Advanced precision construction technologies continue to proliferate in today’s construction market, but many business owners still associate these solutions with large-scale site prep and road building projects. The truth is that machine control technology is a highly scalable solution, and these systems have now become more accessible than ever before to contractors of all sizes. In fact, there are many market segments where machine control is becoming more and more necessary to stay competitive.
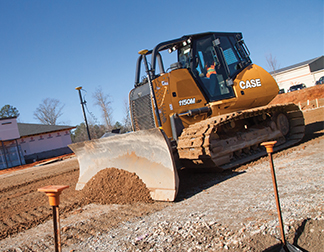
Why Now?
Machine control systems are a great way to invest in the long-term productivity of an operation, and more and more fleet managers and equipment owners are integrating precision construction solutions into their fleets every day.
This technology provides greater predictability and control over job costs, improves productivity and reduces the amount of rework necessary on a jobsite. Over time, intelligent equipment utilization through machine control can reduce the wear and tear on machine components and ground-engaging tools, reduce maintenance costs and fuel consumption, and extend the life of equipment.
Many new machines now come right from the factory with integrated systems that make it easy for business owners to start using these advanced technologies. CASE has recently developed a universal machine control option for its production class M Series dozers. This universal system option makes each machine factory compatible with all major suppliers of precision construction technology for the life of the machine, with no need for wiring harness or mounting points to be changed or altered if a different precision supplier is used during the second or third life of the machine.
The technology has become easier to integrate, but like anything new, it can be a challenge to decide how and when to take advantage of the benefits. The following is an overview of the technology itself, as well as a rundown of the systems available.
The Basics
Machine control is simply defined as the use of integrated on-machine sensors and/or geospatial technology including lasers and positioning satellites—like global navigation satellite system (GNSS) or global positioning system (GPS)—to either indicate or automatically control the machine functions in order to more efficiently achieve production goals. This technology can be divided into two basic categories: guidance/indicate-only systems, and automatic systems.
A guidance/indicate-only system is designed to “indicate” operating parameters to an operator—usually a laser-based system that will beep and/or flash when a predetermined digging or grading parameter has been met or exceeded. Automatic systems are a bit more automatic in nature and require less input or manual control from the operator, and are designed to control the blade or bucket function, physically preventing the operator from exceeding the parameters set for the jobsite.
There are a few ways that business owners can go about integrating machine control into their equipment fleets. Aftermarket/retrofit kits, which can be added to new or used equipment, factory-integrated kits and OEM-ready kits that are integrated from the factory and allow business owners to adopt machine/grade control technologies from any provider—like CASE’s universal machine control solution for dozers.
1D, 2D & 3D Systems—What’s Right for You?
There are several key considerations for contractors when it comes to determining the right machine control solution for their business. Business owners need to consider the site’s current conditions, the required accuracy of the finish work, as well as any potential application issues (complex slopes, etc.). They also need to take budget priorities into consideration, in addition to their existing fleet size. Business owners should also consider their future growth plans when determining the level of investment available for precision construction solutions.
In the simplest terms, 1D systems are designed to regulate single plane grade and slope. 2D systems regulate grade and slope with many variations needed on the work site. The most advanced and capable of the available systems are the 3D systems which regulate grade and slope dependent on the positioning of the machine across the entire worksite, based on GNSS machine position, laser guided sensors or total stations, and changing map/worksite topography.
1D systems are an ideal entry point for contractors who are interested in seeing the immediate benefits of machine control with the lowest cost of entry. Designed to guide basic excavation and grading through indicate-only functions, and simple slope and grade automatic control with manual parameters set by the operator based on their jobsite needs, 1D systems are ideal for digging foundations, some utility work and rough grading.
An example of a 1D system is the CASE SiteControl CoPilot, a simple solution comprised of an inertial measurement unit (IMU), wiring harness and in-cab display. The affordable and easy-to-use system allows operators to set a desired slope/grade reference, and the system automatically holds that slope/grade without the need for lasers, masts or GPS. This allows both seasoned and less-experienced operators to easily achieve and maintain a smooth surface, slope or grade throughout a work area, and can help eliminate the need for additional passes and re-work while reducing fuel costs, labor costs and machine maintenance intervals.
2D systems allow a machine and its attachments to work in two different dimensions—plane and slope. These systems can be both indicate-only or automatic, and are ideal for residential and general construction, drainage work or other more complex commercial excavation projects. 2D grading systems are designed to regulate elevation and cross-slope with the aid of lasers and reference points set for the worksite, and are ideal for mid- to large-sized residential and commercial developments.
3D systems are the most advanced of the three. These systems are comprised of a series of sensors, GNSS masts and receivers with the addition of a base station for good accuracy, or a total station for ultimate accuracy on site that serves as a cross-reference point to locations on the ground. These systems are designed to place the machine precisely within a three-dimensional site plan and provide the highest degree of accuracy, and are ideal for medium to large infrastructure and development projects, industrial sites and large highway projects. Accuracy of the grade can easily be scaled to the need of the jobsite within thresholds as large as a golf ball and as small as a pencil diameter.
Scalability
It’s important to know that most 1D and 2D systems are easily scalable to 3D systems as a contractor’s needs grow over time. Many of the sensors, lasers and other basic components of these systems are integrated into 3D systems as well, so upgrading to a more advanced system is often easier and less costly when the time comes.
Equipment owners and fleet managers should consider their long-term needs and research the scalability of their machine guidance/control systems. Several equipment manufacturers have partnered with technology companies in order to offer some form of grade control option installed direct from the factory. Specifying grade control options direct from the factory not only saves time and money in the long run—by eliminating the future downtime for installation—it also means it’s easier and more affordable than ever for contractors to get started. CASE introduced the Universal Machine Control system, for this reason among many. This allows dealers and customers the ability to bundle in the main harness and mounting points for cents on the dollar compared to ordering the entire system, so the machine will be ready for installation without major retrofitting when the owner is ready to begin their machine control journey.
In addition to eliminating several past barriers to entry for contractors, these partnerships between equipment manufacturers and technology companies also provide advanced system setup, calibration and training through their dealer networks, which helps to ensure that contractors are getting the most out of their investment.
As an example of one of these partnerships, CASE Construction Equipment and Leica Geosystems announced a strategic partnership in 2014 to develop and provide machine grade control technologies—both factory-installed and aftermarket—throughout the CASE line. This agreement includes a commitment to shared product development, which enables the full integration of Leica Geosystems mounting solutions from the factory and professional dealer installation of completion kits on CASE equipment, and expands access and support of machine control technologies through a growing number of CASE Certified Precision Solution Dealers.
Machine control technologies are becoming easier to operate and integrate across fleets of all sizes, and with that comes the possibilities for greater productivity and increased ROI. The costs of more advanced 2D and 3D systems should no longer be seen as a barrier to entry. Owners and operators from worksites on the farm to the municipality to large infrastructure projects are all utilizing these systems and seeing benefits in the way of owning and operating costs, as well as helping to train the new generation of operators, while not sacrificing jobsite efficiency in the name of training.
While some still think of it as a technology that’s only suitable for large-scale projects, the truth is that machine control is a transformative technology for machines of all sizes that can help contractors, fleet managers and equipment owners get onto their next jobsite with greater efficiency and profitability than ever before.
Read More
Click here to learn more about Universal Machine Control.
Watch how one contractor significantly improved his business with machine control.