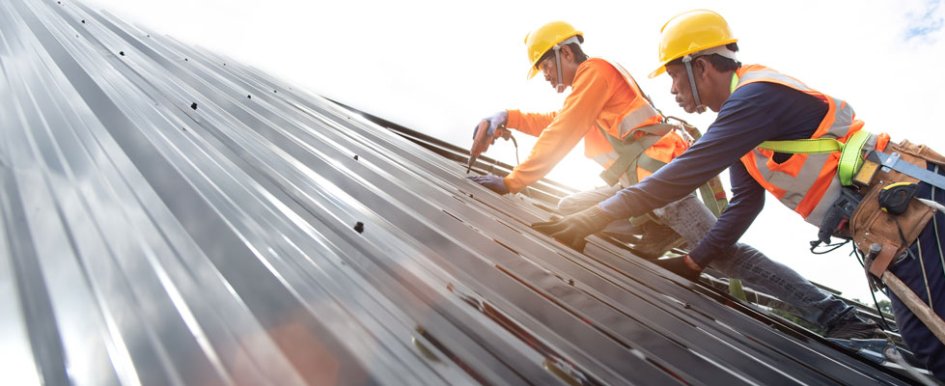
Gathering forensic safety statistics is an arcane science to most and attempts to predict which risks we should to pay attention to based on incidents from the past. In the construction trades, these lagging indicators are unmistakable, and there are four major categories of accidents that reliably compose a high percentage of jobsite fatalities.
The Occupational Safety and Health Administration (OSHA) has bundled these categories into what is called the “Focus Four,” also called the “Fatal Four” for obvious reasons. These four categories follow the leading causes of death in the workplace: opioid abuse, suicide, homicide and transportation fatalities. When any of these incidents occur in an occupational setting, they are classified as work-related fatalities.
OSHA’s mantra of “providing a workplace free from recognized hazards” is a good starting point, or basis, for implementing a program that works to avoid the Fatal Four. Recognizing and adopting this mantra should be followed by identifying possible hazards, a step that is typically missing or buried in the weeds of most safety program agendas.
Hazard identification should be carried out by a “competent person,” which is defined by OSHA as “one who is capable of identifying existing and predictable hazards in the surroundings or working conditions which are unsanitary, hazardous or dangerous to employees, and who has authorization to take prompt, corrective measures to eliminate them.”
Employee safety committees also have a role to play in hazard recognition, and they are particularly effective. But even to most who are not OSHA-verified competent persons, the Focus Four are real, tangible categories of high-risk hazards. They are usually easily recognizable, provided you know where and how to look for them. In order of prominence, they are as follows.
1. Falls
Six feet and above is the recommended height for providing some type of fall protection, of which there are multiple types. Railings and physical barriers are preferred, but a harness and lanyard, self-retracting lifelines, travel lines, etc., all qualify, as well.
Most safety programs are fairly clear on fall protection guidelines, since understanding gravitational force does not require a degree in physics. The equation becomes more complex when scenarios change, openings and holes are cut in roofs, structures are built in stages, etc.
Most of the building trades, especially roofers, receive this message. The high-risk category of deniers (those who ignore the hazard often) include estimators, inspectors and maintenance technicians, who say, “I’m only going to be there a minute, so fall protection isn’t necessary.” Suffice it to say you should pay close attention to this category of people visiting the jobsite.
2. Electrocution
These hazards are ubiquitous and are often in disguise, such as when handling long metal objects when power lines are obscured by vegetation, for example. In fact, OSHA has a couple of videos depicting this exact hazard and accidental contact taking place.
Another example is using a simple tape measure around electrical hardware, such as conduits, light fixtures, junction boxes, etc. The lesson? Do not discount the electrical exposure just because it’s not something you’re typically thought of being subject to due to your job description.
Underground utilities, overhead lines, lightning, arc flash and tree work are also among the most common electrical hazards. Because electricity is about as unforgiving as gravity, this category of hazards needs to be addressed in a definitive pre-work assessment.
The next two categories, while less readily apparent, have combined fatality numbers that are steadily increasing at an alarming rate.
3. Struck-By
This category covers a lot of territory. There are obviously a large number of things one may be struck by. According to Newtonian physics, two bodies cannot occupy the same space at the same time. On the jobsite, it’s usually the human body that loses out when struck. And jobsites are only becoming more complex.
For starters, they are being increasingly mechanized. Examples of struck-by hazards include vehicle or equipment movement, a tool left on a step ladder, unsecured items on a roof, a machine backing up, debris being pitched, poor rigging and hoisting practices, etc.
Growing evidence of attention to this category can be seen in tool manufacturers adding tethers to their product lines and machinery manufacturers adding proximity warning systems, back-up cameras, sensors, telematics and the like.
A good example of preventive strategy can be seen in the state of Virginia’s “Unique Standards,” a safety regulation enacted over 10 years ago that requires a spotter, a camera or the driver to get out and check his backing clearance. Backing fatalities in Virginia significantly decreased after this rule went into effect. Prudence dictates learning from this example and adopting this practice as your own safety commandment.
4. Caught-in or -Between
This category is exactly as gruesome as it sounds. Examples include getting caught by things like outriggers, remote hydraulics, telescoping mechanisms, a counter-weight swing radius, moving machinery or equipment, conveyors, forklifts, backhoes, etc. This is why you see decals and warning stickers on these types of machinery.
The hazards exist in both wide-open and tight clearance areas, near obstructions, with unstable loads, irregular surface conditions, etc., and the outcomes are generally horrific since these workers are not using Lego blocks for materials. The less dense object invariably gets the squish. While this is a hard category to predict on an active jobsite with all kinds of movement, both around and overhead, you would be remiss to neglect putting it on your safety radar screens and making it part of the daily safety briefing.
A thoroughly vetted Focus Four assessment should be built into your job planning process, starting with the estimator’s first look. Every activity and task should include a simple assessment for these risks. The Focus Four should also be a stand-alone chapter in your safety manual and a line item on the job hazard analysis (JHA) and activity hazard analysis (AHS) forms, discussed regularly in safety meetings, part of your safety committee agenda, etc.
Probability statistics indicate that there are limitless possibilities for bad things to happen to good people. By closing off these Focus Four loopholes, you and your workers have a fighting chance of avoiding these hazards entirely, thus ensuring a safe outcome.