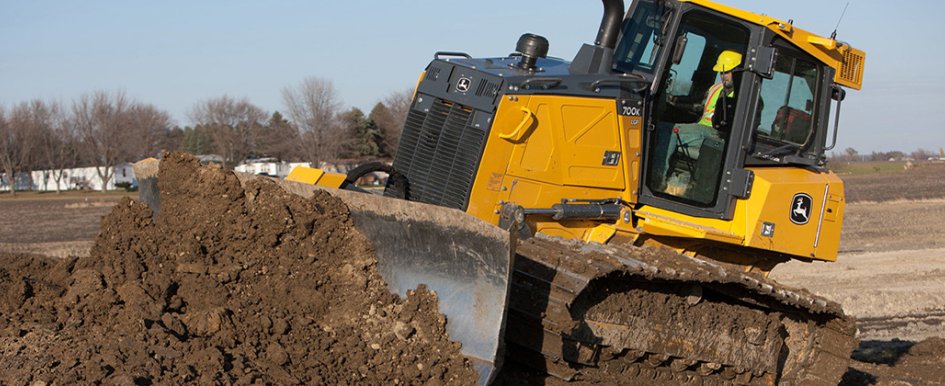
Grading a worksite is a critical element in preparing land for development. While it can be an expensive process, grading plays a critical role in laying out a mapped overview of jobsite development.
Today, machine technology has emerged to simplify the grading process and eliminate inefficiencies. Grade control is quickly being adopted on jobsites throughout the country, and the cost benefits of investing in grade control technology can enhance a contractor’s bottom line. Pairing a grade control system with a crawler dozer or motor grader is a great way to see a huge return on investment. A grade control system gives contractors the accuracy needed to bid more competitively and, in turn, win more jobs.
With grade control, the impact on an operation’s return on investment is almost immediate. For example, a developer plans to build a shopping center with a huge parking lot, a commons and a pond on a stretch of land. First, the developer will hire an engineer to build a 2-D representation of a 3-D land surface, or a topo. From this map, a design of the shopping center is then created.
Once the design is in place, contractors are brought in to prepare an estimate. Using a grade management system, contractors can topo the site themselves to verify the engineer’s quantities on the initial, 3-D contoured map of the existing site. This process is known as takeoff, which is comparing the plan quantity versus takeoff quantity using construction software. After completing his/her own accurate estimate, the contractor can create a competitive bid and win the contract.
Next, the contractor creates a 3-D model from the digital design, and then he/she will localize it and integrate the model into the on-site data collector and grade control machine. With the system ready to go, the contractor’s accuracy is improved, reducing the number of passes for successful job completion. Grade control drastically eliminates the need for grade stakes and additional workers on the jobsite, even during the verification process.
Grade Control Systems
There are many grade control systems available in the market today:
- Entry-level 2-D systems—The 2-D grade control system allows operators to set up a laser transmitter to cut to their desired grade, on both flat and sloping surfaces. The 2-D system uses angle sensors and rotational sensors to calculate the cross slope of either side of the blade, as well as a laser receiver to provide elevation control. Using a motor grader or crawler dozer, the system allows stringline, previous pass or curb and gutter tracing. With the laser receivers, operators can use the system for fine grading plane surfaces. The 2-D grade control system is ideal for applications with tight tolerances and finished grade work. Often, these systems come with a control box that includes software with a powerful range of features specifically designed for lift and/or tilt control on dozers and motor graders.
- 3-D systems—With a 3-D grade control system, the job’s design elevations are input into the crawler dozer’s or motor grader’s control box. A receiver on the machine reads the GPS signals received by an elevated antenna, as well as correctional data transmitted by a jobsite-based station to calculate an accurate, cutting-edge position. The control box’s computer compares the cutting-edge position to the design elevations and then displays cut-and-fill information. A 3-D system is best for complex contours. Automatic systems for both 2-D and 3-D even adjust the blade for the operator. Both methods allow you to achieve a precise height and angle, while using an exact amount of materials and manpower to complete the job.
- Robotic total stations—Robotic total stations are convenient when access to the sky is limited, such as on a project involving work inside a building or tunnel. They are 3-D positioning sensors for a 3-D grade control system. The sensor is an electro-mechanic and optical positioning device. It works anywhere a view of the sky is obstructed. Also, it is one of the most accurate positioning sensors available for 3-D grade control applications.
- Millimeter GPS system—An MMGPS combines the advantages of a laser with a GPS into one versatile, easy-to-use system. This technology can improve grading accuracy up to 300 percent over most 3-D machine systems. The MMGPS transmitter sends out a wall of light 33 feet tall and up to 1,000 feet in diameter, and with a machine control sensor added to the existing GPS system, the vertical accuracy is enhanced considerably.
