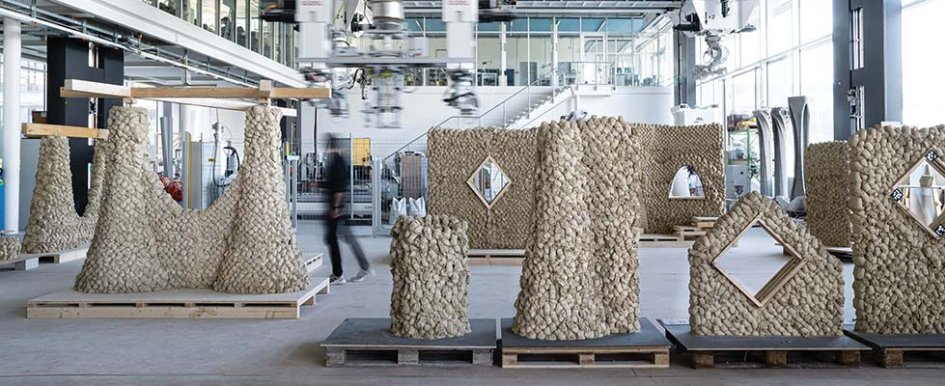
The building sector is facing major challenges. We need to dramatically decrease the embodied carbon dioxide (CO2) emissions for new construction. At the same time, we need to embrace digital planning and automation technologies. And globally, we are facing labor shortages.
Three-dimensional printing, or 3D printing, is often proposed as one solution to address many of these challenges, and it’s often marketed as a sustainable solution, since material can be used more efficiently. However, there are several issues with the way that 3D printing is done now. Concrete is the most used material, while extrusion-based 3D printing with gantry systems is the most common method and platform for full-scale construction.
However, 3D-printed material comes with relatively high CO2 emissions per volume, due to smaller aggregates and extra additives, canceling the potential benefits from efficient material use. Usually, when delivering material to the end effector utilizing a pump, the material must quickly transition between a liquid to a semisolid state. This is called “green strength development.”
Enabling resistance to plastic as well as structural buckling failures relies on accelerating the properties of the material rapidly through additives and chemical processes. Additives can also affect the recyclability of the resulting structures. Extrusion-based 3D printing cannot easily be adapted to other materials that might be more environmentally friendly.
A New Type of Robotic Printing Developed Specifically for Excavated Materials
Impact printing is being developed as an interdisciplinary collaboration at ETH-Zurich, between Gramazio Kohler Research, the chair of Sustainable Construction and the Robotic Systems Lab. The project vision is to develop an efficient and highly automated additive manufacturing method for excavated materials, to be realized on the full building scale, to produce unreinforced one- to two-story structures.
Using earth-based materials is one important strategy to decarbonize the building industry. Excavated materials are ubiquitous, local and cheap, and this material is a significant byproduct of new construction. Traditionally, earth has been used as a building material for centuries; however, there are many barriers to industrializing it. Existing methods are usually done with molds and formwork and rely on many manual steps, which can make them very expensive.
Impact printing is a robotic additive manufacturing construction method developed at ETH Zurich based on the controlled high-velocity deposition of extruded dense material parts. A three-subsystem mechanism, arranged in a vertical fashion, enables the extruding, portioning and shooting of dense premixed material (2,300 kilograms/cubic meters) with high velocity. The custom printing mechanism can deposit dense material at velocities up to 8-12 meters/second with 1-3 millimeters positional accuracy. By depositing the material in with such high velocity, a bond is enabled between parts, even when the material is already very viscous and dense. The prototypes can be cut and there are no visible joints.
Compared to normal types of 3D printing, this robotic additive manufacturing process thus has many advantages. The material is deposited in a relatively higher state of yield stress, so it is already in a state to withstand the structural load of significant vertical buildup. Thus, the process relies less on additives to accelerate the green strength, and therefore can have a lower ecological footprint.
