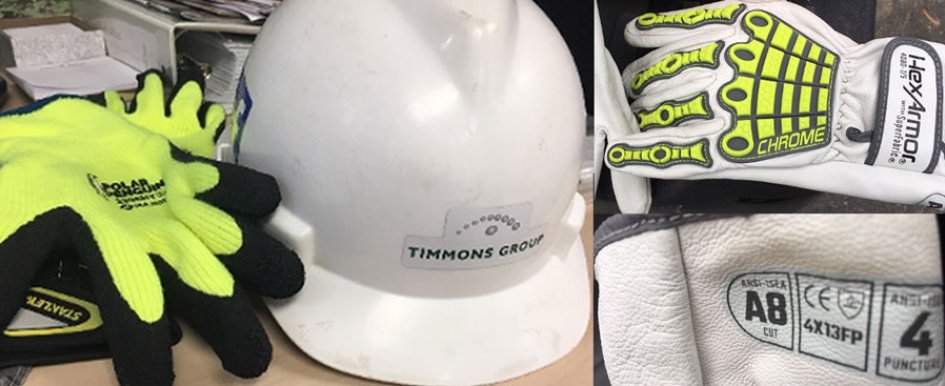
The range of new personal protective equipment (PPE) coming on the market is growing at a fairly steady clip. This is partly due to highly innovative engineering, intensive research and development, new composite and synthetic materials and advanced production techniques.
In this article, we will look at two universal examples of PPE—hand and head protection. According to the rubric of the Occupational Safety and Health Administration (OSHA), these forms of PPE are not actually called “gloves” or “hard hats.” They are correctly described as “hand protection” and “head protection.” This clarification might seem like semantics, but it illustrates OSHA’s line of thought—and there are actually a lot of ways to protect both the hands and the head from jobsite hazards. We naturally default to gloves and hard hats, but in reality, the decision regarding selecting the best protection is a bit more complex.
In the OSHA parlance, “the employer” should ideally perform a “hazard assessment” to “recognize and identify” hazards in the workplace. OSHA offers guidance on something called the “Hierarchy of Controls,” which specifies the order of priority to eliminate or control the identified hazard. Engineering controls are first, followed by administrative controls, and lastly, PPE.
Those working in the construction trades typically default directly to the PPE control, because of the wide-ranging and diverse multitude of hazards on a typical jobsite. Luckily, OSHA has already done the research on these industry-specific hazards, and an assessment form can be found at osha.gov.
Next on the front lines of protection equipment is the American National Standards Institute (ANSI). ANSI is partnered with a group called the International Safety Equipment Association (ISEA). They set the acceptance standards for performance criteria on most articles of PPE. It’s important to note that all PPE is subject to the following minimum requirements:
- Must be paid for by the employer. Keep in mind it’s not a blank check. Reasonable controls apply on employee usage.
- Must be ANSI/ISEA-rated. Task-specific hand protection and hard hats are subject to this requirement:
- Examples include welding gloves, high-cuff rubber gloves, lineman’s gloves, nitrile-dipped and acid-resistant gloves, etc.
- Many other trades require specialized gloves that will carry an ANSI rating for cut resistance, impact protection, puncture resistance, electrical insulating properties, etc. These are called “defined hazards,” and the definition is crucial when it comes to making the call on what those are.
For companies with an active employee safety committee, the selection of PPE is a prime area of involvement for them. Best practices include running an “acceptance trial” to gauge the reception of certain pieces of PPE and solicit feedback.
When it comes to employee training requirements, remember to include care, limitations, inspection, storage, sanitization, etc., and consider shaping a dedicated safety meeting to cover all of your PPE with your employees—whether they are new to the job or veteran team members.
Head Protection
Hard hats are one of the most common articles of PPE and deserve more than passing attention in your inventory of PPE. In the scope of best practices for the selection of head protection, be sure to include the following:
- Select a hard hat that comes in sizes (small, medium or large)
- Human anthropometry (the scientific study of the measurements and proportions of the human body) varies widely. Ideally, so should your PPE. Getting this right will help with worker acceptance and frequent use.
- It also means the hat manufacturer has done their homework and offers a highly engineered product. The cost differences for alternate size hats are usually minimal.
- Head protection can be in a “cap” or “full-brim hat” configuration (often called a lineman’s hat). Ideally, the employee should be able to select their preference of hat style, as this will increase the likelihood of the employee wearing the head protection anytime they are on the jobsite or in a potentially hazardous situation.
