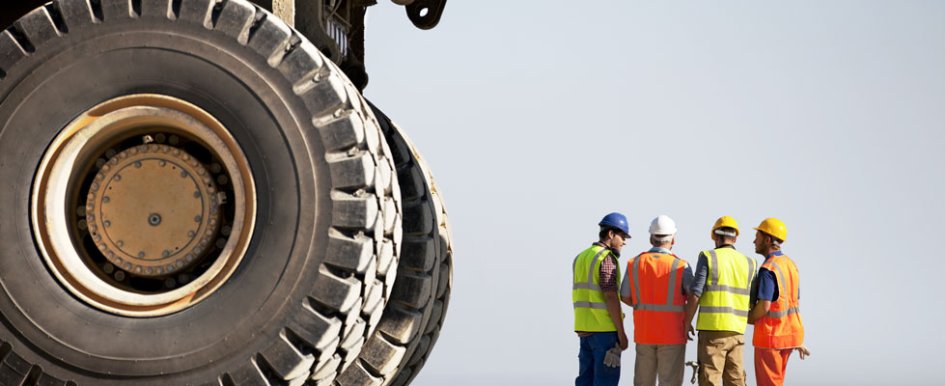
The construction industry, deemed an essential business during the coronavirus pandemic, never stopped working. Because it remained vital, 67% of workers expected consistent or increased project backlogs. As project managers (PMs) navigate a new normal and a considerable amount of work, lean workforce management processes can provide a blueprint for successful crisis management and risk mitigation.
Lean construction workforce management is a simple strategy that prioritizes efficiency in decision-making to maximize performance and competency. This includes assigning workers to projects, collecting data, budgeting and forecasting. PMs who focus on eliminating waste during scheduling have more time to prevent problems before they become a crisis.
The core factors addressed by lean workforce management are improved efficiency and processes, both of which are fundamental to risk management. Both factors decrease the time it takes to complete projects. According to a study in the Alexandria Engineering Journal, lean construction principles led to a 15.57% decrease in project times.
Construction involves myriad moving parts, which is why maintaining and assigning crews requires long-term planning that is reproducible at scale. Managers can practice lean workforce management by generating a labor plan graph that shows how many hours it will take to meet the needs of a project.
The graph will have ridges and valleys, so managers will need to tweak the graph until it is flat, indicating fewer wasted resources. With careful management of all project elements, construction leaders can unlock the following five advantages of waste elimination:
1. Smaller Workforce
Some projects do not require a company’s entire staff. For example, assigning 10 workers to a project that needs only five distances everyone from the work and decreases everyone’s job satisfaction. About 15% of construction companies say they have a workforce with 1,000 or more people.
If each project has the exact number of workers needed to complete it, managers can increase efficiency and open up company capacity. Creating a leaner team is the basic foundation of workforce waste elimination in a construction environment.
2. Increased Productivity
When managers are leading smaller workforces, they are closer to their projects and people. Low productivity is the result of poor leadership, so the more involved managers can be, the better.
When everyone is working efficiently, it reduces the chance of escalating project costs. Delayed projects can cost firms up to 20% of their original estimations, so it is in companies’ best interests to practice lean construction workforce management.
3. Less Equipment
Smaller crews need fewer tools and less equipment (which is expensive to buy, maintain and protect). Plus, using fewer pieces of equipment can reduce the level of cleaning needed to maintain a safe working environment during the pandemic.
About 60% of construction workers are at higher risk for COVID-19 due to age and co-occurring risk factors, so this mitigates the risk of infection and improves the health and safety of crews working on-site.
4. Improved Communication
Centralized team communication helps everyone know about their assignments. It reduces waste, eliminates mistakes and decreases inefficiencies by reducing the chance that information can be dropped along the way.
For example, if a PM needs to shift workers from one site to another and they rely on individual texts and calls, then they might forget to notify an important team member.
With improved communication channels, PMs can streamline internal processes and avoid uncertainty in scheduling, resulting in timely work and fewer holdups.
5. Reduced Trip Waste
PMs who practice lean construction workforce management assign workers to individual jobs based on their travel time from home. Shorter commutes mean more time on-site, and workers will appreciate the efforts to respect their time. As a bonus, it decreases the carbon emissions produced during jobsite trips.
Despite its devastation, the coronavirus pandemic has led to a renewed focus on proactive problem-solving and risk mitigation. Managers who implement lean workforce management processes can tackle their increasing number of projects with increased efficiency and accuracy. Instituting a proactive approach to crisis management today will yield real benefits for construction companies now and for years to come.