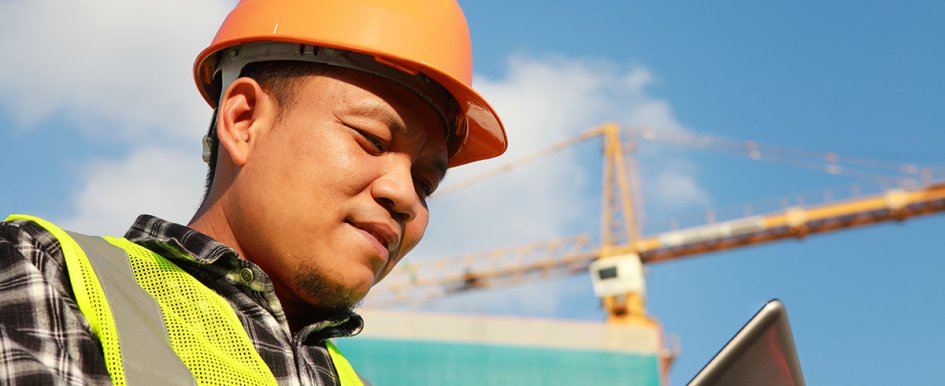
Information is at its best the first second it is available, especially in the construction environment, where projects and the method and time frame in which they are carried out morph and change by the minute. It seems like construction crews and technology are each working head to head to keep up with the other, many times missing the mark that would make a project successful. Reaching this targeted balance of connectivity is crucial to a prosperous construction business. Still, it is no easy task. Acquiring the technology necessary to close the communication gap between owners, contractors and workers is preceded by taxing business decisions when it comes to fit and finances; and training crew members to utilize the technology to its maximum efficiency requires diligence and time. However, any loss of time and/or money is only temporary, as this new connectivity is sure to increase both the lucrativeness and productivity of your construction projects and crews.
Nicolas Mangon, vice president of architectural/engineering/construction (AEC) business strategy at Autodesk, is currently focusing on the global advancement of Building Information Modeling (BIM) and the industry’s digital transformation and move to the cloud. He is also an accomplished structural engineer.
CBO recently caught up with Mangon to talk about how business owners could fully utilize tech solutions to connect the jobsite and ensure that the most up-to-date information possible is being passed from one team member to the next. See his answers to our questions below.
CBO: What issues do you see currently with jobsite connectivity?
The key issue we currently see is a lot of siloes of data. There are a lot of point solutions in the market, but not all of them integrate well with each other. Those siloes increase risk for contractors. If something changes on the jobsite, the drawings are often not updated and any changes are not immediately communicated. If the owner works with architects and engineers to change designs, it doesn’t immediately go to the field because the software is so fragmented. It’s great to have all of these companies building these solutions, but there must be a better process for managing the data. The information needs to be fluid, connected, from the beginning of the project to its completion and handover.
At Autodesk, what we have been focusing on is making sense of all of the different jobsite tech solutions available. We are in the midst of launching a new platform–BIM 360 construction management platform–and we made a number of acquisitions to accompany it. The challenge we had with all of the solutions we acquired – and this isn’t unique just to Autodesk – was they were all built on different platforms.
We have now launched the next generation BIM 360 allowing Autodesk to be the first company in the market to have a fully connected platform to manage data through the entire project process from conception to handover. Autodesk’s integrated solution offers different modules – Design and Build – depending on the team member accessing the information at any given time. What kind of tools does that person need? What information should he/she have access to at any given time? The next generation BIM 360 connects teams and the information they need anywhere, anytime on a single connected platform. Learn more about the BIM 360 solution here.
Returning to the issue of the proliferation of individual point solutions, a single connected platform will become less of an option and more of a “must have” for the project lifecycle. Connecting all of the apps and solutions in one place is increasingly critical to make sense of all the data collected on a site. For example, we have the BIM 360 integration program which currently has 46 completed integrations with more than 90 additional integrations in the pipeline today.
CBO: What will be the biggest challenges for business owners that have yet to implement tech throughout the project process?
If you’re a contractor, time is money. The challenge is that contractors need to stop running for a moment and learn new tools, but in the end, jobsite processes and performances will benefit. Short term pain, long term gain. For some of our clients, adoption has been a bottom-up approach. Someone in the field has a vision for how the site could be run and how tech could help, and he/she drives the adoption of the solution. But sometimes, it’s the executive team leading the charge. Ideally, you want to have both involved in the implementation. It will take time, too. The current construction climate, though, is like the perfect storm for tech adoption—you need a strong infrastructure (mobile technology and the cloud), and then more work/projects and a skilled labor shortage will serve as catalysts for implementation.
The rise of artificial intelligence and machine learning will have a profound effect on the industry. There is so much information related to any given project that it is difficult to make sense of it in real time. With machine learning, you can run data that will make sense of trends and issues with projects. Supervisors and planners in the field will facilitate that, of course.
Additionally, the convergence of manufacturing and the construction industry will radically change the industry in the coming years. Due to urbanization, forecasts for industry growth doesn’t seem to be slowing much. Many companies are already looking at manufacturing approaches to construction, and this number will only grow. Modular construction can create a safer jobsite and less waste overall. Construction projects produce 30 percent of the waste in the world. Modular construction could potentially cut that percentage by approximately 90 percent.
While we see challenges for adoption, the benefits are clear. Our goal with this new platform – and everything we do – is to make construction safer, simpler and smarter in order to help overcome these challenges.
CBO: What parts of the project do you see having the most potential for improvement through the use of tech?
Change management—how a construction team deals with each and every change that comes to them. Tech could have a revolutionary effect on how real-time information is circulated throughout a jobsite. That’s been the goal with BIM 360 from the very beginning.