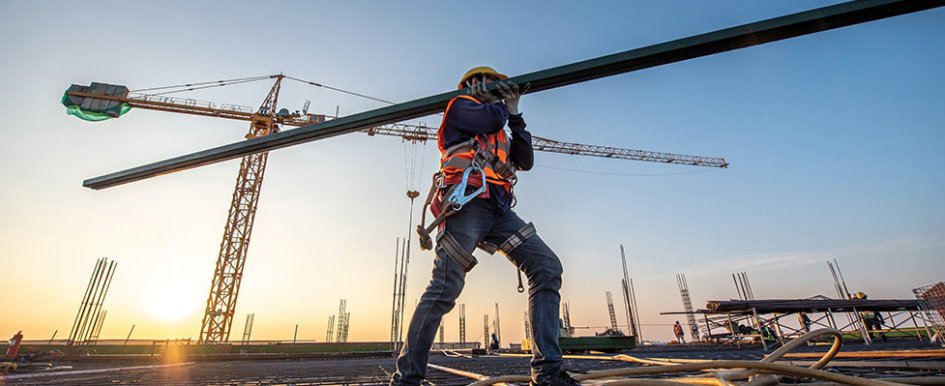
Here’s the thing about construction project delays: It’s not a matter of if they will happen — it’s when they will happen, for how long and why. There are many reasons for a project delay: weather, supply chain hiccups, labor shortages, financing and more. Most of these reasons are out of the control of the project manager or construction business owner, while others are not. The key to project profitability is identifying and addressing the factors that are in your control before it is too late.
Going beyond the “hindsight is 20/20” maxim, there is a way to get ahead of project delays. The obvious option is to use technology, but recent data suggests that technology is one of the primary drivers for delays, despite increased investments in it.
Survey data from iCornerstone reports that in 2016, 15% of construction projects experienced delays, while in 2022, the number rose to more than 28%. Meanwhile, an April 2024 Quickbase survey of nearly 2,000 workers found 66% of their organizations are actively increasing investments in software designed to enhance productivity, work management and collaboration. However, 58% spend less than 20 hours a week on meaningful work that drives results. Therefore, it probably comes as no surprise that 42% of survey respondents reported challenges related to project delays or projects missing delivery times.
Despite having seemingly unlimited technology options to improve efficiency, workers are falling even further behind. Arguably, the sheer volume of apps, tools and platforms may be the very reason for project delays. Here is what is really happening behind the scenes.
The Quickbase survey found that 9 out of 10 respondents report being overwhelmed to some degree by the amount of software solutions they use on a daily basis. This explains why over 45% spend 11 hours — or more — per week chasing down the information they need just to do their jobs.
If your employees are spending more time working and getting less done, consider that their valuable time is being lost to this issue, also known as gray work. And it is not relegated to the back office. The rise in mobile devices and apps used on the jobsite has increased.
According to JBKnowledge, 92% of contractors and construction workers use their smartphones every day at work, and 22% use six or more construction apps. However, only 5% of those apps are integrated, which extends the gray work issue from the office to the field.
Now that you recognize the problem of gray work and its impact on projects, how do you fix it? One way to eliminate this issue is to shift to relying less on the tools and more on connecting the information in those tools. An integrated approach brings data together in a way that makes it easier to manage projects instead of bogging down workers in tedious, repetitive tasks that take up time that could be better spent on more impactful activities.
While many construction business owners have approached this issue using a project management platform, they are finding it limited in terms of reducing gray work. This is often due to learning curves, integration challenges or having to customize parts of the platform for their specific needs. Alternatively, a dynamic work management platform makes the most of existing investments in tech, including project management platforms, by making it easier to access information across the company. Information that is vital to spotting potential delays before they creep up.
Realistically, no technology solution can serve as a crystal ball. Project delays are inevitable, but a dynamic work management platform can reduce gray work and get ahead of delays that are in the construction business owner’s control. These delays are typically:
- Staffing gaps — While technology cannot solve the industry’s persistent labor shortage, it can keep accurate records of certifications, journeyman levels and past project experience. This informs the superintendent’s planning, hiring and assignments, and the right time to bring on subcontractors.
- Local, state and federal requirements — Having project mandates, inspector names, fees and compliance regulations readily available can be a considerable time-saver. Once the information is input into the platform, it can be easily accessed by other crews working in the area, providing an added bump to the time and cost savings.
- Potential accidents — Create an opportunity to decrease jobsite accidents with digital recordkeeping that eliminates paper-and-pencil forms. That leads to knowledge sharing, including near-misses, throughout the company. The information can be used for toolbox talks, identifying and fixing existing processes that can inadvertently lead to mishaps, and safety recordkeeping. As data accumulates, a project manager can dig in to spot trends and get even further ahead on preventing accidents. Additionally, solid recordkeeping is critical in the event of an Occupational Safety and Health Administration (OSHA) investigation.
- Tracking daily progress — Against project plans, daily logs, budgets and the schedule. Oftentimes, these critical sources of data are kept in different reporting systems. When they are brought together, it is easier to get a big picture view and spot potential issues.
- Project reporting — Project stakeholders, both internal executives and the client, expect regular status updates. Telling them the reports are delayed due to employees spending hours tracking down information is simply not an option.
The ability to spot and thwart project delays is considered a win. And if it makes work easier for employees without compromising the quality of the project, it is an even bigger win. This is not a futuristic goal — it can be done now if technology is used in a strategic way.