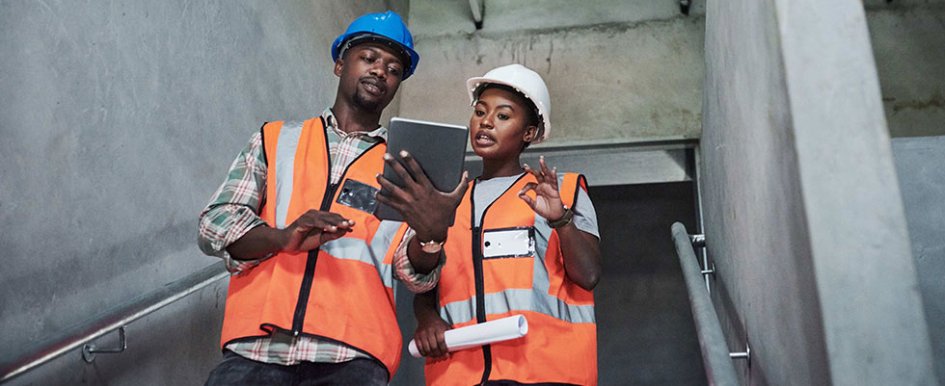
When it comes to construction, “lean” is a hot topic. It serves as a potential playbook for more operational and jobsite efficiencies — which, for construction companies, is a great way to plan to face challenges on and off the jobsite.
The lean game plan has a key concept for a challenge that affects construction companies everywhere: identifying and aggressively confronting waste. Add technology to the plan, and your company is on its way to becoming an unstoppable force in the construction industry. Before removing waste, you’ll need some tools to sift through it.
3 Lean Tools: What to Use to Sift Through the Waste
- Genchi genbutsu — This lean tool gets people to see the “place where it happens.” The Toyota Production System (TPS), for example, is well known for utilizing this concept in their company to make sure any problems, their causes, roots and relevant facts are taken into consideration and observed. For construction, genchi genbutsu is quite simple: Go see it yourself. See the jobsites your company operates on. See your team perform. See where there are openings for any waste.
- Kaizen — This tool brings together your entire team to continue growth, improvement and development. This concept can find ways to identify and eliminate waste while facilitating teamwork across roles and teams. Having collaboration across the organization opens your company up to more solutions, creativity and innovation when removing waste.
- Poka-yoke — This lean tool refers to mistake proofing — making sure mistakes aren’t allowed to happen on and off your jobsites in the first place. Examples are everywhere in construction, from lock out/tag out to clutches on cordless drills. If there is room for error, then your company can take the necessary and informed steps to eliminate that risk.
Adopting these three tools doesn’t require a full-blown lean transformation — but with those tools in your pocket, you can review how waste affects your company. Your team may already use these tools in your company, whether you know the terms or not. If so, good for you: You’re one step closer to dumping waste. If not, it’s easy to implement these tools at your company.
8 Types of Waste & Tech to Confront Them
The eight types of waste plague construction companies everywhere. Remember how I said small improvements can lead to big changes? The same goes for waste. You may have a little waste here and a little waste there, but before you know it, a little waste can turn into a heaping pile of problems.
1. Defects
When you find defects in your work, you waste time and money. Bad estimating takes more time and resources, leading to poor quality. Safety incidents and plan collisions are other defects that put your company at risk. Construction companies do their best to plan to account for as much as possible before the project starts, but we can all do more here. Building information modeling (BIM), estimating tools, safety reporting, and augmented reality (AR) and virtual reality (VR) are technological solutions to enhance your planning. By using these tools, your team can make data-informed decisions that create plans to avoid defects — not respond to them.
2. Excess/Nonvalue-Added Processing
The construction industry pushes a lot of paper and does a lot of manual-data entries. Some warning signs that this waste is present at your company are poor communication, data duplication and reports that aren’t reviewed. What can you do to digitize that information earlier in the workstream? The answer: Make it downstream to use, update and refine to make it easier for your team. Helpful technological tools include enterprise resource planning (ERP) systems, jobsite data vacuums and Power BI. They clean up excess junk, dump it off your jobsites and clean it out of your back office.
3. Overproduction
This is not a common type of waste in construction since the type of work we do naturally limits overproduction, but we can leverage digital tools more to manage supply chains and innovate like manufacturers. Look into your raw materials, tool management and uneven work in progress (WIP) across the job to see if overproduction affects you. While this waste is not common, technology can reduce or remove it like the other types of waste. Supply chain software, accounts payable (AP) solutions for the field and jobsite data vacuums are good tools to tackle this type of waste.
4. Waiting
Waiting is a silent killer to productivity, especially in an industry with time-sensitive delivery commitments. Waiting includes project delays, missed milestones and difficulties collaborating. Ensuring that you’re using modern, digital tools to get your teams coordinating and collaborating is a great way to confront this type of waste. Tech tools like project-management software, digital-collaboration tools and cloud-document-sharing tools get your team on the same page.
5. Inventory
Construction inventory is a way of life for most specialty and general contractors. Having too little inventory often leads to maintaining excess inventory. Be on the lookout for write-downs, too many warehouses for excess inventory and a lack of vendor-managed-inventory (VMI) agreements. Digital tools provide an opportunity to create better supplier relationships that shift more of the inventory-management burden back to your suppliers, where it belongs. Warehouse-management software, ERP systems, AP solutions and vendor scorecards are technological tools to keep better track of your inventory.
6. Transportation
Construction has massively complex transportation requirements. This is one of the reasons the largest and most sophisticated contractors leverage advanced fleet-management tools. Keep an eye out for truck rolls, delivery charges and rush fees that can waste time and money for your company. Use service-management tools, supply chain management tools, ERP systems and short-interval scheduling tools to enhance the transportation of materials and equipment to and from your jobsites and cut back on wasted time and money.
7. Motion
Construction workers are in constant motion, but much of it is not tracked and certainly is not centrally coordinated. Are you tracking elevator rides, truck rolls, back-office inefficiencies and pushing paper into technology? If the answer is no for any or all of these, your company could have a pile of motion waste building up.
Start tracking the amount of motion that happens on a typical project, and you’ll be surprised at the amount of waste. Use cell phones (with features such as step counters/GPS tracking), optical character recognition (OCR) and integrations to track and keep progress moving.
8. Nonutilized Talent
This industry cannot abide nonutilized talent. That further builds waste and crushes your team’s potential. Examine your business for trade-level variances and 40-hour-week variances as they can affect your company.
As the labor crunch continues to impact everyone, there’s an opportunity to use more digital tools to plan and schedule, as well as source, train and retain your talented team members. If you have a strategic initiative to obtain more talent for your organization, you should have a digital tools’ plan to go along with it. Use labor-productivity software, labor-planning software and human resource information systems (HRIS) to your company’s advantage, and give your team the tools they need to shine.
How to Get Moving
Your next step: Bring these concepts and tools into action at your construction company. This is where the game plan comes to life. Start small: Listen, learn and keep track of waste. Once you have a good handle on what has the largest impact on your ability to be efficient, think about copying the playbook of other contractors who successfully leverage modern digital tools to solve these productivity challenges.
With that said, get out of your office, and get to the “gemba: the actual place” where the work happens (like genchi genbutsu). Get your boots dirty and look at your company. What are your business problems, and are they the focus, not technology solutions? Remember: Always tie your technology back to the problem.
Lastly, hold your vendors accountable. Their actions have an impact on your company’s waste. Keep things productive and a part of your playbook. Do that, and your company will have the game plan it needs to be victorious over the eight types of waste.