Grade Control WorkFlow
Now, you have picked a grade control system that best suits the needs of your jobsite. Once you are ready to begin a project, it is critical to properly implement grade control to ensure your investment is worth the while. Since contractors are reducing their operating expenses with this technology, grade control impacts them significantly throughout the entire work cycle. To see efficient return on investment, it’s important for contractors to execute flawless grade control workflow, a step-by-step process to help them complete jobs and maximize ROI while using grade control technology. Walk through a day in the life of a contractor utilizing grade control:
- Setup/Topo—An engineer establishes four control points for a particular jobsite through specific measurements. The engineer will measure control points with a rover to establish the complete jobsite. Then, the engineer will create a topo of the jobsite. Wherever site development will occur, the engineer covers the entire jobsite to ensure all measurements are recorded. The topo will map out all of the elevation changes across the site, and the engineer will create the site design after all measurements are ensured and completed.
- Design—The jobsite design establishes the location of all the structures that will be built, including underground utilities, parking lots and everything else the landowner wants to build on the site.
- Takeoff/Estimate—In the takeoff/estimate portion of grade control workflow, contractors compiling bids will compare what the design engineer has provided for quantities on the site. Contractors will then verify utilities. Contractors will also confirm the material that will be required to move using the grade management system. They will then compare the surfaces to make sure all of the engineer’s information is accurate and construction can begin based on the engineer’s measurements. F0+90 (feet and tenths of a foot) are measured on the map to paint the picture for the contractors, letting them know the distance of cut and fill. This helps contractors plan the equipment that will most efficiently move the material, allowing them to have the lowest cost per yard.
- Winning the bid—Without grade control, the project will be more expensive and more challenging to provide a low-cost estimate. In some cases, grade control allows the construction team to use one crawler dozer instead of two. Also, the winning contractor does not need to hire a third-party surveyor throughout the duration of the project, as the technology will have the team covered.
- Model—Once the bid is won and construction is ready to begin, a 3-D model using software will allow contractors to build cut, fill maps and format the project to run on specific grade control software. The 3-D model is then used for grading.
- Localize from the project—At this stage in the work flow, the contractor will measure the control points to orient himself to the site. Then, he/she will take measurements of local coordinates Northing-Easting-Elevation, tying them down to latitude, longitude and ellipsoid height.
- Import 3-D model to the crawler dozer—Using a simple USB, the contractor can upload the surface coordinates to the machine. With assistance from your dealer, a grade control specialist can support the contractor throughout the process.
- Support—A local dealer is with the contractor every step of the way to ensure grade control efficiency and results are achieved to increase the contractor’s bottom line. Dealers have the parts on their shelves to ensure uptime, and dedicated specialists to help keep operations running smoothly.
Grade Control vs. None
In order to paint a better picture of the benefits of grade control usage, consider a project on a jobsite with 100,000 cubic yards of material to move and 50,000 square yards of parking lot.
- Mobilization—Mobilizing a jobsite for development without grade control requires two articulated dump trucks, one excavator, two dozers and one tractor. With a $120 hourly rate, site mobilization will cost an estimated $2,160. With grade control, contractors still need two ADTs, one excavator and one tractor, but they will only need one grade-control-enabled dozer, which will cost roughly $1,800 for site mobilization—a savings of $360.
- Site clearing—When clearing a site for construction without grade control, laborer stakeout limits are required to ensure control points are met throughout the site clearing process. With a grade control system, control points are easily verified through the technology’s incorporation of the topo, saving contractors approximately $1,440 in labor costs.
- Stripping of topsoil—When stripping topsoil without grade control, a laborer is required to verify measurements, costing contractors roughly $2,400. A grade control system ensures soil is stripped at exact measurements based on the topo integrated into the system, allowing contractors to save on labor costs.
- Cut/fill—Without grade control, a cut-and-fill assignment requires two ADTs, one excavator, two dozers, one tractor, one laborer and six operators—costing contractors an estimated $294,000. Grade control only requires one dozer, no laborer and only five operators, creating an estimated cut and fill cost of $236,000—a savings of $58,000.
- Placing aggregate/stone—To place aggregate and stone, two operators will spend around 320 hours applying materials to the jobsite without grade control. One tractor, one dozer and one laborer will spend 160 hours completing the aggregate placement portion of a project. A grade control system allows two operators to spend 224 hours on the project, and only a dozer and tractor are required for 112 hours. With no laborer required, grade control saves approximately 288 project hours for a total savings of $30,720.
- Topsoil respread—With grade control, fewer operators and no laborer are required to complete the respread of topsoil. A grade-control-enabled dozer will spend half of the time respreading topsoil of a dozer lacking grade control, allowing for an approximate savings of $11,600.
In total, grade control can save contractors roughly $118,520 on projects. With savings on labor and equipment costs, it is time to think about a grade-control-enabled dozer for your fleet.
Based on this project example, contractors that go without grade control might not even have a chance at landing a contract. Return on investment is evident throughout the entire process. An average 3-D machine control system costs between $60,000 and $70,000, and a base station, rover and data collector costs roughly $30,000. One project using grade control can pay for itself.
Grade control is growing rapidly with the introduction of integrated systems. While the initial sticker price may scare people, following the grade control process can save contractors thousands of dollars toward their bottom line.