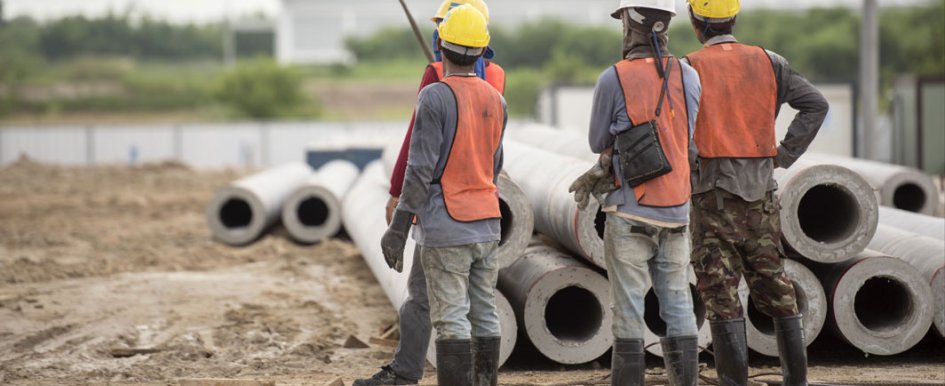
Georgia Power’s Vogtle, a nuclear power plant located in Waynesboro, houses two Westinghouse Advanced Passive 1000 (AP1000) nuclear units, each with about 1,117 megawatts, providing power to homes and businesses throughout the state.
But Georgia Power is aiming at more than providing power to over one million; and they seek to provide clean power, as well. So, in 2017, the company revealed plans to construct two more nuclear units, which would be the first built in the United States in the last 30 years.
With safe and reliable power front of mind, safety and quality were also top priorities for the project—priorities reflected in the company’s contract with Bechtel, an engineering and project management firm known for its safety practices, which are reinforced through its commitment to worker training. For help providing training facilities on site at the Vogtle Plant, Bechtel looked to Xtreme Cube, a manufacturer of custom-built modular structures.
Impressed by the convergence of so many noble aspirations (clean energy, jobsite training and modular construction), CBO chatted with Bechtel project director for the Vogtle project, Brian Reilly, and the chief executive officer of Xtreme Cube, Brandon Main, about their work in Waynesboro. See their insights below.
CBO: Tell us about your company’s work on this project.
BR: In 2017, Georgia Power awarded Bechtel the contract to complete construction of Plant Vogtle’s two new nuclear reactors, Units 3 and 4. These are the only reactors under construction in the country right now and the first to use Gen III+ technology.
Bechtel’s scope is construction completion, so that includes management of subcontractors, craft labor, field engineering, project controls, safety, quality—everything that will deliver two complete units safely and as designed. I’m the Bechtel project director of the Vogtle nuclear power plant expansion project in Waynesboro. I’m responsible for ensuring our team of roughly 8,000 people completes construction of two new reactors safely, as designed, and on schedule.
This project is important for us because, when it’s complete, Vogtle will be the largest provider of carbon-free energy in the country. It will provide clean power to more than a million Georgia homes and businesses.
BM: At the Vogtle Nuclear Power Plant, safety is the No. 1 consideration on site. That being said, large contractors, such as Bechtel, have some of the most robust safety and hazard training programs in the industry. Every jobsite is unique, and the Cube Hazard Training School facilitates training programs for this particular job, where the content is tailored to the specific hazards on the job.
There are a lot of similarities and crossovers between jobsites, but there are also many traits that are specific to one jobsite. The hazards also change throughout the construction phases, and the training is continually adapted to what is actually taking place.
CBO: How did Bechtel use modular buildings for its jobsite training needs?
BR: Bechtel traditionally has new craft professionals attend many hours of safety training during their onboarding process. Afterward, trainees may be assigned to crew mentors or buddies for the first few months they work with us, but we don’t always know the extent of each person’s ability to recognize all safety hazards. Therefore, we do safety "road shows" or "hazard schools" that demonstrate the safe behaviors we’re looking for in response to specific needs.
At Vogtle, we wanted to be more proactive, because a nuclear environment isn’t one where you can afford to make mistakes. We created an interactive safety school with the help of manufacturer Xtreme Cube that all craftworkers go through during onboarding to show their understanding of safety measures in a hands-on environment. They retain a lot more information through this type of training in comparison to a traditional classroom setting.
This idea had been piloted on other Bechtel projects by our company’s innovation team and Bechtel Equipment Operations, but Vogtle was the first to fully deploy the modular building Hazard School into our programming and make it a requirement for all crafts. Having the school already created from its pilot run and sent to us ready to go saved a lot of time and cost involved in creating the hands-on environment we needed.
CBO: Can you say more about the specific safety training that took place in these cubes?
BR: So, in the modular buildings, there are different stations set up for different kinds of safety hazards. Craft professionals rotate between the stations and apply what they know in a realistic setup. We have specialized training personnel lead the half-day sessions, and only so many people are allowed in each session. We’ve run about 1,500 people through the school so far.
BM:The training includes everything from fall protection, electrical safety, lifting and rigging, hand tools, proper use of personal protective equipment (PPE), etc. Very common safety and hazard training concepts, but Bechtel’s specific program is tailored to the specific job they are working on to make the training relevant and effective.
CBO: What have you learned through the use of an on-site, modular-building method of training?
BR: In an industry like ours, where we are continually mobilizing to new areas and recruiting craft professionals with different backgrounds and experiences, it helps us to have something standardized and ready to go so we can quickly re-baseline our safety program wherever we go. There’s less setup time and cost involved since our project team doesn’t have to recreate the Hazard School again and again.
CBO: Have you found that any specific type of contractor is more open to using modular buildings for training?
BR:This is the first time I’ve come across a technique like this for an entire safety program—it’s more often you see something like this in welding, for example.
BM: Generally, the larger contractors have the more robust, in-house training programs that would utilize our modular building solutions. Some of the smaller firms outsource their safety training to companies that specialize in safety training, and, in many cases, it may even be conducted off site. Many times, in the case of the larger projects, the recruiting, training and onboarding all takes place right at the jobsite.
Contractors are becoming more and more accepting of modular building solutions, not only for construction support functions, but they are also using modular building solutions to replace other methods of constructions for the projects themselves.
Other uses for these modular buildings include breakrooms, bathrooms, offices, internal technology rooms, warehouses, maintenance facilities, security stations, lube stations, cool-down stations, warm-up stations, etc.
CBO: What is your No. 1 tip for jobsite training?
BR: Go back to the basics on safety and quality. Ensure everyone has a firm understanding of the basics and feels empowered to enforce them and say something if they see something wrong.