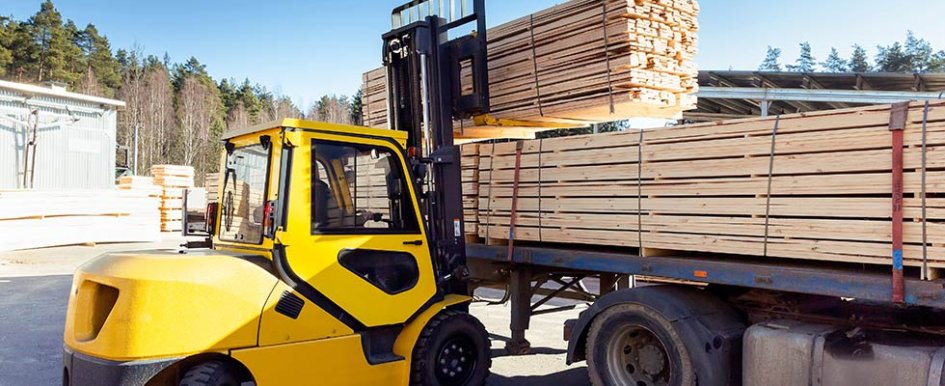
Trees are harvested in the forest or on tree farms by manually cutting the trees with chainsaws or using heavy machinery. Once harvested, the trees are transported to sawmills for processing. The trees are either loaded onto flatbed trucks or rail cars for transport to the sawmill. Trucks are used for shorter distances, but logging companies use rail cars when the trees must be transported long distances.
At the sawmill, the logs are processed into lumber. This involves debarking, sawing and sometimes further processing to create specific wood products. Modern sawmills often use automated machinery for efficiency. The processed lumber may undergo treatment to enhance its durability and resistance to pests or decay. Additionally, the lumber is usually dried to reduce moisture content, making it suitable for various construction applications.
Once the lumber is processed and ready for distribution, it is transported to building product distribution centers, typically by trucks, although rail and shipping may also be used for longer distances or international shipments.
The wood products are stored at the distribution center until they are ready to be shipped to retailers, construction sites or other end users. Distribution centers are crucial in managing inventory and ensuring that products are available when needed.
From the distribution center, the building products are delivered to retailers or construction sites based on orders. This final stage involves using trucks for local deliveries or other modes of transportation for longer distances. Deliveries need to align with project timelines, ensuring that the required materials are available during construction.
Technology for the Forestry Industry
Building contractors, retailers or construction companies place orders with building product distributors based on project requirements. Building product distributors manage their inventory to ensure they have the required stock of lumber to fill their orders. Often, building product distributors use inventory management systems to track stock levels, anticipate demand and reorder supplies.
Once an order is received, warehouse personnel pick the right lumber products from inventory. The lumber is packed securely for transportation, considering factors like size, weight and fragility. Loading procedures consider the type of lumber, weight distribution and special handling requirements.
Trucks are a standard mode of transportation for lumber, providing flexibility and accessibility to construction sites. However, if the distribution center is far away, the lumber may be placed on rail cars.
Shipping forestry products takes a transportation management system (TMS) designed explicitly for this industry. Since lumber is often shipped via multiple modes, the TMS must be able to handle multimodal shipments via truck, rail, barge, etc.
A multimodal TMS will:
- Eliminate manual processes, such as securing carriers, executing orders, scheduling transportation, creating documentation and analyzing results. The TMS will contract with a suitable carrier to deliver to the correct location for the right price. The TMS will provide a coordinated schedule for picking up the lumber, loading it onto trucks or rail cars, and routing it to the correct location so the order arrives on time.
- Incorporate disparate data sources, provide automated functionality to replace many manual or distributed processes, and provide the end-to-end visibility and control needed to optimize logistics operations.
- Track shipments using Internet of Things (IoT), GPS or telematics devices, providing visibility to shippers so you always know where your products are. If an issue arises, such as a truck breakdown, rail car maintenance, a traffic jam or another problem, these devices give immediate insights into the status of the assets so that shippers know what is happening within their supply chain network in real time.
- Perform both shipment execution and visibility across rail, truck, intermodal, barge and ocean shipments, providing unmatched degrees of agility and flexibility. From real-time alerts to interactive data visualizations, a TMS with artificial intelligence (AI) and machine learning (ML) technologies gives organizations the tools to ask more profound questions, predict better outcomes and deliver more impactful results.
- Provide proper documentation, such as bills of lading and shipping manifests. The documentation helps track the origin, destination and contents of the lumber being transported. Treated lumber may be classified as hazardous, requiring the correct documentation and labeling to comply with HAZMAT regulations.
- Manage cross-border shipments. This may include adherence to standards set by organizations such as the International Maritime Organization (IMO) for sea transport.
- Manage alerts. Suppose a shipment is problematic or encounters a problem. In that case, the TMS will alert managers about the issue, providing options to ensure the shipment will continue moving, improving customer service and satisfaction.
- Have an ever-expanding tendering functionality that offers substantial savings compared to older competitive systems that remove the load from each carrier after their time to review has expired. This can save 12% or $110 per load.
A dock scheduling system will allow carriers to check in quickly, get to the loading or unloading spot, complete the process, send proof of delivery, and move to outbound steps like tarping and inspections. Carriers can make appointments with dock scheduling systems to minimize detention times, saving costs.
Safety, Regulations & Compliance
Adherence to transportation regulations, including weight limits, permits and safety standards, is essential to ensure legal compliance and safety during transit. Trucks transporting lumber must adhere to weight limits established by transportation authorities. This includes both axle weight limits and overall vehicle weight limits. Oversized or overweight loads, which may apply to specific lumber shipments, require special permits.
Some distribution center yards use kiosk-type devices that integrate with a TMS to keep truck drivers in the truck, where they will be safer. With a kiosk, the guard at the delivery yard knows certain information before the truck arrives, allowing them to wave the driver into the yard without the driver having to stop and get out of the truck. Even better, the warehouse personnel preparing shipments sees when a truck is approaching the facility before check-in — providing advanced confirmation of the required product staging. Using kiosk functionality within a TMS speeds up the check-in process and reduces on-site time by 30 minutes or more, significantly reducing the total shipping cost.
Sustainable practices are increasingly important in the construction industry. Some companies may prioritize using eco-friendly transportation methods or sourcing lumber from sustainable forests.
Rail cars must follow the standards of the American Association of Railroads (AAR), The Federal Railroad Administration (FRA) and Transport Canada (TC) regulatory compliance requirements. Shippers can’t move their products if a rail car is out for repair. To stay compliant and avoid penalties, rail cars must be maintained appropriately by certified rail shops that can show proper service records. A TMS can house all maintenance records, repair and operational costs, and fleet data, maximizing productivity and ensuring compliance.
Efficient logistics in the lumber supply chain contribute to the overall success of construction projects by ensuring a steady and reliable flow of materials to construction sites while minimizing delays and costs.