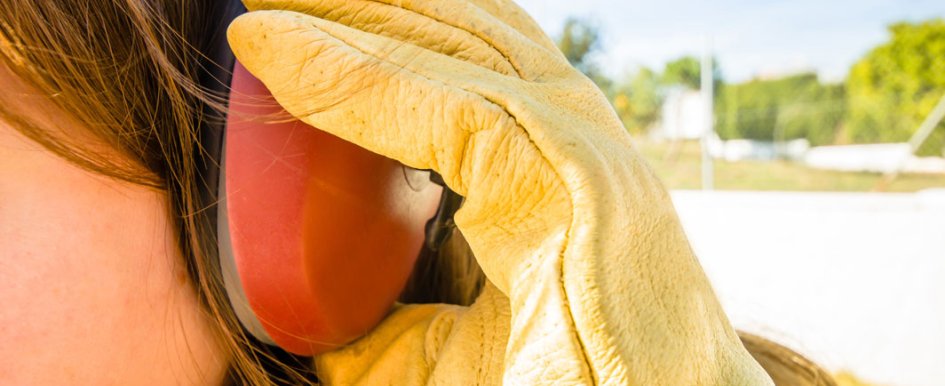
According to the Occupational Safety and Health Administration (OSHA), in 2017, employers were required to pay more than $1.5 million in penalties for not adequately protecting workers from noise exposure; an estimated $242 million is spent annually on workers’ compensation for hearing loss disability; and noise-induced hearing loss (NIHL) affects nearly one in four adults in the United States. NIHL is preventable, but the effect is permanent and can seriously impair a worker’s quality of life.
Thousands of construction workers suffer hearing loss from excessive noise exposure on the job every year. According to a study spanning a decade of research by CPWR – The Center for Construction Research and Training, construction accounted for the second-highest prevalence of workers with a hearing impairment, with at least one in five reporting hearing trouble.
Despite having the duty of protecting employees from workplace hazards that can cause injury or illness, industry employers have no obligation to test workers’ hearing via audiometric testing, even if noise exposure levels exceed OSHA’s permissible exposure limit (PEL). For this reason, hearing loss is rarely recognized as an “occupational disease” in construction.
As such, the Bureau of Labor Statistics (BLS) states that hearing loss is underreported, making hearing loss data for the construction sector unable to be compared with data for general industry. However, the repercussions for the employer who does not seriously consider the auditory welfare of their workforce can be significant, leading to huge payouts in compensation benefits to employees. Measuring jobsite noise exposure levels provides concrete data and pinpoints avenues for improving noisy working conditions.
Noise Monitoring
OSHA sets the legal limits on noise exposure in the workplace based on a worker’s time-weighted average over an 8-hour day. The maximum permissible exposure limit to noise is 90 decibels during the 8-hour day, minimizing the risk of occupational NIHL.
Conversely, the National Institute for Occupational Safety and Health (NIOSH) recommends that all worker exposure to noise should be controlled below or equivalent to the level of 85 decibels for 8 hours. Although NIOSH recommendations are designed to represent a best scientific practice concerning noise exposure, OSHA’s exposure limit is regulatory and is the law that must be complied with.
OSHA standards specify a maximum allowable daily noise dose, expressed in percentages. (i.e., A person exposed to 90 decibels over an 8-hour work shift, will reach 100% of their daily noise dose.) The noise dose is based on both the sound exposure level and sound duration. For each increase of 5 decibels in noise levels, the amount of time the worker is exposed should be cut in half.
By contrast, NIOSH recommends a 3-decibel exchange rate that results in shorter allowable exposures at higher noise levels. See Figure 1 for an example chart of the two in comparison.
In 1981, OSHA introduced a regulation requiring employers to implement a hearing conservation program for workers exposed to an average noise level of 85 decibels or higher during an 8-hour shift. Hearing conservation programs require employers to measure noise levels and provide free annual hearing exams, hearing protection and training.
Employers must also conduct evaluations of the adequacy of the hearing protectors in use, unless the employer makes sufficient changes to tools, equipment and schedules that result in the lessening of worker noise exposure to less than the recommended 85 decibels.
When working to ensure adherence to OSHA regulations on your jobsites, noise level monitoring provides accurate insight into the workers’ environment, identifying where the problem areas are. And doing so through the use of external resources keeps company time and cost burdens low.
If you are keen to train your workforce, there are many devices on the market, but it can be difficult to identify what type of product is most suitable for your working environment and where training is required. A successful noise monitoring program can be carried out on-site by trained health and safety managers, using either a sound-level meter or a dosimeter.
Sound-Level Meters & Dosimeters
A sound-level meter is a hand-held device that enables measurements to be taken at the ear with the instrument pointed toward the noise source. This process must be repeated for both ears, for each duty employees perform, which makes it possible to calculate an accurate record of daily exposure. Settings on these meters can be adjusted according to the type of noise being assessed. Monitors should be calibrated to the ANSI S1.4 standard.
When using a sound-level meter, measurements must be started at the beginning of a task, representing workers’ actual exposure. If workers are likely to be exposed to high levels of impulse noise, emitted from heavy pressing operations or sheet metal working, peak noises must be measured for accurate results and compared to peak action levels.
If individual working patterns are irregular, if the worker is highly mobile, or if the type of work being carried out means it is not practical or safe to conduct noise monitoring with a sound-level meter, noise dosimeters can be used. These are small shoulder-worn devices that will collect individual exposure data.
Dosimeters are worn by employees for their entire working shift. Data is instantly logged and, when downloaded onto another device, details the time history of the noise exposure, highlighting where spikes in exposure occur throughout the day. Workers can also make a diary of times and jobs performed, allowing the employer to instantly see the operations that require more effective noise controls.
It is important to remember that noise dosimeter measurements may be subject to spurious results from employees, especially when first used. High exposures or spikes in the dataset should be checked to see if they are a legitimate part of the worker’s exposure. Modern noise dosimeters can also record the actual audio, which allows the sound to be played back to determine the source.
Worker exposure to potentially damaging noise at work is concerning. What’s equally concerning is some employers’ disregard of NIHL as a legitimate occupational issue, particularly in construction where it poses a major risk. Employers have a crucial responsibility to protect worker health and to upskill their workforce so that employees realize the implications of damaging noise exposure.
Monitoring solutions, like hand-held sound-level meters and noise dosimeters, are an ideal solution for you and your organization to achieve compliance with government standards while effectively and demonstrably protecting your workforce.