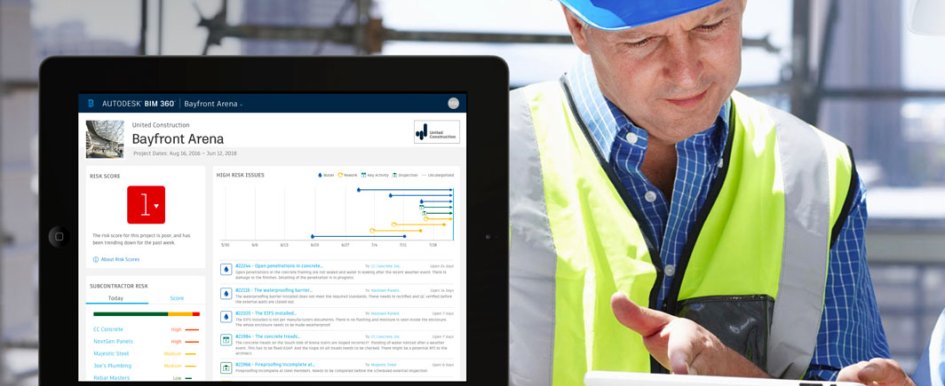
Imagine a jobsite tool that only improves with time. Imagine a tool that records each and every change order, every bit of rework and every safety incident. Not only does that tool record it, but it also files it away for future projects. Imagine a tool that learns from the past to improve your company’s future.
Through artificial intelligence and machine learning, several software providers in the construction industry are building technology to do all of the above. Pat Keaney, director of product management for Autodesk’s BIM 360 suite, has been working on such a solution for several years.
Keaney is part of a team called Project IQ. The team is comprised of approximately 20 artificial intelligence (AI) experts, data scientists, product engineers, user experience (UX) designers and several more roles, all of whom are focused on taking the mountains of data that circulate a construction site on a daily basis and making that data actionable for the project leader or business owner. The team has been collecting data from a number of different companies involved in Project IQ’s pilot program. The team has used insights from that data to test and improve several different software solutions. The basis of this solution evolves around machine learning.
For the team at Autodesk, it was immediately evident that for Project IQ to succeed, the general contractors would have to be closely involved with the process from start to finish, because it is their companies’ data from which the the team would be learning. And because the team wanted to make sure that whatever it developed would need to be as accurate and helpful to the industry as possible.
Project IQ works with 20 of the largest general contractors in the world, primarily in the United States, but the list includes one in the United Kingdom and one in New Zealand.
The first rollout worked to more accurately capture problems as they occur on the jobsite, as well as track and close out those problems in a more efficient manner.
“You can literally have thousands of open issues on a project at any given time,” Keaney said. “For example, one project manager told me that he could literally spend all of his time staring at issues and trying to find solutions for them.”
One company involved in the initial rollout for Project IQ was Utah-based general contractor Layton Construction. In the last decade, Layton Construction has grown from being a regional contractor to a company that plays on a national level. Rich Holbrook, director of construction operations, is responsible for managing the company’s many business units and project segments. More recently, he has also been tasked with improving the company’s quality program, which is how Layton connected with the team at Autodesk.
“Our executives had enough foresight to see that Autodesk solutions fit well with Layton’s processes. We are a process-driven company that focuses on quality, unity, truth and completeness. Tech is the best tool we have in our arsenal to further those goals,” Holbrook said. “Instead of digging through archives and attempting to analyze all of that data, Project IQ software does it for us.”
The drawback, though, is getting the entire team on board to input good, consistent data. Older solutions were not conducive to easy data compilation, so Layton and the Project IQ team worked together to figure out a software solution that was accessible to the contractor, at any time, in any place.
After the data for each issue is gathered by the team in the field, the IQ team can then cull through all of it. The tech categorizes each issue as either a high or low risk. The team can also auto-categorize issues into types that are inherently more risky. For example, any element of a project that involves water integration would fall into the riskier category, simply because it is a more complex build. This auto-categorization allows a project manager or superintendent on the jobsite to come in each morning, check his/her phone and immediately see a breakdown of the high-risk and low-risk issues on each jobsite. This helps the entire team immensely simply because it prioritizes the issues that need to be resolved first.
