There are plenty of options available when looking to purchase an air compressor. In fact, it may seem as if there are too many options. What makes the situation even more complicated is that a true side-by-side comparison between compressors is difficult to conduct, since manufacturers often rate their specifications differently. However, considering a few simple factors can help you find a good compressor, even when manufacturers seem to be playing the rating game.
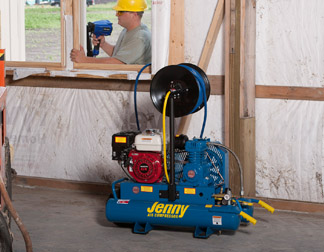
Coming to Terms
When it comes to compressors, there are three main specifications that determine performance: cubic feet per minute (cfm), pounds per square inch (psi) and horsepower. The cfm measures the volume of air that a compressor delivers. The psi indicates the amount of pressure behind the air. Horsepower, of course, represents the power that the engine or motor produces to turn the pump.
It seems simple enough but, unfortunately, things can get a bit more complicated. That’s because there are multiple methods for rating the cfm and horsepower of a compressor. Moreover, there are other considerations, such as service factor and duty cycle, that can also come into play when determining performance. Therefore, buyers should come to terms with the jargon so they aren’t misled to make a poor purchase decision.
Speaking Volumes
The first and most commonly misunderstood compressor rating is . In theory, this could be determined by multiplying the cylinder bore by the stroke and revolutions per minute (rpm). However, the formula only calculates displaced . Due to factors like atmospheric pressure, temperature and friction, compressors actually produce less air than this number implies.
To more accurately measure performance, other rating systems have been developed. For instance, standard gives the volume of a unit according to certain conditions, such as 14.7 psia 60 degrees ambient temperature and zero percent relative humidity. Actual is another rating system that calculates the true output of the compressor at real-life operating conditions.
Because there is no gold standard in the industry for rating , manufacturers are basically free to advertise whichever number they prefer. Some companies choose to be more realistic by rating their compressors with the actual , while others state the displaced because it’s the larger number.
Despite the rating method, the most important point is to not compare apples with oranges. In other words, a unit advertised with a displaced shouldn’t be directly compared with another stating the actual . In this case, the best approach is to ask for the actual of the first unit and then make a fair comparison of the compressors’ air volumes.
The Driving Force
Another specification that often gets confused is horsepower. For gas-powered compressors, this isn’t as much of an issue. The horsepower ratings on these units are fairly straightforward, making comparisons easier. Generally, the ideal solution is to look for an engine with more than enough power needed to turn the pump. Otherwise, if the engine is underpowered for the unit, it will constantly run under high stress, leading to premature failure.
On the other hand, electric motors aren’t as well understood. A person may believe he has a 5.5-horsepower unit when it really only operates at 1.5 horsepower. This is the difference between peak and continuous horsepower.
Peak horsepower is the maximum output that a motor can produce. However, the motor only achieves this level during startup when the start windings are engaged. Once the motor reaches normal rpm, the start windings disengage, and the motor runs at its continuous horsepower rating, which can be 5 to 7 times less than peak horsepower. If the motor was to operate at its peak horsepower longer than the initial startup period, it could overheat quickly and would likely experience a very short service life.
Similar to rating a compressor with displaced , some manufacturers will advertise the peak horsepower because it’s a larger number. Others will state the continuous horsepower. Again, be sure to use the same rating system when comparing units.
In addition to horsepower, the service factor can further infer how a motor will operate under load. This number indicates the percentage of continuous horsepower at which the motor can safely operate. For example, if the service factor is 1.15, the motor can run without issue at 115 percent of its rated continuous horsepower. The higher the service factor, the better the motor is at handling various operating conditions.
Furthermore, take note of the operating rpm. Most electric motors found on compressors will operate around 1,725 or 3,400 rpm. The slower rpm units generally hold more value, since they operate quieter, generate less heat, and produce less wear and tear than faster motors.
Quality Checks
Even if a unit appears to be adequately rated for the task at hand, there are just a few more items to check. By taking note of other compressor qualities, one can get a better sense of whether or not the compressor will live up to expectations.
First, understand that the compressor’s duty cycle will affect its performance on the jobsite. All air-cooled piston compressors generate enough heat that they eventually need to rest in order to avoid overheating. However, some compressors can last longer than others. The best ones on the market have duty cycles up to 80 percent, meaning they can run 80 percent of the time and rest for the other 20 percent. On the other end of the spectrum, lower-quality units may only have duty cycles of 10 to 20 percent.
Another item to consider is the drive system. Is the compressor direct- or belt-driven? Keep in mind that direct drive units may be cheaper, but belt drive compressors generally last longer and are easier to maintain.
In a direct drive system, the pump will turn at the same rate as the crankshaft, which is faster than necessary. Also, direct drives are susceptible to more damage because the crankshaft is coupled directly to the pump. Therefore, if the pump fails, the motor is likely to break down with it, or vice versa.
Belt drive units increase the ratio of how many revolutions the crankshaft makes to how many times the pump turns. In fact, the belt can slow the pump to almost half the speed of the motor, which greatly reduces wear and tear concerns. Furthermore, if either the motor or pump fails, the other component is likely to remain unharmed, and the damaged part can easily be replaced.
Next, analyze the overall construction of the compressor. Are the components made from heavy-duty metal, or are there plastic shields and guards? Are the grease fittings located in protected areas so they aren’t easily damaged? And, if the compressor is belt-driven, is the belt fully enclosed by a heavy-duty guard? These questions can be answered by simply looking at the compressor, but other features aren’t as visible. For instance, one should ask about the construction of the pump’s cylinders. Cast-iron cylinders and linings are regarded as the most durable, while aluminum alternatives are subject to much more wear and tear.
Last but Not Least
Finally, the serviceability of a compressor can add great value. Some manufacturers design their products with wear parts that can be easily replaced. As long as routine maintenance is kept up, these units are likely to withstand thousands of hours of use. And if they actually break down, the compressors can usually be fixed on site or taken to certified dealers for repair. Other products on the market are better suited for noncommercial use and are practically disposable. Once something goes wrong, there are often no servicing dealers or replacement parts available to remedy the problem.
No matter what your compressor needs are, you’re bound to find a wide variety of products that claim to have the solution. However, you can weed out some of the options by understanding the various rating methods and using that knowledge to compare compressors on a level playing field. Then, you can narrow the selection even more by taking into account additional features that reflect the quality of construction. So even if manufacturers try to play the rating game, you can walk away with a clear winner … a compressor that will run for years, producing plenty of air to meet your needs.