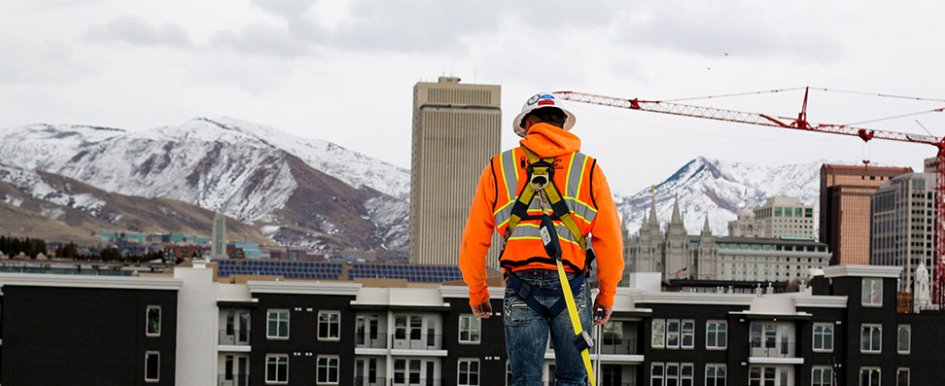
Every year, the same hazard reigns supreme as the leading cause of injuries and fatalities in the construction industry: falls from heights. The U.S. Bureau of Labor Statistics reports nearly 450,000 occupational injuries related to falls annually, and those result in about 1,000 deaths. According to the Center for Construction Research & Training (CPWR), subcontractors are nearly three times more likely than general contractors to face fatal fall incidents with their workers.
Managing the risk of falls on a jobsite is easier said than done. From one day to the next, a construction site can look completely different, and the construction process makes it difficult for workers to access consistent fall protection anchorage locations. If anchorage installation is not part of the preplanning process, safety managers can be asked to provide adequate fall protection with very limited time and resources — which can produce less-than-ideal solutions. While the pressures of protecting profits and productivity rates are very real in the construction world, we must not overlook the importance of incorporating fall protection for construction workers throughout the building process. OSHA 1926 requires construction companies to provide fall protection to workers exposed to falls of 6 feet or greater. This article will offer some methods to provide fall protection at any point in the construction process and raise awareness with crews.
Guardrail
It is very common for jobsites to install perimeter guardrail along unprotected edges. Guardrail is an example of a passive fall protection system, which means it requires no user input to operate. Workers simply need to stay behind a guardrail to remain protected. Guardrail ranks highest on the hierarchy of fall protection controls, after hazard elimination, because it actually prevents falls from occurring. Fall arrest equipment does not prevent falls — it only tries to prevent injury after a fall occurs.
Additionally, guardrails can be constructed right on the jobsite. There is no need to purchase equipment. If a contractor follows the OSHA 1926.502 specifications for guardrail requirements, they will have constructed OSHA-compliant guardrail for their jobsite.
Travel Restraint
Even if a contractor seeks to use guardrail as much as possible to protect their crew, it becomes harder to use as the construction process furthers. When workers are near unprotected edges, utilizing a travel-restraint system can keep the worker in fall prevention equipment. Travel-restraint systems require the user to wear a body harness and connect to a nearby anchorage. If their connection device is a shorter length than the distance to the unprotected edge, the worker is no longer at risk of falling. If they cannot physically reach the edge of their walking working surface, they cannot fall off.
Travel-restraint systems, however, are vulnerable to misuse. If the system is not designed well and a worker is required to reach an area outside of their work zone while connected, they will be tempted to disconnect to finish their job. It is usually in these moments when tragedies occur. The worker would expose the company to an OSHA violation by misusing the system, and could be at risk of falling without any protection equipment. While these systems work excellently in theory, they can prove difficult to ensure users remain compliant.
