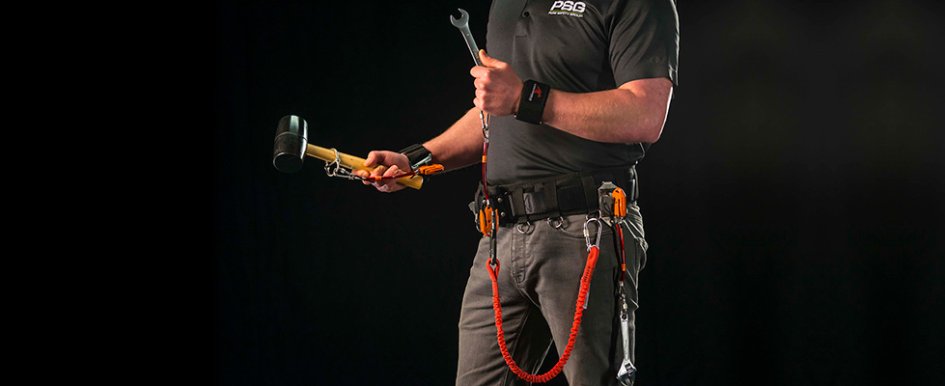
Eliminating the hazard of dropped objects on the jobsite is essential in creating a safe work environment. It’s important to reduce, and ideally eliminate, this hazard at any and all worksites that present a dropped object risk, such as work at heights and work where tools may be lifted to heights.
Safety managers and jobsite supervisors should establish and maintain expectations regarding the prevention of dropped objects prior to the start of work. They should ensure that up-to-date, work-relevant dropped objects prevention training has been presented to all workers, and that workers have been given the latest tool tethering supplies that support their specific worksite activities, especially those performed at height.
Training should include current expectations for compliance to relevant industry best practices and usage standards regarding reducing the risk of dropping an object, which could injure others, contaminate a jobsite (such as in a nuclear environment) and/or damage the structure or other equipment below. Training should consist of an initial course to build awareness and educate on assessing work scenarios and related risks, and how to identify a potential problem. Proper training curriculum includes the following topics, at a minimum: current procedures, the hazards of dropped tools, prevention methods and supplies, proper tool-tethering application and use, and a practical, hands-on tool-tethering exercises. Training should always take place before work begins, and dropped-objects-specific training refreshers should be a regular occurrence for teams, especially those working at height.
As work begins, a proper dropped objects prevention strategy should include periodic assessments and reviews of the effectiveness of the dropped objects procedures for the particular worksite, and appropriate modifications and enhancements to address newly identified risks. Workers play an important role in identifying and eliminating potential sources of dropped objects, given they are the closest to the tasks being performed, and they should be empowered to stop work when they notice an unsafe condition. If a dropped object event were to occur, on-site employees must report the events in accordance to OSHA regulations for reporting an incident.
Tools being used on the site also play a role in the effectiveness of dropped objects safety. They should meet or exceed applicable site and industry standards from the Occupational Safety and Health Administration (OSHA) and American National Standards Institute (ANSI), including the latest standards pertaining to dropped objects. Additionally, a range of tool attachments that will accommodate all tools used at height should be considered when procuring tool-tethering supplies. All dropped objects prevention tools should feature clear and concise labeling and design elements that reduce drop hazards. These design elements include grips integral to the tool, hang holes for use with tool tethers, no sharp edges that can abrade tool tethers, and attachments that are manufactured into tools or tools designed to easily accept a tool attachment. Tools should not be modified using unapproved methods, as tool integrity may be compromised.
Prior to each use, all dropped object prevention supplies should be inspected. As part of a pre-task review, ensure all tools are tether-ready prior to going to height.
