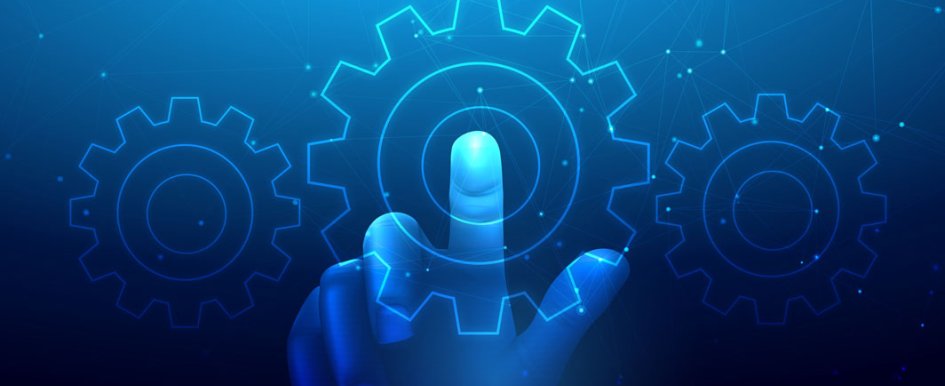
It’s an interesting time for construction. The market is strong: demand is still high; transportation funding is feeding new government contracts into the pipeline; and natural disasters are increasingly creating rebuilding needs in more cities and counties.
To an outsider, construction contracting probably seems like easy street right now. But there are two huge challenges facing the industry:
- A severe skilled labor shortage not slated to correct itself in the near term
- Materials costs that rose 9% from May 2017 to May 2018, the biggest increase in 7 years—with costs continuing to rise due to new tariffs and trade wars
This puts contractors in an unusual bind. The work is there, but it has to be done more efficiently than ever, with a more frugal use of materials and a potentially smaller, less experienced crew.
Add to that the fact that construction has historically changed at a much slower rate than other industries. Agriculture, for example, has improved efficiency by 1,500% since the 1940s. But now, for many construction companies, the choice is clear: change or die.
Why Change?
More contractors than ever are electing to enact change via automation. According to management consultant firm FMI Corporation, over $10 billion has been spent on construction technology ventures in the last decade. Investors have been banking on a technology upsurge in construction, but they didn’t know how badly the industry would need it.
With the aforementioned industry strains, operational efficiency is crucial to keeping up with the workload you have taken on as a contractor. And if you can’t keep up, you will overspend on labor and materials, disappoint your clients and, ultimately, risk the failure of your business.
Additionally, let’s say you have been blessed with a reliable and talented crew. You will still need to hire new ones sooner or later if you want to grow, or even maintain, your current project load.
I hear it from contractors everywhere—right now, it’s difficult to find skilled labor. And with baby boomers retiring out of construction and Gen Xers already settled in other careers, the new ranks will need to be filled by millennials and Gen Zers—a segment which, so far, hasn’t exactly been knocking down doors to get into construction, despite loads of new programs designed to expose high schoolers and younger kids to the trades.
The good news is, even after their elders pushed college, a small but growing cadre of young people is deciding they would rather work with their hands, solving tangible problems, than be stuck at a desk while trying to dig out of college debt. One thing is certain: with the skilled labor
shortage in full effect, there will be plenty of competition for high-caliber hires. And these would-be workers were born with cellphones in their hands, the internet at their fingertips and video games running through their dreams.
As such, they would find it incomprehensible if their potential employer took no measures to increase efficiency with the implementation of new technologies and automation.
What Not to Change
There are lots of shiny new tech advances that are bound to spark excitement (at least at first) among employees and new hires. And it’s easy to be drawn in by the next big thing, whether it’s self-driving equipment, robot bricklayers, exoskeletons or augmented reality (AR)/virtual reality (VR) headsets. The only problem with the industry’s flashier automation options is that they’re expensive, and their ideal uses haven’t been worked out yet.
Take AR headsets—one ideal use is in conjunction with building information modeling (BIM) to see an overlay of what’s being built on top of a blank—or slowly filling—space and catch errors early, before they result in giant change orders. That said, the software available for the headsets has yet to project design onto reality within a fraction of an inch, so far precluding its use as a precision tool in routing duct, for example.
But looking at your work in progress through an AR headset could help you catch a larger error, like detecting when heating, ventilation and air conditioning (HVAC) systems have been misrouted.
The upshot: while bringing an AR headset onto your jobsite will undoubtedly thrill your workers at the outset, you better have a darn good idea of how you plan to maximize your return on investment (ROI) before the device loses its initial luster and begins to collect dust on a trailer floor.
What to Change
The key in automating is to start with the low-hanging fruit (i.e., a single process that will bring reliable ROI) and then gradually move onto bigger processes that may not show direct monetary returns.
For instance, a form of automation that’s easy to implement is a software that streamlines one of your paperwork-heavy processes. This could be document management software, or software used for scheduling, budgeting, bidding or time tracking. If scheduling is available from the same vendor, you’ve got a one-stop solution for time management.
Time tracking software takes a key manual process that is time-consuming and error-prone and automates it from punch-in to paycheck, saving everyone time and shaving off the significant margin of error found in most construction company payrolls.
However you choose to automate your most labor-intensive, manual processes, if it’s a strong product with a proven track record, it should save you time and increase efficiency, while also proving to young hires that you are open to evolving with the times.
Once you’ve brought in this guaranteed ROI, you can start deciding your second and third moves toward incorporating automation and becoming a state-of-the-art business that good workers will flock to, both new and old.