Overhead Anchorage
If guardrail and travel-restraint options have been exhausted, providing overhead anchorage for tie-off for fall arrest is the next recommended method of fall protection. When working in fall arrest, the worker is subject to fall at any time. If they fall, their gear is designed to orient their body upright, decelerate their fall, absorb the fall forces incurred and then fully arrest the worker before hitting the ground. To help accomplish that process, anchorages should be mounted as high as possible. Higher anchorage locations allow self-retracting lifeline (SRL) systems to activate the moment a fall occurs and reduce the amount of free-fall experience with a lanyard. Free fall is the distance during a fall before fall protection equipment activates.
It may be necessary to install multiple anchorages in a given work area. Workers are subject to swing fall if they walk away from their anchor to work. Swing fall is when a worker swings back toward their anchor point during a fall, and they can potentially come in contact with walls or equipment during fall arrest. Workers should try to work directly underneath their anchor or stay within a 15-degree angle to reduce the chances of swing fall. The higher the anchor is installed, the larger the safe working zone underneath it.
Horizontal Lifeline
While providing an overhead anchorage is ideal, anchors must be installed in areas accessible to workers and near their work zone. To cover very large work areas, many contractors set up a horizontal lifeline system. These are linear fall protection systems that allow a worker to walk a wide span while remaining connected to their anchorage and reducing the chance of swing fall.
A horizontal lifeline spans between two anchor points and can provide fall protection for two to four people, typically. As opposed to single-point systems where users have to disconnect and reconnect into several anchor points along a span, the connection on a horizontal lifeline will follow the worker as they walk underneath the lifeline. Horizontal lifelines are quite common for rooftop fall protection because they can be mounted at a worker’s foot level as well, as long as the minimum fall clearance specified by the manufacturer is provided.
Leading Edge Equipment
Whenever anchorage systems are mounted at a worker’s foot level or anywhere beneath their harness’s dorsal D-ring, users will be subject to increased free fall. Fall protection equipment that is rated for foot-level tie-off is commonly known as “leading edge” equipment and will be required for these scenarios.
In August 2023, the ANSI Z359.14-2021 standard came into effect, creating two new classifications for SRLs. Class 1 SRLs give the user one option for tie-off: anywhere above their dorsal D-ring. Class 2 SRLs give the user two options for tie-off: anywhere above their dorsal D-ring, or anywhere above their feet (technically, no more than 5 feet beneath their dorsal D-ring). Besides a clear labeling difference, there are other physical differences between Class 1 and Class 2 SRLs.
Class 2 SRLs require an additional shock pack between the SRL housing and the snap hook that connects to the user’s harness. This additional shock pack exists to absorb the increased forces that the cable lifeline of the SRL will be subject to when the system is pulled over the roof’s edge. That amount of force to the cable would potentially sever a lifeline from a Class 1 SRL since Class 1 does not have the additional shock pack. Class 2 SRLs are tested to withstand forces up against steel edges that are 0.005 inches in diameter.
Fall Protection Training
A company’s fall protection program will only be as successful as its training program. Workers must be educated on the risks they face while working at heights, and they should also be empowered to follow corporate policies and procedures to ensure their safety and the safety of their coworkers. Employers must prepare crews by educating them on the limitations of their fall protection equipment and provide a rescue plan for workers who succumb to a fall.
Furthermore, OSHA requires fall protection training to be given in a language that the employee can understand. The CPWR estimates that native Spanish speakers are 95% more likely than native English speakers to experience a fatal fall. Providing bilingual training can make sure that everybody on the crew has the same awareness level of the risks of falling during construction.
The old saying goes, “If you fail to plan, you plan to fail,” and that sentiment can ring true when it comes to providing fall protection. With proper planning at the beginning of the project, companies can anticipate fall hazards during the construction process and identify solutions to mitigate them along the way. Selecting the right equipment requires safety managers to be aware of minimum OSHA requirements, communicate with crews about unforeseen complications and make decisions that will provide easy-to-use solution for crews. Fall protection companies can help with training employees, providing turnkey solutions for jobsites and maintaining OSHA/ANSI compliance with your fall protection program.