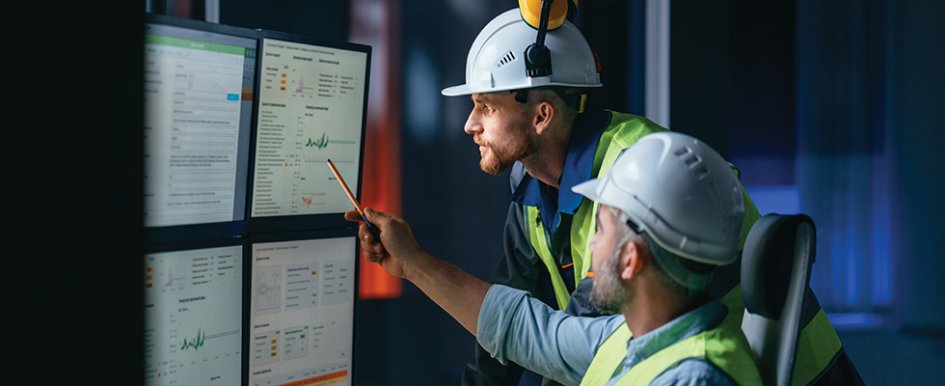
We as an industry have reached a tipping point when it comes to technology and its value across the construction workflow and beyond.
In years past, construction and survey firms have invested in a tool or technique to improve a task with great success. For instance, many now use a total station because it’s far more efficient than using string and tape. But today’s technology-immersed environment dictates a broader perspective that requires a look beyond task-oriented improvements.
The sheer quantity of data gathered by office and field solutions creates a challenge — and an opportunity to reshape productivity, efficiency and what it means to be collaborative in the construction environment.
Foundational Solutions
It might surprise some, but building information modeling (BIM) is more than a design and modeling tool in today’s projects. BIM is fundamentally all about process and collaboration — and therefore a critical piece of digital workflows. It’s a forum for how digital data will be exchanged and reviewed throughout the project life cycle, from design through construction and handover/closeout.
The redevelopment of the Phipps Plaza in Dallas, Texas, by The Beck Group is a good example of the benefits of extending the value of BIM to the field. In this case, The Beck Group was challenged to convert a mall into a mixed-use, upscale property which included a 150-room Nobu Hotel and restaurant, 13-story office building, outdoor event venue and 90,000 square foot athletic facility. To redevelop Phipps Plaza, The Beck Group needed to demolish an existing department store and parking deck to create a new buildable area in roughly the same footprint, all while keeping the existing mall active.
Collaboration and data sharing between the office and the field played an important role in the project from the start. For instance, the same field data gathered by The Beck Group’s field crews to lay out the new structure provided critical insight for the pile installer. In this case, they used a field layout platform with a robotic total station to pinpoint locations from the 3D model and document existing conditions. Using the field layout platform, both crews could make changes that were automatically updated and shared seamlessly across project teams — streamlining work and greatly reducing rework. It also cut the request for information process from two weeks to three days.
To make the best use of BIM for digital collaboration, contractors must have a clear process and guidelines for how digital tools and information standards will be used on the project from start to finish. It’s not just about making sure that everybody has access to digital design, but also how they’re going to share information. For example, “This is how we’re going to sequence things. This is how we’re going to review things to make sure all that sequencing gets put together.”
A Stepped Approach
Moving forward in our new digital reality will require some step changes, the first of which is accepting that technology transformation is critical to increasing productivity and efficiency, and meeting growing demand given workforce challenges that are not going away anytime soon.
Embrace digital technology more and be willing to accept that it is the way the industry is moving — and realize that a digital transformation is not an all-or-nothing endeavor. The really great thing about our current environment is that firms can take small, incremental steps to get started with digital processes rather than trying to do everything at once or diving in too deep initially.
Stutsman-Gerbaz, a multigenerational, family-owned contractor based in Snowmass, Colorado, is relying on a hardware and software subscription model to add 3D grade control systems for its dozers and excavators. Through that investment, the firm is able to expand its 3D model development, drive productivity and expand new work opportunities. On one infrastructure project, the contractor was tasked to complete below- and above-ground improvements such as water line installations. The 3D model was developed in the office and sent to equipment in the field, and at the end of each day, progress was automatically reported back to the office. The team is a month-and-a-half ahead of schedule because they were able to install pipes almost twice as fast — and with greater accuracy than previous methods. That digital data helped build a strong relationship of trust with the engineering and survey company overseeing the project.
The Collaboration Incentive
The Phipps Plaza and Stutsman-Gerbaz examples bring up the third and critical piece of any digital transformation, and that’s the importance of building digital bridges with project partners and owners.
In the past, there’s been little incentive for contractors and trade partners to share digital information. Certainly, the advancement and ease of clash detection has broken down some of those walls — but not all. True digital workflows that drive productivity such as those documented on the Phipps Plaza could not have worked without communication and shared desire for improved processes from all team members.
It’s important that general contractors and trade partners come together to understand what information they need and to look for opportunities to collaborate using technology and drive this new data-driven ecosystem.
The emergence of cloud-based common data environments (CDEs) and cloud-based platforms to facilitate these environments is also helping build these connections. In one case, a construction firm shared its BIM model with all construction related information using a cloud-based CDE. During all phases of the project, the georeferenced BIM model now forms the basis for everything from the estimating to as-built management of required materials and person-hours up to the final settlement. In the earthworks stage, the 3D model is provided to the survey team and operators via a cloud-based data hub. Finally, a mobile scanner maps the newly as-built conditions to deliver a 100% accurate digital twin of the stretch of road to use for maintenance and operation. That’s a digital ecosystem that provides value to the entire project team and even the owner and a clear demonstration of technology’s growing relevance in the built environment.
It’s important for every construction business owner, no matter the size or service model, to embrace digital technology and be willing to accept that it is the way the industry is moving. Develop a strategic digital transformation plan that encompasses a project life cycle that considers your people, processes, partners and customers — and then build it.