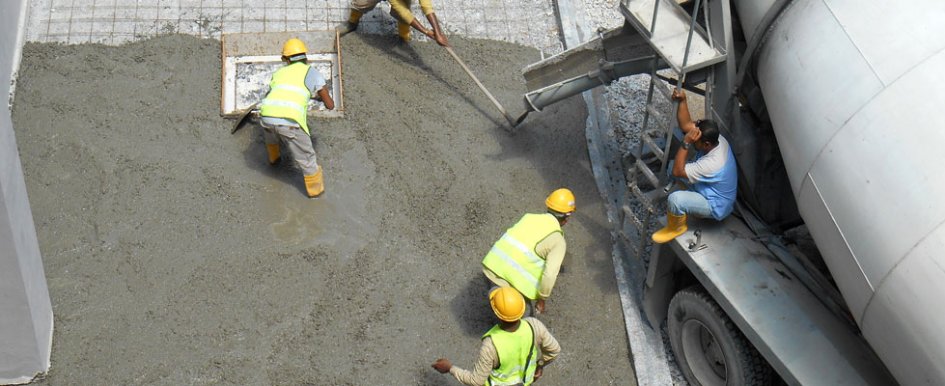
Construction projects are filled with certain risks, ranging from occupational risk to construction defects and property damage to general liability. As more companies begin to operate globally, ordering supplies and raw materials from around the world, they become subject to more risks. In today’s world, many projects face added risks from COVID-19 that can lead to delays and cost overruns.
Technology can help. By performing tests and creating safety-incident documentation, jobsite hazard analyses, getting worker certifications, and providing more employee training, construction businesses can begin to mitigate risks within their organization.
One risk that can be mitigated with technology is concrete yield. Concrete yield is the volume of freshly mixed concrete from a known quantity of ingredients. Ready-mix concrete is sold on the basis of the volume of fresh, unhardened concrete—in cubic yards or cubic meters—as discharged from a truck mixer.
The amount of concrete yield you receive, unload and pour into forms or frames is hardly set in stone. Yield can vary due to factors ranging from air temperature, distance and time traveled to the ratio of concrete, air and water to concrete supplier discrepancies to the way you measure and weigh the delivered product. If you pour concrete and have yield discrepancies, the entire structure can be compromised.
Improve Concrete Yield
Why is it important to measure concrete yield? Contractors measure yield to determine if the concrete supplier has delivered the right amount of concrete. For example, a contractor orders 10 yards of concrete. When the concrete is poured, it comes up short and does not fill the structure as needed.
The contractor will need to perform a yield test to determine if 10 yards were actually delivered. Using a calculation of batch weight and density will determine the volume in cubic feet of concrete you receive.
Another critical number to know? Relative yield. This number determines whether a load of concrete will fill a specific volume in your forms or slabs. You can convert your jobsite yield number to relative yield by calculating your total volume of concrete received divided by the volume the producer intended to provide.
If you find relative yield is 1.00, then these two numbers—jobsite yield and relative yield—are the same. For example, since there are 27 cubic feet in 1 cubic yard, if your relative yield is 27.00, you received the volume the producer claimed was shipped and delivered. However, if relative yield is more than 27.00, you’ve received more concrete, which is a sign that the air content is higher than you have specified.
Keep in mind that a 1% change in air content changes the relative yield by 0.27 cubic feet or cubic yard. If relative yield is lower than 27.00, the air content might be too low for your needs.
Preventing Yield Discrepancies
To prevent concrete yield discrepancies, consider the following tips.
- Check yield using the American Society for Testing and Materials standard C138 unit weight test method on three samples from three different loads (yield is the total batch weight divided by the average unit weight or density).
- Accurately measure volume density by using an accurate, externally clean scale that’s placed on a level surface, remembering that total batch weight equals the sum of the weights of all materials from the batch ticket. You can then reevaluate your volume required towards the end of the pour, provide your estimate to the concrete producer and adjust your order for a few loads to have the optimal amount of concrete. This step helps you avoid the need for short loads after the plant has closed or the nuisance of having to deal with unavailable delivery trucks and costs for returned concrete.
- Estimate any extra concrete you will need. For example, include an allowance of 4% to 10% over plan dimensions for waste, over-excavation, etc. Note that repetitive operations and slips form placement enables you to make more accurate concrete estimates, while sporadic operations, such as alternating placement in slabs, footings and walls, require larger margins of error.
- Construct your forms with enough bracing and shoring (especially if you’re using elevated slabs) to minimize deflection and bulging.
- For on-grade slabs, accurately finish and compact the subgrade to the property elevation.
- Use technology that lets you quickly determine jobsite yield, monitor real-time truck locations and load-level summaries, view records of load status times, and automatically match incoming delivery tickets with hauler pay sheets and invoices. Or take a look at in-truck probes that let you remotely check your slump while it is in-transit so you can quickly recognize and reject out-of-spec loads.
How to Bypass Jobsite Yield Problems
Rather than struggling with concrete sampling and calculations to help you stay on top of your jobsite yield results, explore processes shared amongst all parties on the job. With digital ticket data flowing seamlessly from suppliers to contractors and project owners, the jobsite—and your jobsite yields—stay in sync.
Digital tickets can tell you what jobsite yield you are receiving. If there is a discrepancy, you can find out what happened using the data. With digital tickets, you will be able to browse orders scheduled for the day and future orders for future days. You can also monitor truck locations to receive notifications when a load is on the way, view records of load status times, and automatically match incoming delivery tickets with hauler pay sheets and invoices.