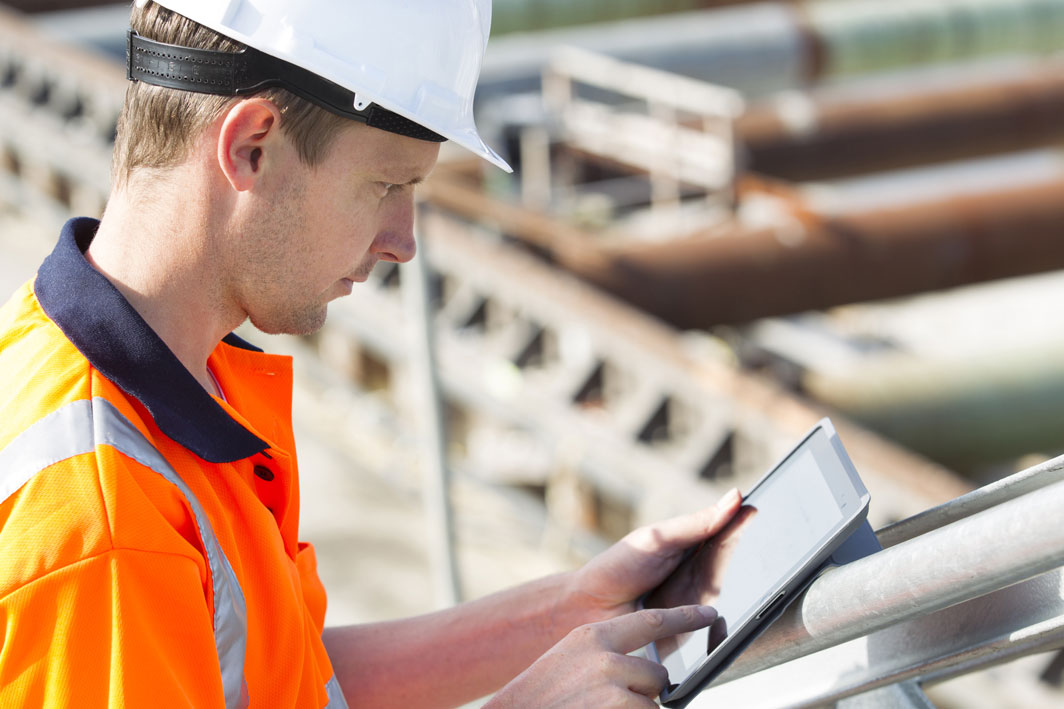
Most of the time, five to seven of the issues need a project manager’s immediate attention, Keaney said, but the software helps separate the immediate risks from the ones that are not quite so dangerous. With project risks neatly in check, the Project IQ team has turned its sights on alleviating another recurring jobsite challenge: safety.
“The idea was, if the software could learn to separate high risks from low risks on the jobsite, it could also record and sift through safety incidents,” Keaney said. For example, fall risks are common on every jobsite. A superintendent or safety director should already be paying attention to any kind of behaviors that result in a fall risk. Keeping detailed safety records is already commonplace on jobsites across the U.S.
However, these project records often go into a database and are never viewed again, barring litigation or an OSHA citation. With machine learning, safety directors can effectively sift through the data, and get a quick, all-encompassing look at which project partners, such as project owners and subcontractors, are more prone to creating situations in which fall risks arise. The software looks for patterns of behavior on a project—from project patterns to subcontractor behaviors. There are 35 main safety hazards the software looks for in every recorded safety incident.
“What’s been really interesting is to see the different patterns we see on different jobsites,” Keaney said. “The safety managers we work with are excited about that because it means they can customize the discussions they are having surrounding safety on the jobsite.”
For the team at Layton, a machine-learning solution focused on safety had immediate results.
“One way we were immediately able to improve processes was by automating and standardizing certain safety checklists on all of our projects,” Holbrook said. “The software gathers all the data we were already filing, and lets us know what risks we repeatedly had on our projects and what could potentially lead to injury.”
The Layton team started by focusing on the fatal four risks (electrical hazards, fall hazards, struck-by hazards and caught-in or -between hazards), and then expanded outward. Layton worked with the Autodesk team to develop common keywords with which the machine learning software could search and identify. When Layton employees report from the field, they can add tags and information to photos and records to help create a more detailed report.
