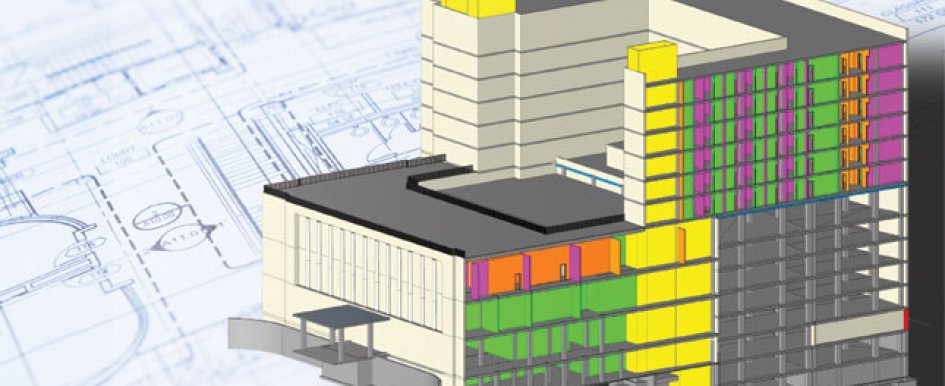
Contractors are hearing a lot about ways to use new technological applications, from building information modeling (BIM) to employing tablets and iPads in the field. One misconception is that only multibillion-dollar corporations are prepared to take advantage of these processes and tools. In fact, smaller construction firms can be more nimble to take advantage of these opportunities faster if they are prepared.
Often when talking about technology, you will hear comments such as “Why should a contractor even look at BIM—isn’t it just for architects and engineers?” or “We can’t afford this stuff.” However, contractors have shown that using BIM processes does create efficiencies and can provide a strategic competitive advantage. The price of bricks and concrete are the same for everyone; how efficiently you deliver them is the key to success.
If you have crossed the first hurdle and realize that the adoption of new technology is necessary for survival in the industry, the next step is to analyze your operations and determine how the technology will benefit your processes the most. Our company recently worked with a contractor whose strength was in self-performed concrete—both vertical and horizontal. When we observed that superintendents and foremen were preparing hand-drawn concrete lift drawings, we helped them automate that process using BIM technology. They developed a BIM-based lift drawing and quantification process used for takeoff and field utilization, which has helped improve their labor productivity significantly. With BIM, you can improve your processes by automating repetitive tasks. When lift drawings are prepared quickly and efficiently, superintendents and foremen are free to spend their time managing the work. Additionally, the BIM model for lift drawings can automatically provide information regarding quantities of concrete and labor hours, saving more time.
The second step in the process is the implementation plan. How will you utilize the technology on a consistent basis? Keep in mind that BIM models provide both a drafting tool and a tool to store, access and use information. So, if you want to create concrete lift drawings, for example, identify the steps and the process flows of creating such a drawing. Then determine how to get the best use out of the BIM model throughout the process. Contractors should develop BIM family components, templates and intelligent objects within BIM models that provide more than a drawing. These components can provide quantities, productivity goals, manpower information, schedule analysis and more.
Some contractors are concerned about potential obstacles involved in implementing BIM processes for the first time in the organization. One common obstacle is the fact that field staff may not believe what the computer can do, or they simply may not want to take the time to learn the technology. The way to work through this resistance is to find the correct team within your company to use the solution initially. Identify a superintendent and project manager who will be open to using the technology. After they execute a project successfully with BIM, encourage them to sell the idea to other superintendents.
As an example, on a hospital remodeling project that was delayed with a complicated permitting process, our company took the opportunity to develop a sophisticated model using BIM for architecture as well as mechanical, electrical and plumbing. All the walls were modeled and coordinated with the MEP so that wall framing could be planned out in detail. The MEP coordination allowed the prefabrication of pipe, electrical and ductwork offsite. The result was a project that was turned over to the owner three weeks ahead of schedule despite having started several weeks late. The other benefit of this effort was that we now had a project team that told every other superintendent and project manager how using BIM saved the project. Superintendents generally listen to their peers more than others trying to convince them of the benefits of new technology.
So, what infrastructure do you need in place to start the implementation process? People are the first piece in the puzzle. When we started, there were two technicians, one with an architectural degree and the other with a technology degree. Both had construction experience, which was essential. But the other characteristic, which we still look for, is a lack of fear of technology. Experimenting with new technological applications will provide the competitive edge for early adopters. Additionally, some of the most successful BIM modelers for contractors have been tradesmen who expressed an interest in technology. Our company’s senior MEP modeler came from the trades and brings that field experience to our modeling team. You should also train your employees at every level to understand the technology your company uses. This is an ongoing investment that requires planning.
Be aware that many of these technicians are part of younger generations and are often not the normal fit in a construction office. You need to be accepting of the need for these people to work with your experienced field personnel to blend technology and construction applications.
High-performing hardware and software are also critical. We recommend running top-of-the-line processors (we use Intel i7) with 32GB of RAM, at a minimum. Sometimes a larger investment may be required. Updating software and hardware will require an annual budget component.
Reviewing successes and failures can often provide significant value. Here are a few lessons our company has learned over the past seven years:
- You will encounter “Bob.” Bob has been building for 30 years and has no interest in computer technology or some young computer “geek” showing him how to build. You will not change his mind with cool animations or visualizations. He needs to see results in the field or hear about successful implementation from his peers. So, pick your implementation teams carefully, and provide direct evidence of the advantages of the technology you are implementing.
- If leadership does not communicate the plan and continually support the implementation of the technology, it will never be adopted throughout the company.
- You need a “pusher.” This is the person who believes in the technology and is not afraid to push upper management to implement it. The pusher should be someone with confidence and experience and who has the respect of the office and the field. A young technician may be too intimidated to walk in the CEO’s office and say, “I have a really big idea, and it is going to cost us $50,000 to try it.”
- Success is difficult to measure. Using BIM processes often provides benefits in the form of avoidance of problems. How do you prove how much you have saved by avoiding problems? Look for measurable items such as productivity and schedule improvements.
BIM does not solve everything. To date, the technology has not been widely successful in providing improved estimating. As an estimating tool, it lacks the ability to take less-quantifiable variables into account. You still need the intuition of a human estimator for this process. BIM does, however, provide an excellent counting tool. The quantities are extremely accurate if the model is constructed properly.
BIM is more about process improvement than software. It is a key to building efficiently, but it will change many of your organizational processes. Be prepared for this kind of change.