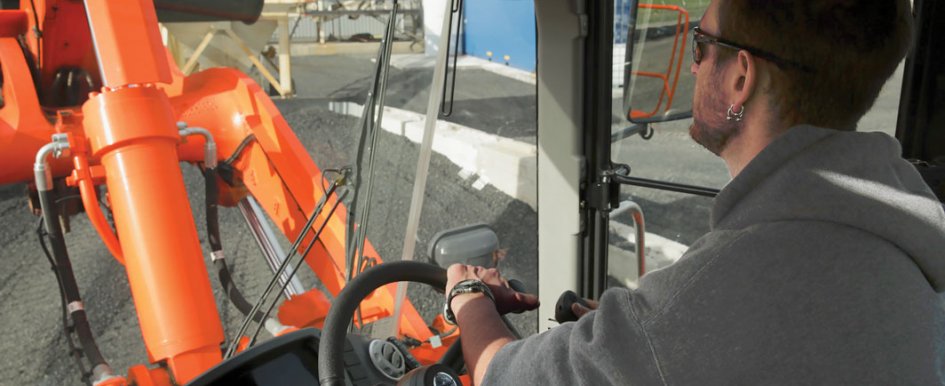
Are your operators tired or stressed? Both of these factors can contribute to a higher rate of accidents. What steps are you taking to help ensure your company’s employees have opportunities to relieve stress at work? Are you giving your operators ample opportunities to rest and rehydrate throughout the day?
Complacency is another leading cause of accidents at jobsites. How many of your operators become complacent with their tasks, then get distracted and don’t pay attention to what they’re doing? Are your operators overconfident about their abilities to perform their tasks?
Risks
The statistics about distracted driving are alarming. According to donttextdrive.com, using a cellphone while driving can be up to six times more dangerous than operating a vehicle while intoxicated, as writing or reading a text message takes your eyes off the road for an average of 5 seconds.
At 55 mph, that’s like driving the length of a football field blindfolded, according to distraction.gov. Imagine your operator under the influence of drugs or alcohol. Then, imagine those effects multiplied. What might happen? A lot can happen in 5 seconds, but there is much you can do to overcome these jobsite safety challenges.
1. Perform Site Inspections
Be mindful of your jobsite, equipment, workers and the environment. If you can, meet with your operators (or ask a superintendent to meet with them) before your crew starts work every day. Walk around the jobsite to identify anything that may have changed since the day before, looking for potential challenges. Then provide advice on how to avoid them.
Are underground utilities clearly marked? If not, be sure to call 811 or your local underground service identifier. If the lines were marked but were later covered by dirt, remark them and make sure your operators know where the underground utilities are buried.
In addition to daily machine maintenance, look for any excessive machine wear that may contribute to unsafe operation. Work with mechanics to repair issues immediately or contact your local dealership’s service department. More than likely, the dealer can dispatch a service technician to make the repairs at your jobsite and get you back to work.
Be aware of low-light times of the day, such as early morning and late evening, when visibility may be hindered. Use proper lighting on machines or bring in supplemental lighting, such as light towers, to properly illuminate your jobsite.
2. Give Safety Briefings
If your company does an annual safety briefing, that’s a good start. Consider increasing the frequency to weekly. Remind operators about the importance of their work and doing everything they can to avoid distractions. Point out safety decals on the machines to remind operators about proper operation.
Follow the recommended service intervals listed in the operation and maintenance manual and follow the proper machine maintenance to ensure your equipment is working as it should be.
Use safety briefings to inspect personal protective equipment (PPE). Does every operator have what he or she needs that day? If not, does your company stock extra items on-site? As an incentive, provide rewards for employees who show up with the proper PPE, as well as incentives to employees who follow safety standards. Encourage workers to come forward if they see someone doing something unsafe and being a risk to others.
3. Provide Breaks
Give operators an opportunity throughout the day to take short breaks. They don’t have to be 15-minute breaks, but you should give operators a chance to get out of the cab and walk around. They can use the time to stretch before climbing back in the cab. It’s also a good opportunity for them to drink water and eat a snack, and follow up on calls and texts. Some companies have banned cell phone use by operators in the cab. Do you have a policy? If so, are you enforcing it?
4. Promote Wellness
According to Carol Keyes, co-owner of the consulting company Complete Health, Environmental and Safety Services Inc., “If workers are healthier and feeling better, they tend to handle on-the-job stress better and will stay more focused on the risks of the job.”
What type of wellness program does your company offer? Do you offer opportunities for employees to perform physical and mental wellness activities? More and more companies are providing these services because the upside is tremendous—when operators bring a positive attitude to the jobsite, they’re more likely to pay attention to their work and help reduce the risk of an accident.
5. Use Machine Cameras
Many of today’s machines come standard with a rearview camera. Sideview cameras may be offered as an option for some earthmoving machines. Put these to use to help operators increase overall visibility.
Chad Cecil, a project manager for Native Environmental LLC in Phoenix, Arizona, says the cameras make a big impact for his operators when they’re using excavators and wheel loaders, particularly when they are performing work in tight quarters. “You can see where your tail swing is coming, and it helps minimize damage to the equipment because you can see how clear you are for your tail swing,” he said.
Distractions will always be a threat to construction equipment operators, but you can take steps to eliminate on-the-job injuries by taking distractions more seriously, implementing steps to curb them and rewarding those who do.