For example, if a picture of a worker standing on the top two steps of a ladder is recorded, the project manager may assign the photo to a specific project partner or subcontractor. When the team is discussing the record later, they can look at all of the recorded incidents associated with that company.
According to Keaney, the data has shown that there is a direct correlation between the subcontractors that exhibit a lack of attention to detail or quality and the level of safety under which they operate on the jobsite. “Many of our general contractors knew this prior to implementing the software, but now they have the data to back up those assumptions,” Keaney said.
This is perhaps the most useful asset of machine learning for the construction industry—clear, concise data that takes the bias out of workplace decisions. Contractors are able to make decisions based on consistent analysis.
While there is a large degree of interest surrounding data and insight in the industry currently, it is difficult for most contractors to attempt to implement machine learning on their own. For the team at Autodesk, this is where a solutions provider can truly provide value.
“Our main focus is to create machine-learning technology that is truly valuable and accurate for the contractors,” Keaney said.
That has meant a high level of interaction with leadership teams in each of the 20 companies the Autodesk team has worked with for Project IQ.
“We placed high value on connecting the older, experienced superintendent and the younger, tech-savvy project engineer through this software,” Keaney said. “We see both of these people, and more, interacting with the solutions we are providing. We also wanted to keep it simple.”
Like any new technology, Holbrook said Layton’s younger employees more readily adopted the software. “We got more pushback from the older craftsmen, but I think it just takes every individual seeing that it is critical they play a role in collecting data. When they recognize that those tools are there to help them, the team really begins working as a cohesive unit,” Holbrook said.
The executives that the Project IQ team works with are extremely interested in how the data collected can apply across a companywide level—what can be learned from one project or another and be used on future projects with similar teams.
“We are more interested in getting it right, and solving prevalent jobsite problems. We didn’t want to create yet another dashboard. We wanted to create actionable insight. We wanted to create a new way of looking at data that would help a business owner, safety director or superintendent get the job done,” Keaney said.
For Keaney, she sees this progress as only the beginning. “AI is the next giant, disruptive technology force. It would not be possible with all of these preceding trends. It wouldn’t be possible if computing wasn’t ubiquitous and centralized. It wouldn’t be possible without the volumes of data we have been collecting for some time now. But AI is going to change every aspect of our lives,” Keaney said. “What’s exciting is that it’s going to work its way into all tech. Done well, it will be almost invisible. It will make technology smarter and more assistive.”
According to Keaney, AI enables a reverse-engineering of knowledge. Take a seasoned superintendent. He/she doesn’t forget all of his/her experiences. But how do you harness that knowledge? If software can take his/her notes and reports and pull actionable data from them, that’s a way of capturing that knowledge.
“We designated representatives within each business unit that be the go-to owner of each unit when other employees need help with the machine learning software,” Holbrook said. “We also created a leadership safety committee, which was responsible for creating a strategy around working with the data and learning from it.”
According to Holbrook, the team also extends an invitation to all of Layton’s subcontractors, owners and architecture firms to work with the software as well. For teams like the one at Layton Construction, adapting to a jobsite where machine learning touches every aspect of the project will take time. However, the benefits that AI can provide are already evident.
“As a team, we are learning to keep our eyes wide open,” Holbrook said. “There is a direct correlation between the projects that adopt these tools and follow processes to the profit margins that are well-executed.”
For Layton Construction, anyway, the software is there to help, not deter. The trick is just in getting the team on board.
“Data is both the biggest opportunity and the biggest obstacle,” Keaney said.
Whatever your strategy, you no longer have time to wait. Make a plan for your company to harness the power of data now.
Building a Data-Driven Company
Every GC should prepare to make the shift to become a data-centric business. Machine learning, like anything else, can easily be done poorly. Keep in mind the points listed below.
- Establish a consistent, organized plan for collecting data right now. Do not delay.
- Incentivize your employees to collect data. This is the key to successful implementation of machine learning software.
- Considering the power of data is important—and understanding the importance of cloud-based systems to store all of that data is paramount.
- Approach a DIY strategy with caution.
- Pay attention to larger trends across the industry.
- Choose your vendors carefully.