The long-term goal would be to eliminate all stabilizers and additives so that the material could be fully recycled without downgrading at the end of the life cycle. However, this needs to be carefully studied and developed in terms of trade-offs, because more viscous material with higher-yield stress also requires more power from the mechanical extrusion system.
The current mix design was developed by the Chair of Sustainable Construction, and the main component is an excavated material that is supplied by an industry partner, Eberhard. This mix design has about 2 megapascals (mPa) of compressive strength, but the process may be extended to more materials in the future. This new printing process may have higher robustness and lower sensitivity to material variability. For example, if the current batch mixed material has lower or higher-yield stress, the process parameters (such as deposition velocity) can be adapted.
The custom printing mechanism has been integrated initially on a high-payload gantry system. The state-of-the-art robotic facility used by the research group Gramazio Kohler Research enables the development of custom robotic building methods. This experimental setup enables coordinated and controlled movement of the tool according to digitally sent instructions from design software. This setup has been used to build custom structures up to 2 meters high. For now, the design explorations are concentrating on forms that are in pure compression. Currently in development are also secondary robotic surface finishing methods that apply a secondary plaster to the surfaces, which are otherwise very rough in texture. This robotic surface finishing method can have several benefits because a stronger or more durable material can be applied in a small quantity to increase the durability of the structures. Ideally, such a surface coating could also be stripped at the end of life to still enable a circular supply chain.
The tool can be mounted on an autonomous excavator, “HEAP,” developed by the Robotic Systems Lab. HEAP (hydraulic excavator for an autonomous purpose) is a customized Menzi Muck M545 developed for autonomous use cases as well as advanced teleoperation. The machine has force-controllable hydraulic cylinders, enabling it to adapt to any terrain. This robotic-legged platform can navigate in unstructured terrain to enable continuous printing within mountainous terrain in the future. The control algorithms for the excavator currently enable it to move the 900-kg printing tool along trajectories with 1 to 3 centimeters of positional tolerances. The patented tool was developed in such a way as to enable decoupled synchronization between the extrusion system and the velocity of the tool along the path. The tool extrudes, holds and dispatches the part precisely at the right time. This construction method utilizing the autonomous excavator has so far been used to make a 3-meter-tall demonstrator in a semi-structured exterior environment.
Future Steps & Commercialization
There are many areas of future development. First, it is necessary to increase the level of automation and to develop a custom material delivery system based on conveying the material. It is also necessary to optimize the extrusion rate through engineering upgrades to the current system.
A new startup is planned to commercialize the robotic printing technology. The startup aims to first enter the prefabrication market and to develop resolved and cost-competitive building systems, such as walls that combine excavated materials with timber details. In further steps, the startup may expand to also sell or lease robotic printing equipment. The mission of the startup is to use robotics and automation technologies to enable a greener and more sustainable built environment.
Resources: Impact printing is an interdisciplinary collaboration developed by Gramazio Kohler Research, the Robotic Systems Lab, and the Chair of Sustainable Construction, at ETH Zurich with additional partners. The process is currently being commercialized through the establishment of an ETH spin-off.
Dr. Lauren Vasey, Kunaljit Chadha, Ananya Kango, Victor Leung, Fabio Gramazio, Mathias Kohler, Gramazio Kohler Research, ETH-Zurich
Dr. Coralie Brumaud, Julie Assunção, Prof Dr. Guillaume Habert, Chair Of Sustainable Construction, ETH-Zurich
Grzegorz Malczyk, Filippo Spinelli, Prof. Dr. Marco Hutter, Robotic Systems Lab, ETH-Zurich
Partners and collaborators: Eberhard Unternehmungen, WASP, ZHAW (Michael Wüthrich), OST (Prof. Agathe Koller).
Funding provided by ETH Zurich Research Grants, Innosuisse Circular Building Industry (CBI) Innovation Booster, ETH Partnership Council for Sustainable Digital Construction, Innosuisse Additive Manufacturing Innovation Booster, SNSF/ Innosuisse Bridge, NCCR Digital Fabrication (affiliated project).