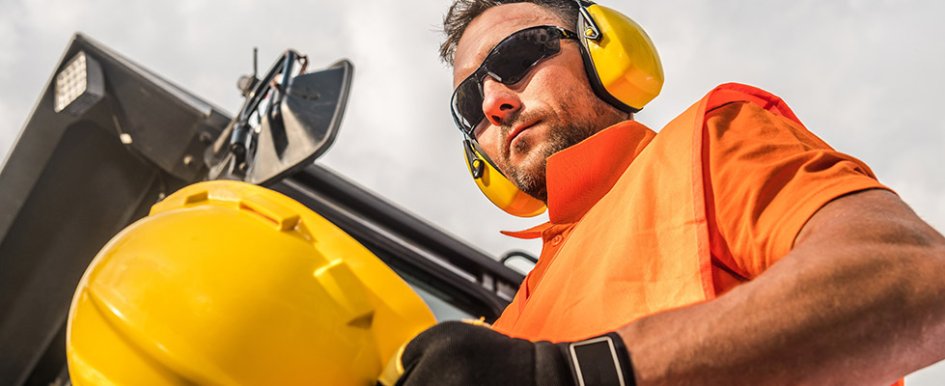
The average construction worker may encounter any number of loud noises during a shift, but just how loud is too loud? Exposure to loud noises — especially over a long period of time — can cause permanent hearing damage, including ringing in the ears and partial hearing loss. Hearing damage, which is irreversible, can limit a worker’s abilities and reduce their overall quality of life. But sounds also help workers orient themselves in the work environment. Reducing sound pollution can help protect everyone’s hearing in the field. Loud noises may be commonplace in the construction industry, but business owners and managers are responsible for protecting workers from sounds that could damage their hearing.
If workers are exposed to more than 85 decibels (db) of sound for eight hours on a time-weighted average, employers must implement safety measures to prevent hearing loss, as required by the Occupational Safety and Health Administration’s (OSHA) occupational noise exposure standard 29 CFR 1910.95. Hearing loss prevention can take many forms. Companies can use quieter equipment, set up sound barriers and ensure workers wear the proper hearing protection, such as earplugs and earmuffs.
Recognize the Risks
No two construction sites are exactly alike. Each project or jobsite presents unique risks and challenges that must be addressed before workers begin their first shift. The management team will need to measure the intensity, duration and frequency of the noises to which workers will be exposed on the job. The intensity is measured in decibels, the duration refers to how long the employee will hear the noise, and the frequency can either be stable, fluctuating, intermittent or impulsive. Managers can use a sound meter to measure the decibel level of these noises based on the worker’s proximity to the sound. According to audiologists, irreversible hearing damage occurs when individuals are exposed to noises at or above 85 db for eight hours or more. The higher the decibel level, the sooner the worker will begin to experience hearing loss. The sound of city traffic alone is at a decibel level of 85, while a lawn mower may clock in at 90 db. Workers only need to be exposed to a lawn mower for 2.5 hours before they could begin to experience hearing loss.
Most of the equipment used in the construction industry is much louder than traffic or lawn mowers. In some cases, a worker may damage their hearing after only a few seconds of exposure. Power tools emit 110 db, and workers can only tolerate 1.5 minutes. Jackhammers and other heavy machinery produce 130 db, and damage can occur in less than one second. If workers exceed the safe noise exposure limit, the company will need to take additional precautions to prevent hearing loss. The best option is to eliminate the loud noises by finding a quieter alternative, such as a newer piece of equipment. Electric motors tend to be quieter than those that run on fossil fuels. Proper equipment maintenance can also help reduce noise pollution. Construction crews should avoid using loud machines whenever possible to limit their effect on workers and the surrounding environment. If this is not an option, the company can set up sound barriers between the worker and the source of the sound or increase the distance between the worker and the source of the sound. For example, workers may be able to remotely pilot equipment to limit their contact with the sound.
Once all these options have been exhausted, the company can use hearing prevention equipment to protect workers. Hearing damage is cumulative. Workers bring a lifetime of noise exposure to the job. A preemployment screening for existing hearing loss may be prudent for those jobs where high-noise environments are expected.
Increase Employee Awareness
Hearing loss prevention requires both teamwork and individual responsibility. Every person occupying the jobsite will need to take precautions to protect their hearing. It’s the company’s job to inform workers of the potential risks and the importance of using hearing loss protection equipment. Managers should post “High Noise Area” signs in and around locations with loud noises.
Workers should receive training on how to use their hearing loss prevention equipment. The instructions may be verbal, written or both. A visual demonstration can help reinforce this information. The training must be available in different languages to accommodate workers of different backgrounds. Workers should feel comfortable coming forward if they have any questions. Workers should also learn to look out for one another on the job. Senior workers could mentor younger workers who may overlook important safety considerations. If a worker notices someone getting too close to a loud sound without proper equipment or lingering in the work area, the worker should remind them to wear appropriate safety gear or leave the jobsite.
Each worker should thoroughly inspect their hearing loss prevention equipment for damage before using it in the field. There shouldn’t be any cracks or tears in the earplugs. Clean plugs regularly to prevent the buildup of bacteria. If they are damaged, they should be disposed of and replaced right away. Every crew should have multiple pairs of earplugs on-site in case a pair is missing or unusable.
The company should continuously review the merits of its hearing loss prevention program to ensure it is doing everything it can to keep workers safe in the field. Managers should always strive to use the best safety equipment for the task at hand to encourage employee compliance. New equipment models may also become available in the future, possibly reducing the need for earplugs and other preventive measures.
Choose the Proper Hearing Loss Protection
Companies have several options when it comes to protecting their hearing. There are different types of earplugs and muffs for virtually every type of situation.
Earmuffs are reusable and long-lasting. They can be worn with a headband, behind the head, under the chin or with a neckband. They can also be mounted onto other safety equipment, such as a hard hat or welding helmet. Earplugs come as two separate plugs. They will either fit into the ear canal or rest just outside it. The plugs are typically made with expandable foam or rubber that will adhere to the exact shape of a person’s ear canal. They can be either reusable or disposable. Both can work well in various applications.
Reusable plugs are made with premolded layers that adjust to the shape of the ear canal. They can also be custom molded for each worker. Reusing plugs will help companies save money over time, but they must be maintained and cleaned after every shift. Disposable plugs must be thrown away at the end of each shift, as the expandable end will only work once. They are a great choice for those visiting the site temporarily, including zoning and safety inspectors, clients and investors.
Managers may want to invest in various types of hearing loss prevention equipment to give their workers multiple options. The earmuffs or plugs should fit comfortably on the person’s head, neck or ear. They should be able to wear them for long periods of time without becoming irritated. Workers should still be able to wear all the necessary safety gear in addition to their earmuffs or plugs. Most earmuffs and plugs come in only one size, but workers should be able to adjust the length of the band for a better fit.
This equipment should be able to withstand the surrounding work environment. It should be able to hold under pressure while repelling sweat, dust, dirt and other airborne debris.
Everyone has the right to work safely without jeopardizing their hearing. Just a few seconds of exposure can lead to a lifetime of poor hearing. Construction teams should keep these considerations in mind when evaluating the potential risks of using loud equipment and machines.