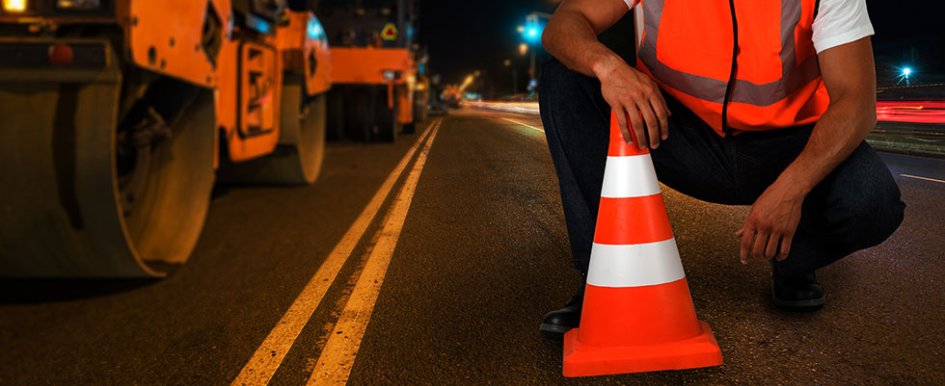
By now, most contractors have heard of “lean” construction; it has clearly gained a foothold in the practices of many contractors. However, according to a recent study conducted by Dodge Construction Network for the Lean Construction Institute (LCI), most contractors are still only lightly engaged with lean, even though increased engagement leads to meeting budget and schedule and improved safety.
To gauge the level of engagement with lean, the study asked general contractors about their use of 29 different lean practices on their projects. The general contractors were recruited from two very different sources: Dodge used its own industry-representative contractor panel, and LCI recruited participants from general contractors that are members of their organization. Not surprisingly, there is a striking difference in the level of engagement between these two groups.
- Over half the general contractors recruited by LCI utilize 25 of the 29 lean practices on at least some of their projects, and 11 of the practices are used by 80% or more.
- In contrast, only two lean practices are utilized by more than half the general contractors recruited from the industry-representative panel, with the most widely deployed practice (production scheduling) only used by 59%.
Based on these findings, this discussion will consider the general contractors from LCI as highly engaged with lean and contrast their findings with those from the industry-representative panel. However, it is worth noting that, even in Dodge panel responses, use of lean is still evident among general contractors. Eleven lean practices are used by 40% or more, and eight additional practices are used by over 30%. This clearly demonstrates some engagement with lean across the industry, albeit at a much lower level than that shown by LCI respondents.
All participants using lean practices were asked about the impact of lean on their projects. Among the general contractors recruited by LCI, 73% reported that their lean projects experienced final construction costs lower than the original budget, 80% found that they stayed on schedule or shortened the schedule on these projects, and 66% said their projects were safer.
Far fewer of the less intensive users of lean practices from the Dodge panel reported these positive outcomes, with only 30% reporting lower construction costs, 38% reporting the ability to meet or reduce their schedule, and 22% reporting increased safety on their lean projects. These numbers demonstrate the value of more deeply engaging in lean. However, it is notable that even these less engaged general contractors more frequently achieved these positive outcomes on their lean projects than on traditional ones, with only 21% reporting lower construction costs, 18% reporting meeting or reducing the schedule, and 14% reporting increased safety on their traditional projects compared with the lean ones.
The fact that even those who are less engaged often experience benefits from lean practices is particularly important because it demonstrates that taking an incremental approach to introducing the practices into your organization will provide some benefits from early on, which will likely only increase as you increase your use of lean approaches.
Given the benefits of lean, perhaps the most important question is what is prohibiting wider use of these practices in the industry, and the study provides some insight. Given the wide breadth of the practices included, perhaps it is not surprising that lack of familiarity is the most widely reported factor preventing the general contractors from the Dodge panel from engaging more with lean on their projects, selected in the top three by 53%. However, it is striking that 47% of the general contractors recruited by LCI for the survey agree that they also face this challenge. The breadth of lean as a practice continues to be an obstacle, even for contractors who are already widely engaged in it.
However, for the LCI respondents, the biggest challenge is a lack of staff with sufficient lean expertise, which is reported by 64%. This is also the second biggest challenge for the Dodge panel respondents. Evidently, the industry is hungry for more internal expertise on lean in their companies.
In addition, the study reveals a more persistent obstacle — one that was revealed in the first lean study Dodge conducted in 2014. The fundamental driver of a commitment to lean construction is often rooted in the perception of the inherent inefficiency of current construction processes and the need to change. Therefore, the understanding that change is needed is an important motivator for increased engagement with lean. The findings still reveal a major gap in that perception: While nearly two-thirds (63%) of the general contractors from LCI rate the U.S. design and construction industry as inefficient, only 30% of those from the Dodge panel agree.
Until this fundamental perception changes, the challenges associated with adopting lean are likely to outweigh the benefits for many general contractors. As the industry faces a looming recession and continues to struggle with worker shortages and supply chain challenges, the increased efficiency offered by lean continue to gain in importance — but first the industry needs to fully recognize the need for change.