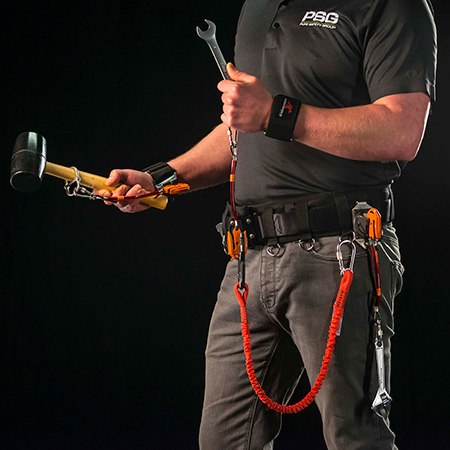
When at height, tool tethers should meet the following criteria: Tethers are not to be loaded beyond the manufacturer’s published weight rating. They are to be used in accordance with all other manufacturer instructions and they should be as short as practical to reduce impact forces, as well as to prevent swing hazards and impact with persons working below. Tool tethers are not to be used in areas where snag hazards or rotating and operating equipment hazards have been determined to outweigh drop hazards. Also, they should be secured both to the tool and the anchor point whenever an object is in use. Holding one end of a tool tether with a hand is not proper tether use. When transferring a tool from one location to another, be sure to always maintain 100% securing. For example, attach the tool tether to the attachment point before removing the existing tether. Avoid using the tool tethering products around sharp edges and never daisy-chain tool tethers together.
When selecting an anchor point, be sure that location is truly fixed, meaning it will support the full drop force that may be exerted on a tether. Ladder and belt loops on jeans are examples of anchor locations that are not truly fixed. Tools and equipment should be anchored to fixed structures whenever possible. The order of priority in picking anchor locations is structure, waist (any center of mass connection such as a belt, harness or vest) and wrist. If a person is selected as the anchor point (waist or wrist), then be sure to tether the smallest amount practical to the worker. It is important to understand that each worker is different and tether-stopping forces can widely vary. General guidance is that no more than 6 pounds should be tethered to a worker. All items that don’t have a practical way of tethering should be contained while not in use. Tools and equipment that are labeled to be tethered should also be contained when not in active use. Containers used should have one or more of a load-rated closure system or integral tethering for all stored tools.
It’s becoming easier to comply with product standards and incorporate the latest in dropped objects innovation as new products are introduced into the market. One such invention is the Quick-Switch tool tether system, introduced by Stronghold, a Pure Safety Group Brand, at World of Concrete 2020. The Quick-Switch is available in North America, the United Kingdom and all major European markets. It is based on the proprietary Quick-Switch design—the only technology that allows workers to switch tools in a single motion while the tools stay 100% tied off at all times. This is a breakthrough in the industry that is not available on other tools.
The Quick-Switch system keeps tools connected at all times, including when they are transferred or handed off. The Quick-Switch system gives workers the flexibility to use multiple tools at their work areas and switch tools, all while keeping them connected through a patented combination of keys, links and anchors. Keys allow the use and manipulation of the tools. Links are the mechanism that allows the switching of locations of tools. Anchors are the points that support the tool in the event of a drop.
The Quick-Switch system components include:
- Quick-Switch Starter Pack that includes everything needed to get started with the Quick-Switch system—Four Quick-Switch Links, one Quick-Switch Bungee Tether and one Quick-Switch Wrist Cuff
- Quick-Switch Link and Dock—Links are paired with tools and are the mechanism that makes Quick-Switch the only tethering system in the world that allows movement of tools from one place to another without ever having to be untied. Each link comes with its own dock.
- Quick-Switch Wrist Cuff
- Quick-Switch Bungee Tether—For tethering tools to a belt or fixed structure
- Quick-Switch Retracting Tether—For retractable applications
- Quick-Switch Apron—For use over handrails and railings
- Quick-Switch Rotating Dock—The anchor point for the Quick-Switch system that can be used on pouches and tool pockets
- Quick-Switch Tethered Tool Bucket and Bolt Bag and Tool Holder to contain anchors
Staying abreast of advancements in dropped objects standards, training, usage and products is essential when working in an environment that requires at-height work or tool transfer. Managers, workers and manufacturers must work together to address and eliminate dropped objects and increase safety on the job.
For more information, visit the Stronghold product web page.