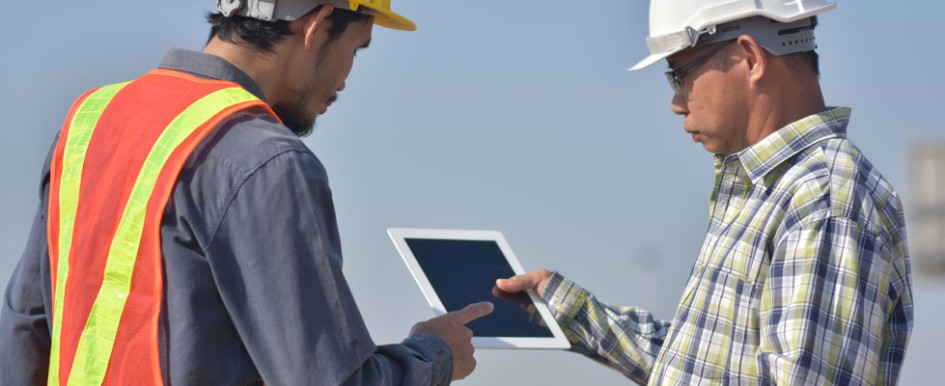
Construction has changed quite a bit over the past 5 years. Many jobsites today are turning to automated processes to overcome some of their most significant challenges—reducing safety incidents and improving productivity in the chaotic construction environment. Compounding these challenges is the growing demand for new construction and renovation, despite the shortage of skilled, experienced workers.
Growing Ecosystem of Tools
With hundreds of workers spread across a large jobsite at any one time, it is impossible for a site supervisor using manual methods to see everything that is going on, know where workers are, effectively monitor safety, or have real-time insight into project progress.
Any information that the supervisor receives can be delayed, which is particularly problematic when it comes to safety. The good news is that many new tech tools have emerged, giving contractors essential, real-time visibility. Internet of things (IoT) technologies now enable contractors to track the location of workers, equipment and tools, enabling new ways of increasing productivity, including tracking time and attendance automatically, helping workers locate equipment, and giving site supervisors critical insight into site bottlenecks and job progress.
Similarly, on the safety side, two-way communication through devices enables workers to immediately report safety hazards and site supervisors to notify everyone of an evacuation or other emergency. Thanks to real-time location services, contractors can identify any workers remaining in the building during these emergencies.
Another key safety benefit of wearable devices is the ability to detect falls and automatically notify safety personnel in real time, so they can immediately dispatch help to the worker’s location. In addition to these applications, IoT devices can be used to monitor the physical environment, including humidity, temperature, noise and vibration. Drones are providing visual data that can be used to track site progress and identify potential problems that could be avoided.
Data on all IoT devices can be collected and aggregated into a central repository—a specially designed network—giving site supervisors and management complete visibility across the jobsite.
This network enables real-time data on a specific construction project, worker, piece of equipment, and/or materials to be communicated among all of the project stakeholders. It can then be integrated across the larger tech ecosystem of tools, such as project management solutions, so managers can access and analyze it centrally against all other project data.
Data Is Key
When sensor data is collected and the devices “talk” to each other through the network, contractors can uncover key insights quickly. For example, if a wearable device approaches a sensor on heavy machinery, it could notify management that the worker is not authorized to use it. Similarly, if the worker approaches a beacon that leads to an off-limits section, such as an occupied area in a school or hospital, a supervisor will receive an automatic notification so security can be maintained.
Data can also be used to measure productivity. Contractors can use time and attendance data to determine how many workers are needed to meet project deadlines based on progress to date. And, based on the type of work to be done, they can determine the optimal use of subcontractors, reducing downtime, increasing productivity and more effectively managing cost and deadlines.
Using historical data from several projects, contractors can begin extrapolating variables to achieve productivity gains and more accurately bid on future contracts.
Meeting the Construction Network Needs
Creating this network connectivity on a jobsite is no easy feat. By their very nature, jobsites are extremely challenging tech environments, with low-power supplies and a constantly changing footprint. Despite those challenges, the network must be strong enough to enable communication through concrete, steel and other rugged materials.
In addition, the network must be adaptable and flexible enough to scale along with the project and be able to handle communication from hundreds or even thousands of connected devices on-site at any one time.
Because of the unique requirements of the jobsite, many traditional network technologies are not feasible. For example, while global positioning systems, or GPS, are useful for many consumer applications like maps and directions, they aren’t able to identify location on a vertical plane. They also do not function well in urban locations where tall buildings are in close proximity to one another.
Another option, Bluetooth low-energy technology, is not able to handle hundreds of devices, or those that are densely deployed, making it impractical for most jobsites. And ultra-wideband technology requires many power sources and is limited to about 100 devices per gateway, making it impractical on large commercial construction sites.
Because of the challenges and the limitations of other technologies, a new type of construction-specific mesh network has been developed from the ground up. This battery-powered, robust network solution is best able to address the low-power requirements, minimal hardware practicality, and need for ongoing scalability on the jobsite. Construction sites are now collecting data from all types of sensors to gain critical visibility into productivity and safety incidents.
By connecting these devices, contractors can gain new insights into their interactions and a deeper understanding of how they can manage people, equipment and projects more safely, efficiently and economically.