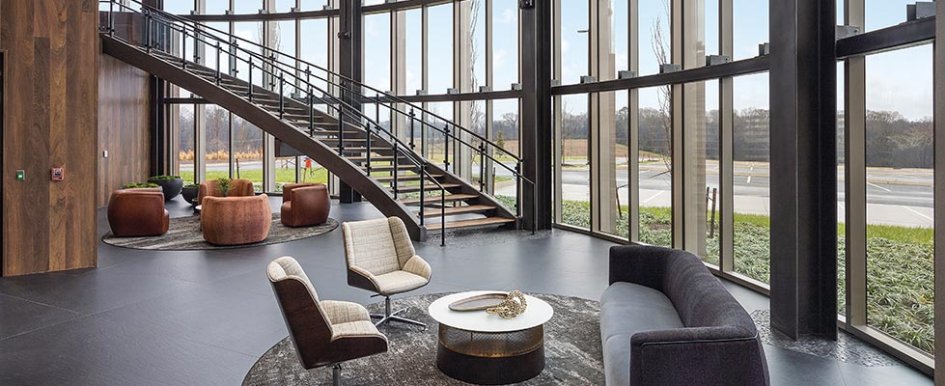
General contracting can be like conducting an orchestra — and just like a musical piece, timing is everything. This is especially true for manufacturing clients, because lost time is lost money. Through extensive planning and coordination, our team at The Christman Company (Christman) used everything from rotating crews to a helicopter to meet ambitious milestones for the construction of the $120 million Smith & Wesson corporate headquarters and operations center in Maryville, Tennessee.
This allowed the manufacturer to begin staging equipment while construction was still underway. Within a year of breaking ground, Smith & Wesson was able to get inside the 620,000-square-foot facility to install conveyor belt and pallet racking systems to avoid any lost time at the distribution hub.
Meticulous sequencing throughout the project led to the best outcome for the client. For example, contractors had to ensure the company’s firing range was immediately operational, since the manufacturer test-fires every firearm before shipping.
We were still running sprinkler lines and electrical in some areas when installation began — along with ongoing construction — so planning, coordination and flexibility became critical. Had we waited until the plant was fully complete for Smith & Wesson to start bringing in equipment, it would have been another year before the facility was operational.
Background & Initial Challenges
A large-scale endeavor such as this project required the integration of various construction phases with the logistical needs of a major manufacturing operation.
The facility, a key manufacturing and distribution center, also serves as headquarters for the company. The two-level building, located on a 236-acre greenfield, includes a 492,000-square-foot manufacturing facility as well as a 128,000-square-foot office building that contains a cafe, gym and commercial kitchen with a pizza oven.
The scope included extensive site preparation, construction of a state-of-the-art building and the early installation of specialized equipment. Unique features included a boardroom ceiling cloud that was designed to mirror a large conference room table made of walnut and buffalo hide. The roof of the office rotunda is topped with the company’s logo that can be seen from the sky, which is especially useful since the plant is near McGhee Tyson Airport in Knoxville, Tennessee. Even everyday items were specialized, including the floor tiles in the rotunda — the largest tiles we’d ever installed at 10 feet long and 4 feet wide.
From the outset, the project faced several challenges, including supply chain disruptions and the need for precise coordination with equipment suppliers.
Contractors had to install an extensive electrical infrastructure with two major electrical rooms to accommodate the equipment, including conveyor systems that move packaging and products within the plant. Supply chain issues caused long lead times for transformers. That meant formulating a plan far in advance to make sure the electrical was ready in time to support manufacturing. The Christman team had rotating contractors working overtime to meet the deadline so the client could begin installing equipment. This necessitated a phased turnover of the building.
