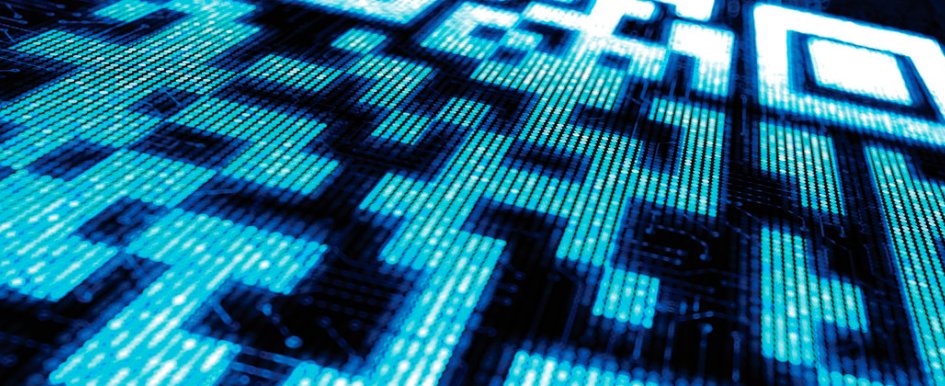
Today’s workforces are both technology savvy and technology dependent. Instead of racking their brains for arcane information, they have all the knowledge they need on the touchscreen of a smartphone. These “moment of need” pioneers have forced employers to approach employee training and awareness differently. For the construction industry, technology is becoming a major player in deciding how health and safety is promoted, executed and managed. Organizations that have embraced this change are quickly realizing that the benefits far exceed the initial investment.
Construction workforces have an ever-growing number of millennials who are accustomed to using technology and the ability to access the information they need when and where they need it. If organizations leave a void and do not systematically address this need, the worker will still find some way to get the information he/she needs. Then the question is whether that information is correct. Ensuring that a worker accesses quality, controlled information should be a top priority. If you provide this information, they will access it, even the generations that do not fall in the millennial cohort.
Technology in health and safety is nothing new. Years ago, the introduction of software and e-learning took the health and safety world by storm. The use of mobile devices has only increased those capabilities for field-level engagement.
QR Codes in Health & Safety
Quick response (QR) codes are one good way to provide workers with vital information and training when they need it. QR codes are matrix barcodes, or 2-D barcodes, that were invented in 1984 by Denso Wave Corporation (a subsidiary of Toyota) to keep track of vehicle parts during manufacturing. Because of its quick readability and greater storage capacity (as compared to UPC barcodes), QR code use quickly became attractive for other organizations outside the automotive industry that wanted to distribute information, tracking, managing documents and marketing. QR codes can be generated easily via free online tools and redirected to any uniform resource locator (URL) an employer chooses. All an employee needs to do is download the QR app on a smartphone and snap a picture.
A QR code can be used for almost anything to increase employee safety awareness and provide information. Companies can provide supplemental learning or reference material, such as job aids, regulations and SOPs. Below are some ways to incorporate QR codes.
- Posters/signs on the jobsite—To build a foundation for an effective health and safety culture, heightened employee awareness is key. Organizations are now including QR codes on posters and signs on jobsites to promote health and safety. Posters can distribute “soft” safety and health information, such as safety tips or employee health. By doing this, employees are empowered to engage in the “pulling” process for information, rather than waiting on a particular subject matter or message be assigned to them.
- Equipment/machinery—Attach QR codes on equipment, tools or machinery to show quick video demonstrations on safe operation and use. Depending on the type of project or the particular job function of an employee, it is reasonable to assume that they might have not used a tool or piece of equipment in quite some time. Providing them with the ability to access vital information and instruction could mean the difference in property damage-related losses, injuries or death. If tied into a learning management system, QR codes can provide a record that the worker accessed before engaging that particular piece of equipment.
- Checklists/inspections—QR codes can also be used to push information from the field to a central location. When tied to a URL that contains a checklist or inspection tool developed by the organization or a third party, jobsite inspections can be completed electronically and establish a record of completion. The same arrangement can be used to house other types of inspections as well. By understanding how QR codes are tied to a specific URL, the possibilities are endless regarding the collection of data from the field.
Statistics confirm that construction workforce is getting younger. According to the United States Bureau of Labor and Statistics, the construction employment rose 6 percent from 2013 to 2014, adding 542,000 workers to its ranks. Of that, the largest increase of employees occurred in the 20 to 24 year old category (8 percent). This trend is expected to grow in years to come. The median age of the construction worker remained the same at 42. In 2013, the largest age group was 45 to 54. In 2014, it was replaced by the 35 to 44 age group. These younger workers are more technology dependent. Keep workers engaged in health and safety by adapting to the new generation of technology-savvy and dependent employees. A QR code could be a good start.