabrication and modular assemblies; and give the owner and design team the best mechanical solution.
The specialty contruction team comprised of project managers, virtual design construction (VDC) specialists, fabricators, logistics coordinators, trucking operators and on-site field personnel created fabricated, modular skid assemblies to house and support all mechanical system components.
These included heating pumps, chilled water pumps, chiller piping connections, condensing boilers, steam boilers, buffer tanks, heat exchanger pumps and a heat exchanger.
However, creating modular fabricated skid assemblies was a new concept to the owner and design team. Therefore, it was essential to get the ownership team behind the proposed solution during the initial planning phase.
Immediately, the crew faced serious implementation challenges. The first issue involved the location of the mechanical room. Typically, mechanical systems are supported by a concrete slab on grade, but since this mechanical room was on the second floor of the structure, additional weight, as well as sound and vibration transmission, were major engineering concerns.
Secondly, on the design side, the team had to ensure the skid assemblies would be fully supported to maintain the structural integrity of the mechanical system, not only in the final resting place, but also during shipment to the jobsite. The skid assemblies would have to travel from the fabrication facility to the jobsite on lowboy tractor trailers, hoisted into the building and rigged to final placement.
Finding a Solution
The mechanical solution began with full VDC coordination. The first step was to break the room layout of mechanical equipment into modular skids, which were as large as possible, liftable, riggable and transportable. In addition, it was important to carefully consider the constructabity restraints in the fabrication shop and the connection obstacles in the field.
The design team contracted a third-party structural engineer to size the framework, support and bracing for all of the skids. Department of Transportation (DOT) trailer load requirements were taken into consideration when it came time to stack skid assemblies on the trailers. Overpass clearances also had to be checked and verified on the delivery route. On the jobsite, the team coordinated with the general contractor and subcontractors to ensure there were appropriate openings in the building to allow hoisting and installation of the skids.
Extensive cross bracing was required to keep skids from swaying back and forth during transportation. All braces had to be drawn and detailed in the building information model (BIM) and coordinated with other trades in order to eliminate clashes and conflicts. To further alleviate the concerns about sound and vibration, the modular skid design placed the steel-framed bottoms of the skids on isolated concrete housekeeping pads.
All modular skid assemblies were prefabricated in a 51,000-square-foot facility in Landover, Maryland, following lean construction principles that minimize waste, maximize time savings and ensure delivery of completed assemblies to the jobsite to help the team stay on schedule. The company’s in-house fabrication shop provides a controlled, safe environment that enhances productivity.
Getting Results
The plan came together and the team executed the work, bringing the central plant to full operation as scheduled. The facilities director was an early adopter of the modular design concept and a valuable team member in bringing the rest of the ownership and design team on board.
In retrospect, there was a considerable number of moving parts in this project, and the need for a great deal of coordination. The success of this project was a testament to the perseverance shown by the entire project team. The VDC team worked well with equipment vendors in overcoming a host of hurdles to bring this concept to fruition.