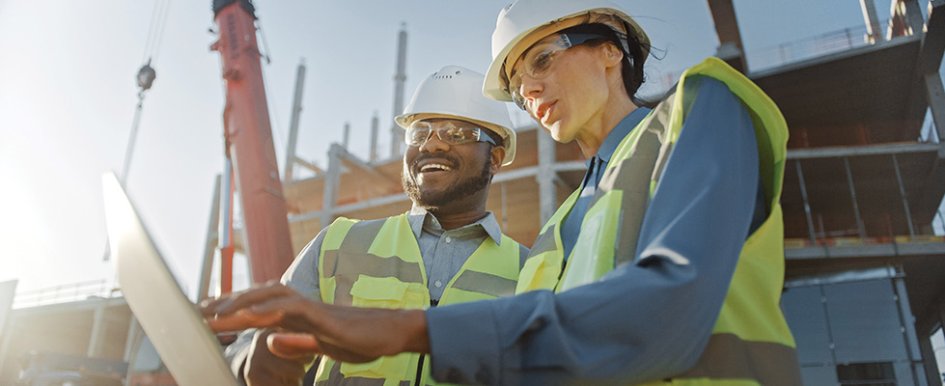
Quality assurance (QA) in construction isn’t just ticking boxes: It’s about building safe, durable structures that stand the test of time. For construction business owners, mastering QA can mean the difference between costly reworks and a sterling reputation.
At its core, QA ensures that projects meet or exceed quality standards. It’s a systematic approach that covers every aspect of construction from the initial design to the final inspection. But to truly understand QA, we need to distinguish it from its close cousin, quality control (QC).
While QA is proactive, setting standards and procedures to prevent defects before and during construction, QC is reactive and involves inspections of completed work to ensure it meets the required standards. Both are crucial components of a strong quality management system, and advanced platforms are increasingly bridging the gap between these proactive and reactive processes.
The benefits of a robust QA program are manifold. By implementing comprehensive quality processes from the outset, establishing clear standards and ensuring proper documentation and information access, potential issues are prevented or identified early, leading to safer, more reliable structures. This proactive approach includes efficient management of requests for information (RFIs), submittals, project communications and issue tracking.
Having a centralized system for these critical processes ensures that all stakeholders have access to up-to-date information, facilitating quick resolution of potential quality issues. This comprehensive approach to information management translates directly to cost savings.
Beyond the financial impact, QA ensures regulatory compliance, helping projects meet all necessary building codes and regulations, thus avoiding legal headaches and fines. By integrating all aspects of project information from initial designs to final inspections, construction teams can maintain a proactive stance on quality, catching and addressing issues before they escalate into costly problems.
And truth be told, delivering projects that meet or exceed client expectations builds a reputation that can lead to more referrals and repeat business. In an industry where word-of-mouth recommendations carry significant weight, the long-term benefits of a strong QA program can’t be overstated.
So, what does a robust QA program look like in practice? It starts with setting clear, measurable quality objectives for each project phase, aligned with client expectations, industry standards and regulatory requirements. These objectives serve as a road map, guiding every decision and action throughout the construction process.
Comprehensive quality plans are developed, covering everything from structural integrity to material quality. These plans aren’t static documents but living guides that evolve with the project, adapting to new challenges and insights as they arise.
Effective documentation processes are crucial, keeping detailed records of all quality-related activities. In the digital age, this goes beyond mere paper trails. Modern QA systems leverage cloud-based platforms to create searchable, accessible archives of every quality check, test result and corrective action taken.
Clear communication protocols ensure that all team members, including subcontractors, can quickly and efficiently address any issues that arise. In an industry where time is money, the ability to swiftly identify and resolve problems can make the difference between a project that’s on time and on budget, and one that spirals into delays and cost overruns.
But even the best-laid plans are only as good as the people executing them. The human element in QA cannot be overstated. Ongoing training keeps teams up to date on the latest QA practices and standards, closing skill gaps and maintaining high-quality work. This isn’t just about technical skills; it’s about fostering a mindset where quality is everyone’s responsibility, from the project manager to the newest apprentice.
Fostering a quality-focused culture attracts top talent, improves employee satisfaction and enhances a company’s reputation for excellence. It’s about creating an environment in which taking pride in one’s work is the norm, not the exception. This cultural shift can have far-reaching effects, improving not just the quality of construction but also workplace safety, employee retention and overall project efficiency.
In recent years, technology has become a game-changer in the QA landscape. Advanced project and information management tools are revolutionizing how QA is implemented. Software that builds complete project records using mobile apps and cloud-based platforms, allow for real-time data collection, collaboration, communication and reporting. These information management platforms should be powerful search engines that are not just made for storing information, but actually finding the information. This streamlines the quality management process and ensures quick issue resolution.
The right project and information platform is an integral part of your QA, providing a comprehensive view of project progress and quality metrics. Having one tool for all your project management, information management and even building information modeling (BIM) coordination allows for more informed decision-making, as quality data can be viewed in the context of overall project timelines.
Marge Hart, senior vice president of product at Newforma, emphasizes the importance of information management in QA: “Effective quality assurance happens because of robust information and communication management. The right platform doesn’t just store data — it facilitates seamless communication and makes quality-related information easily accessible and actionable. By integrating QA processes with efficient project information management and communication, we transform quality management from a reactive measure to a proactive strategy that drives continuous improvement throughout the project life cycle.”
Indeed, effective quality assurance relies heavily on robust information management. A centralized information repository ensures everyone has access to the most up-to-date plans, specifications and quality standards. Real-time updates prevent work based on outdated information, a common source of errors and rework in construction projects.
Historical data analysis allows for the identification of trends and recurring issues, improving future QA processes. By learning from past projects, construction firms can anticipate potential quality issues before they occur, leading to more efficient planning and execution.
Improved communication, facilitated by a robust information management system, is crucial for addressing quality issues promptly. In an industry where multiple stakeholders often work in silos, the ability to share information quickly and accurately can be a significant competitive advantage.
It’s important to remember that QA is not a one-time task but an ongoing process. Capturing lessons learned and continuously
refining QA practices prevents recurring issues and drives innovation. Quality management software plays a crucial role in this process by providing the data and insights needed for continuous improvement.
The construction industry continues to evolve, and those who prioritize quality assurance and leverage technology to support their efforts will be best positioned to thrive in an increasingly competitive market. The future of QA in construction lies in combining robust processes with cutting-edge technology. Success will come to those who not only create comprehensive quality plans but also harness the power of the information they generate.
In the end, effective quality assurance is key to project success, client satisfaction and structural integrity. It’s an investment that pays dividends in the form of reduced costs, enhanced reputation and buildings that stand the test of time. According ISO Update, American Society for Quality (ASQ) studies indicate that for every dollar you spend on quality management, “you could expect to see an additional $6 in revenue, a reduction of $16 in costs and a $3 increase in profits.”
Looking forward, one thing is clear: Quality assurance will continue to be at the heart of excellence in the built environment.