- The “cowboy” hat design is also ANSI-approved. In some applications, they also offer sombrero protection.
- A quality hat will serve as a “platform” for additional safety gear. These include face shields, earmuffs, welding shields, sunshade attachments, etc.
- Hat suspension should be easily adjusted, such as with a ratchet wheel setting
- Don’t forget the chin strap, with a 3-pound breakaway force limit to prevent snag hazard. Never permit zip ties or other strong cords for use as chin straps.
- This is important for outdoor work or at-height to prevent dropped-object/struck-by hazards.
- All hats carry a date stamp. Read the hat literature or packaging to determine the recommended service life.
- Keep in mind, the interior suspension of the head protection may have a different service life than the shell.
- Encourage good hygiene practices for all PPE and wash it regularly.
- The application of reflective decals is recommended for front, sides and back of the head protection for increased visibility on the jobsite and in low light conditions.
- Employee acceptance can be increased by personalizing the hat with company logo, name sticker, preprinted sport team logos, project decals, etc.
- Low-profile/high-performance hard hats are becoming more widely adopted, mostly for specialty applications. This includes tower and wind turbine work, steel erection, free-climbing, high-angle technical rescue, confined space entry, etc.
- This design has long been a European and global standard and is now entering wider United States market penetration. The cost difference of this type of hard hat can be appreciable.
- These “hats” are highly engineered for a wide range of jobsite applicability.
- Most of the new styles are vented, offer additional rear and side of head protection, have three-point suspension, are easily adjusted, and offer additional features.
Hand Protection
Hand and finger injuries are on a steady incline and OSHA is taking notice. In response, OSHA recently revised its PPE standard to focus on hand protection. Based on root cause analyses, most hand and finger injuries are clearly avoidable. Here are a few things to consider:
- Defined hand hazards include vibration, burns (thermal and cryogenic), puncture, laceration, impact and crush, chemicals, corrosives and a few others.
- If the average person understood the fragile orthopedic structure of the hand, they would be wearing hockey gloves at work.
- The hand, wrist and fingers are bound with a lot of flexible cartilage, better to accommodate a range of tools, grip configurations, controls, etc.
- When the hand does get mangled in a door or pinch point, the flexibility of that cartilage helps minimize destruction.
- Wearing the right gloves can add an enormous protective measure to the equation. Hand surgery is expensive, and so is the time lost and pain suffered.
Selecting gloves or any other PPE from a catalog or online menu is a borderline practice. Everyone does it, but mostly for convenience. Some best practice recommendations include the following:
- Engage a reliable local vendor to receive a range of PPE options, including industrial glove styles. It would be a good idea for your safety committee to take part in PPE selection and become conversant in the terminology of your PPE inventory.
- “Engineered” gloves will carry a lot of printing on them to attest to their performance and ANSI-acceptance rating. Some clients and general contractors are becoming increasingly specific on which ANSI-rated PPE they require in their jobsite safety plans.
- Glove grip characteristic is very important:
- High-grip material can decrease the amount of force your employees need to control a tool.
- Bare skin has a poor coefficient of friction, as does most leather.
- Nitrile, rubber, composites and synthetics usually provide high grip, increased dexterity and abrasion resistance.
- Some vendors have made it considerably easier to stock a variety of PPE products. You select options from their menu, they bring vending machines to your shop or project and issue a debit card to your employees.
- Large organizations use this system because it tracks use and preferences and allows for ease of restock.
- This dispensing system is not just for PPE, but all kinds of tools, hardware, consumables, seasonal gear, Tylenol, etc.
- Some other relevant best practices for hand protection include:
- Identify and protect pinch points.
- Look for snag hazards and eliminate, identify or protect.
- Instruct employees on how to avoid hand hazards, such as using cheater bars or wrenches, using high force in tight quarters, inspecting tools for wear, defect or other hazards.
- Find safer tools, power tools and/or alternate methods to eliminate manual force requirements.
There is an endless array of PPE options available at varying prices to professionals throughout not only construction, but multiple industrial trades. And when it comes to protecting your employees and providing them with the reasonable and necessary tools and protection they need to get their job done is a responsibility you hold to your business and the clients it serves. Like an individual sustaining an injury, when your employees are hurt on the job, you’ll feel it for a long time.