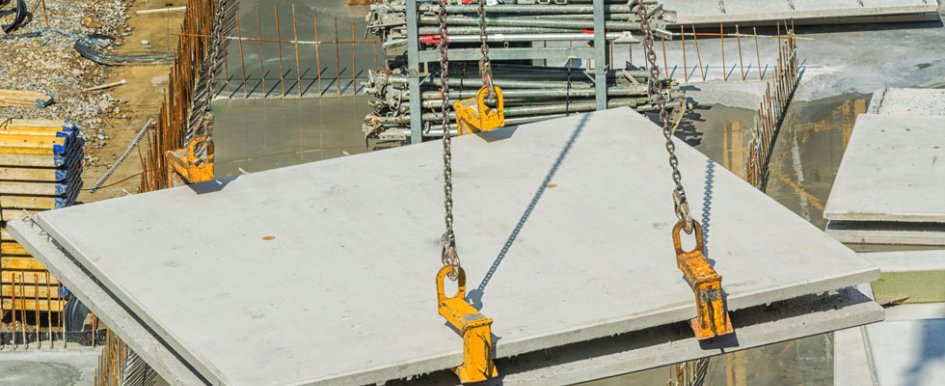
Picture dozens of modules slotted into place, creating multi-unit apartment blocks, hotels or student housing. This has been the prevailing image of prefabrication in construction: volumetric modular builds that are repetitive, cellular and simple.
Builds such as the Nightingale hospitals in the U.K., which were assembled in just days, prove the quality, predictability and speed that the prefabrication approach can deliver. There are many other stories about volumetric modular construction
like Nightingale that get the lion’s share of the focus — but they all overlook the bigger picture.
Prefabrication and industrialized construction are a significantly larger ecosystem with stakeholders that provide everything from building parts to assembled components and large-scale building systems, as well as volumetric modular elements. For example, in projects with heavy mechanical, electrical and plumbing (MEP) elements and hardened structural requirements, subcontractors engineer and build systems offsite and then deliver and install them in the
building project.
Looking to the future, five sectors will define and establish the standard for prefabrication and productization (prefabrication’s next level) and will set the stage for transformation throughout design and construction: data centers, pharmaceutical manufacturing, oil and gas, manufacturing facilities and semiconductor plants.
Serial Owners Look for Certainty
What do these sectors have in common and why are they well-suited to industrialized construction? Unlike housing, for example, all five represent highly consolidated markets with a smaller number of serial owners operating across multiple geographies. Serial owners typically require consistency across projects to provide operational efficiency, the ability to accelerate projects and to control costs. Rather than starting from scratch on every project, these owners also want uniform facilities that are constructed — then operated — in the same way every time so they can gain economies of scale only available with repetition. They want to develop and provide an owner’s playbook to their designers and builders to allow them to follow a proven process.
Uniformity is especially important for heavily regulated industries, like pharmaceutical manufacturing, where compliance depends on a consistent environment. And in less predictable, remote locations like oil refineries, uniformity helps mitigate risk.
Lastly, all five industries depend on specialized, technical facilities. Every project requires heavy MEP and hardened structural elements, especially in oil and gas. Traditional construction processes are typically not a good fit for these projects as they require building complex systems in constrained spaces with multiple trades developing highly technical systems at the same time.
With prefabrication, MEP and structural components can be decoupled from the jobsite and engineered and manufactured concurrently in a controlled setting. This approach provides owners with a greater certainty over schedule, cost and output — factors critical to every project.
Reaping the Benefits of Productization
Serial owners that build and operate data centers, pharmaceutical manufacturing, oil and gas, manufacturing facilities and semiconductor plants are even progressing beyond prefabrication to productization. Productization means owners are partnering with design for manufacturing and assembly (DFMA) experts to create a scalable product that is defined, managed and optimized for a specific need. The resulting components can be incorporated during a structure’s design phase and then procured like equipment.
Productization creates incredible value for these industries, from the first build through to an asset’s entire life cycle. For example, facilities in all five sectors incorporate technology that will evolve and be replaced over time, such as the heating and cooling elements in data centers or manufacturing robotics. Through productization, these systems have well-defined functional requirements and system integration that makes installation easier, serviceability and replacement is simplified, sustainability increased and downtime for upgrades minimized.
Then there’s scalability. Instead of building large facilities with unused space reserved for future capacity, productization allows serial owners to be more responsive to demand and to “right-size” their projects — conserving capital. They are more responsive because they can build faster, build from reliable components and systems, and get consistent results regardless of who builds the project. Through productization, owners in these critical sectors can create future-proof facilities or even allow for technology swaps without risking their capital.
Embracing the Industrialized Construction Opportunity
As owners in these five influential industries take greater control of projects, they will drive change in the built environment ecosystem. Other stakeholders are also beginning to take advantage of the benefits of industrialized construction, prefabrication and productization to better serve their customers.
If you are an MEP subcontractor, you should be working to transform into a manufacturer of products, rather than just aiming to be fabricator. Consider what you produce, what variations are required and begin to define your products. The ecosystem will need systems integrators — with a clear understanding of complex MEP and hardened structures — to bring together these pieces and parts.
Forward-thinking contractors will need to build on their existing relationships and embrace new processes. To adopt the new product-focused model, it will be important to grow a supply chain experienced in both prefabrication and productization, working closely with systems integrators. And across the ecosystem, there is a need for technology to underpin these new workflows: platforms that can support the flow of data and bring stakeholders together.
Embracing innovation and transforming a company to benefit from industrialized construction is a process, and it can be challenging. Right now, many companies have some of the foundational skills in place. However, there is a gap in the understanding of manufacturing techniques and other skills unfamiliar to the conventional stakeholders. Moving to prefabrication and then productization takes a mindset shift, including an awareness of the importance of reusable data across the life cycle. But from there, you can progress through optimization and even circularity enabling the ability to reuse both digital and physical assets — the benefits can be huge to many different types of organizations.
Transforming Design & Construction
Productization has the potential to transform design and construction. With consistent elements and assemblies, it’s easier to take advantage of technology including generative design — or apply advanced building techniques like
robotics in manufacturing facilities as well as on the site. From an operational perspective, these components can also feed into digital twins, generating functional data that can create feedback loops for operating in autonomous buildings in the future.
The ecosystem is at different stages of this journey, but the influential technology companies and owners in data centers, pharmaceutical manufacturing, oil and gas, manufacturing facilities and semiconductor plants are helping lead the way.
These five sectors are a fertile ground for advancing the innovations that will benefit other industries and the ecosystem as a whole. These leaders — along with the convergence of design, make and operate — will result in better business outcomes and a more holistically sustainable world.