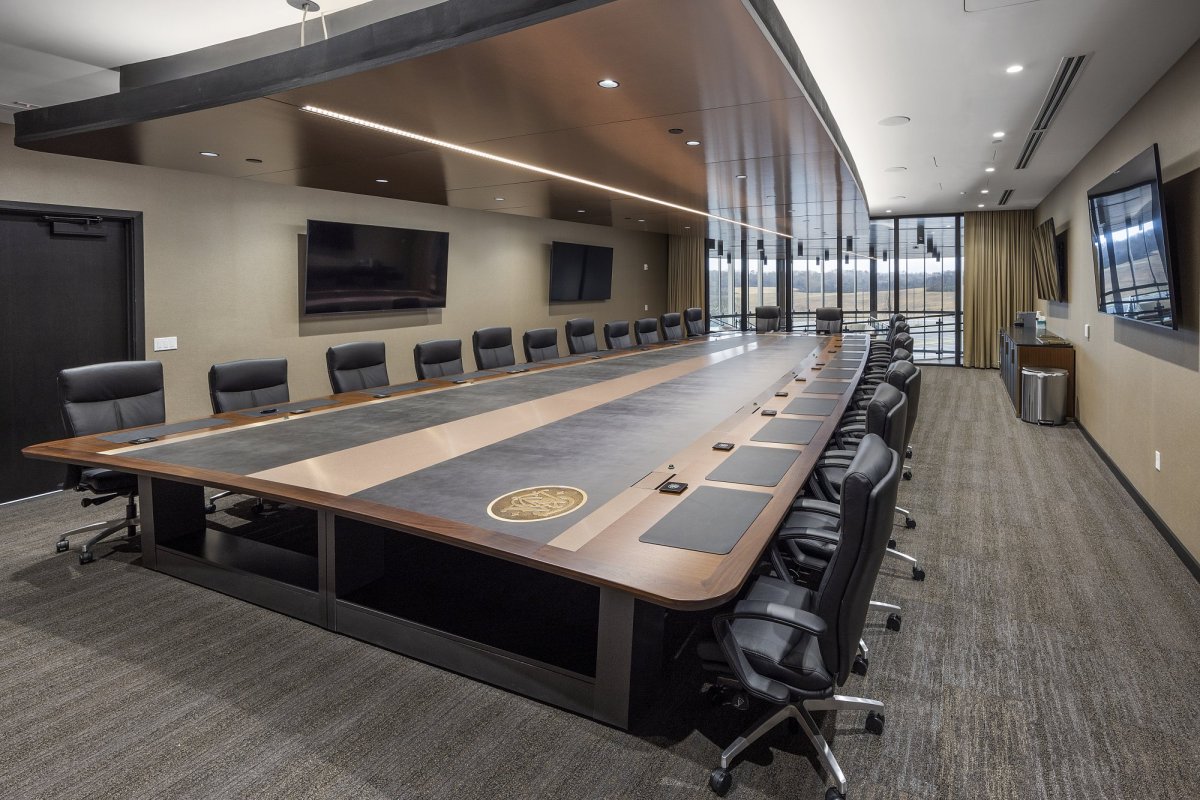
Strategic Sequencing for Early Equipment Staging
To meet the project timeline, our team adopted a sequenced approach. We divided the building into manageable sections and focused on completing areas in a specific order that aligned with the client’s needs. Initially, the plan was to turn over the building in four distinct phases. However, partway through the project, the manufacturer revised its priorities, requiring a resequencing of the construction phases to accommodate changing operational needs.
Our first critical step was to ensure that the building’s envelope was sealed and key areas were prepared for equipment installation by completing the overhead work in the designated sections. The Christman team also had to ensure these areas were safe and ready for the manufacturer, minimizing the risk of damage or injury due to ongoing construction.
Coordination & Communication
Effective coordination and communication are paramount to the success of any project. The construction team held regular meetings with Smith & Wesson and its equipment suppliers to synchronize the construction schedule with the delivery and installation of equipment. The collaborative approach allowed both parties to address potential issues proactively and adjust plans as needed to keep the project on track.
A key aspect of this project was managing the movement and installation of large, complex equipment. The client’s manufacturing process required extensive electrical infrastructure and specialized machinery, which had to be integrated seamlessly into the building. Our team worked closely with the client’s contractors to facilitate delivery and setup of equipment, ensuring that critical areas were accessible and ready for use as soon as possible.
Innovative Solutions & Overcoming Obstacles
The project presented numerous logistical challenges, particularly in terms of managing the movement of equipment and materials within an active construction site. One solution involved using a helicopter to install large fans on the facility’s roof.
The process took about 30 minutes to set all four units. With a crane, that would have taken several days.
Using a helicopter isn’t cheap and doesn’t make sense on every job, but with an expedited timeline it was an easy choice.
Lessons Learned & Best Practices
The Smith & Wesson project offers several valuable lessons for construction business owners, particularly those involved in large-scale manufacturing facilities. Key takeaways include:
- Importance of sequencing — Meticulous planning and properly sequencing construction activities can significantly enhance project efficiency and allow clients to begin operations sooner.
- Proactive coordination — Regular communication and coordination with clients, their contractors and local authorities are essential to align construction schedules with operational needs and address issues before they become critical.
- Flexibility and adaptability — It is vital to adapt to changing client requirements and resequencing work as needed to meet project goals and ensure client satisfaction.
- Innovative problem-solving — Utilizing innovative solutions, like a helicopter for equipment installation, can overcome logistical challenges and streamline the construction process.
- Supply chain management — Anticipating and mitigating supply chain disruptions by securing critical items in advance is crucial to maintaining project timelines.
The successful completion of this manufacturing facility underscores the benefits of strategic sequencing and proactive coordination in construction projects. By allowing our client to stage equipment before the construction was fully completed, the project team was able to expedite the facility’s opening and minimize operational downtime. These practices not only enhanced the efficiency of the project, but also provided valuable insights into managing complex construction endeavors.
For construction business owners, adopting similar strategies can lead to improved project outcomes and greater client satisfaction. As the industry continues to evolve, the lessons learned from the Smith & Wesson project remain relevant, offering a blueprint for successfully navigating the challenges of large-scale construction projects, especially for manufacturers.