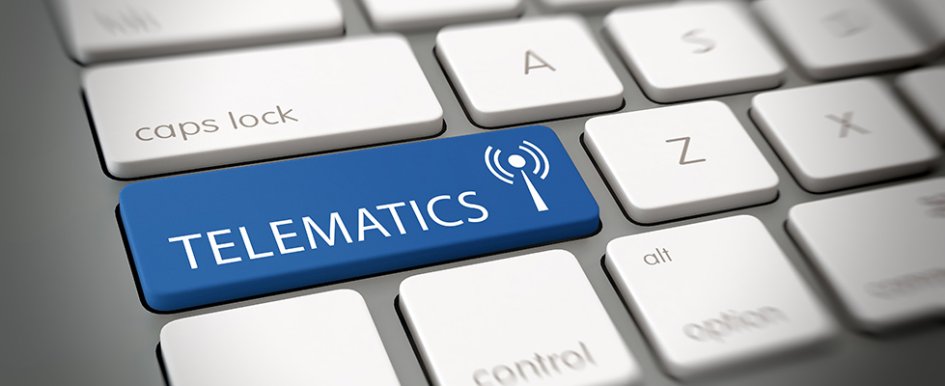
Inflation has taken its toll on the construction industry. Earlier this year, one of the world’s largest equipment manufacturers said the average price of its machinery would jump by 8% globally. Further, in a survey Teletrac Navman recently undertook, equipment operators said that maintenance costs are also growing. According to the findings, 44% of operators ranked maintenance as their highest expense due to inflated part costs and extended periods of downtime.
To combat sticker shock, industry stakeholders are implementing various cost-cutting strategies, turning to equipment leasing and rentals, collaborative equipment sharing platforms and data to understand site and equipment efficiency.
Data has tremendous potential to add financial efficiency to an industry that already operates on razor-thin margins. It can be implemented across the entire project — from planning to building — to make better decisions, improve productivity and utilize assets more efficiently. All these improvements together can have a direct impact on the bottom line.
Telematics, which uses GPS and sensor data to unlock valuable insights on equipment, operates at the front line of the construction site and offers valuable insights about the performance, maintenance and location of construction assets in real time. The Teletrac Navman survey found that construction fleet operators are using telematics technology to lower costs: 97% of telematics users have seen a reduction in fuel costs of up to 40% after implementing telematics, and 45% of respondents report the most significant benefit of their telematics program was the ability to effectively manage resources across jobsites, so that management teams can keep projects on schedule without their budgets slipping.
For example, knowing how and when to deploy a piece of construction equipment is a valuable piece of data to maximize utilization. Equipment that stands idle on a jobsite can be very expensive — and wasteful. A piece of equipment that is down can cost construction companies into the thousands, but you won’t know it’s down if it’s not being tracked. With telematics, construction companies can monitor the entire fleet and know when and how long each machine runs to determine its productivity. Machines used more frequently also need more fuel, maintenance and upkeep. Tracking these metrics allows site managers to cut idle time and fuel consumption, reducing project costs and delays.
Although equipment maintenance is the leading cause of downtime, planned downtime due to scheduled maintenance can be anticipated and incorporated into total costs. Unplanned downtime, on the other hand, is a huge culprit in sabotaging profitability. Telematics can also help in this area by recognizing when equipment needs maintenance through a process known as predictive maintenance. An alert is triggered when a machine’s performance leaves a certain threshold, telling site managers that the machine may need repairs. This way, items can be attended to before a breakdown.
Predictive maintenance often involves combining performance-tracking telematics devices with an artificial intelligence (AI) algorithm that can constantly process and analyze the data in real time.
Finally, construction site theft can cost contractors up to $1 billion each year. Stolen equipment leaves businesses open
to significant replacement costs and higher insurance premiums. With telematics, there are steps that can be taken — such as GPS asset tracking — to keep track of equipment, help prevent unauthorized use and locate equipment in the event of a theft.
In the future, the question won’t be about whether construction is using data, but to what extent data is being used. Those who embrace data will be at an advantage. The right data strategy can contribute to both better return on investment (ROI) on equipment and profits.