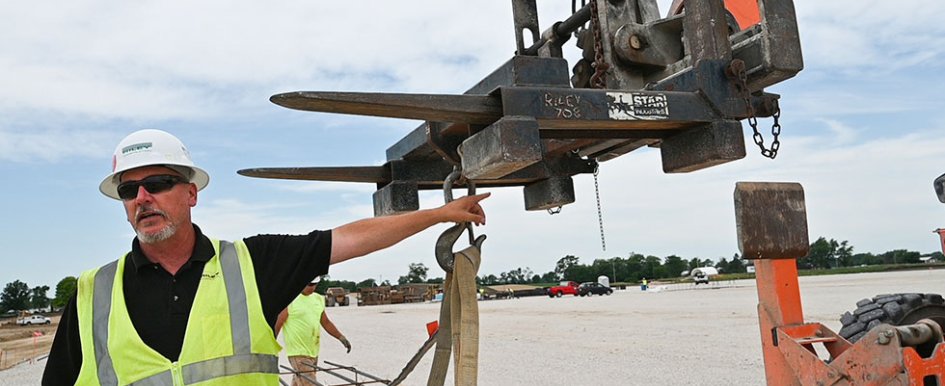
Working in construction inherently poses a higher risk of on-site accidents and other health and safety hazards off-site. On average, two construction workers die of work-related injuries every day in the United States. The Occupational Safety and Health Administration (OSHA) categorizes falls, caught in- or-between, struck-by and electrocution as the “Focus Four” construction hazards responsible for most jobsite incidents. No matter the size of the project, safety planning and employee health must be prioritized to reduce injuries that can result in work delays and potential litigation.
Consider the following four ways that planning for safety and risk management can protect your people and projects.
Early Preconstruction Plans Reduce Risk
Safety planning doesn’t begin on the jobsite — it first starts during the procurement, bidding and preconstruction process. It’s vital for construction leaders to work closely with project owners and subcontractors to identify potential risks before they become larger issues.
To manage risk from subcontractors, use a thorough, trustworthy prequalification process that involves reviewing safety records, experience modification rates (EMR), OSHA logs and other important metrics to pinpoint areas that might need attention throughout the project. This will help project managers determine subcontractors with the least potential risk.
Before any project begins, kickoff meetings should be held with project executives, project managers and field leaders as well as quality/lean, safety technology and accounting teams. These meetings provide the ideal time to identify preexisting conditions that could translate to potential safety issues as well as discussing quality/lean and insurance compliance requirements. Subcontractors should be fully insured and contracted before any work begins.
Reliable, project-specific safety plans should follow a trusted continuous improvement planning process.
Communicate for Crew Success
A prevention strategy is important for construction safety. Part of the prevention strategy is constant communication that ensures operations run smoothly from a project’s beginning to final inspection. Hosting daily huddles and weekly jobsite meetings help ensure that everything is running on time and to-plan.
During pre-install meetings, the team should address upcoming safety issues or high-risk work activities that are at least six weeks out, providing time to plan for necessary changes. These can include trenching and excavation, steel erection, crane activities, hot work and helicopter picks. Make sure all necessary materials such as respirators, fall protection equipment, etc., are on hand.
Other important safety activities to include in the communication plan are jobsite safety walks, subcontractor huddles, safety inspection reports and quarterly safety bulletins.
Build a Safety Culture
Creating a safety culture requires a lot of forethought and buy-in from top leaders to the on-site crew. A safety-first mindset needs to be integrated into the culture from day one and throughout the job — and that takes planning.
A safety culture starts with construction teams actively listening to stakeholders to learn new ways to improve safety protocols. It’s also essential to work directly with project owners to ensure safety practices are thoroughly outlined and followed. Creating longstanding relationships of trust with subcontractors also has a major impact on this process.
Create jobsite-specific safety plans during the preconstruction phase of each project. This will help identify potential hazards and safety concerns. Workers who feel like they have had a part in building or improving the safety culture from the beginning will feel more invested and are more likely to take it seriously. Everyone involved in the project should feel empowered to raise concerns and know they will be heard. Make sure safety rules are clearly outlined, and each crew member understands the consequences should someone fail to follow the rules.
Offer Training & Incentives
Every construction firm’s goal should be to ensure that employees, subcontractors and clients return home to their families safely each evening. To achieve this high standard, organizations need to prioritize training beyond a one-time event. Leaders should track industry trends and thoroughly review any losses to refine safety practices.
Safety incentives can also reward workers for following safe working practices. Reward programs should be simple, reinforce safety protocols, and allow for consistent feedback to employees.
Leaders who integrate safety into every facet of projects, communicate often and build a safety culture with continuous learning and rewards should see noticeable improvements in their overall safety practices.